1.8079 Aluminum foil Supplier control of product quality
►8079 Alloy Material Purity
8079 Aluminum Foil Supplier alloy foil should meet specified purity levels according to industry benchmarks. Key elemental impurities can negatively impact formability, printability, and long-term product protection. Request documentation validating purity test results from suppliers being considered.
►8079 Aluminum foil Thickness Consistency
Foil thickness is a critical parameter that needs tight control. Variations in gauge can disrupt processing speeds, cause defects, and compromise the integrity or performance of finished goods. Responsible suppliers implement multi-point measurement protocols on each roll.
►Surface Texture & Integrity
Ideally the foil surface will exhibit a smooth, glossy profile free of blemishes, pinholes, scratches or other defects which hinder further converting operations or mar the appearance of end-use packaging. Inspect sample swatches under magnification if needed.
►8079 Aluminum foil Jumbo Coil Width & Length
Uniformity in these dimensions is important to minimize waste during slitting/sheeting and maximize yield. Reputable suppliers tightly control manufacturing tolerances.
►8079 Aluminum Foil Packaging Quality
Proper packaging prevents damage to Aluminum Foil Supplier in transit. Look for clean, tight winding on corrosion-free cores with no edge creasing or telescoping. Undamaged packaging preserves quality until receipt.
►Batch-to-Batch Consistency
Fluctuating quality adds non-value costs. World-class 8079 Aluminum Foil Supplier deliver consistent gauge, purity and surface properties batch-over-batch through rigorous quality management systems.
►8079 Aluminum foil Certifications & Testing
Food-grade foils require documented conformance to stringent standards. Evaluate suppliers' certifications from accredited organizations and inquire about samples testing programs.
Overall, prioritizing suppliers proven to deliver consistent, high-quality 8079 aluminum foil across all key attributes gives confidence issues will be avoided during downstream conversion and end-use. Thorough quality evaluations set the stage for a productive partnership.
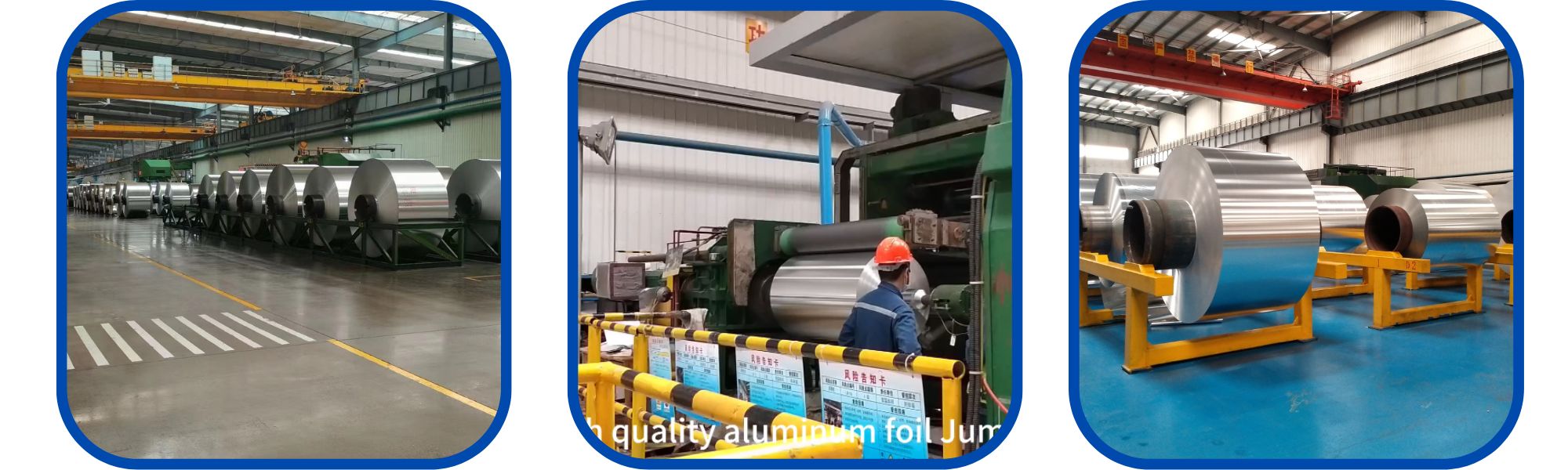
2.8079 Aluminum foil Supplier Reliability & Lead Times
Consistent on-time delivery allows for optimized production planning and inventory management. Evaluate suppliers' logistical competencies:►Order Fulfillment
Assess reported fill rates, quantity tolerances and rates of backorders or delays.
►Available Inventory
Consider average order quantities fulfilled from stock to minimize lead times.
►Warehousing Infrastructure
National or global distribution networks facilitate JIT inventory deployment.
►Shipping Methods
Multiple carrier integrations provide routing redundancy and flexibility.
►Advanced Shipping Notices
Timely communication of order status maintains visibility.
►Purchase Order Integration
Streamlined electronic data interchange accelerates order processing cycles.
►Contingency Planning
Assess disaster recovery protocols and capacity to accommodate surges in demand.
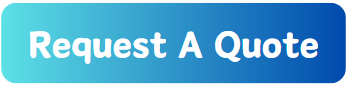
3.8079 Aluminum foil Supplier Production Capacity
Ample capacity supports uninterrupted fulfillment even during seasonal peaks or new product launches. Assess:►Current Manufacturing Capacity
Inquiry determines available slack and ability to ramp up increments quickly.
►Facility Footprint & Layout
Wafer/annealing capacity constraints may necessitate equipment or facility additions.
►Production Planning Flexibility
Ability to expedite or postpone campaigns maintains optimal inventory turns.
►Warehousing Infrastructure
Available square footage impacts maximum consigned stock and throughput.
►Personnel Levels & Staffing Flexibility
Ability to temporarily increase headcount avoids capacity bottlenecks.
►Growth & Expansion Outlook
Capital expenditure plans provide reassurance demand increases can be efficiently met.
Supply chain disruptions prove costly. Suppliers with proven scalability to flex up or down according to fluctuating needs engender most confidence in partnership continuity.
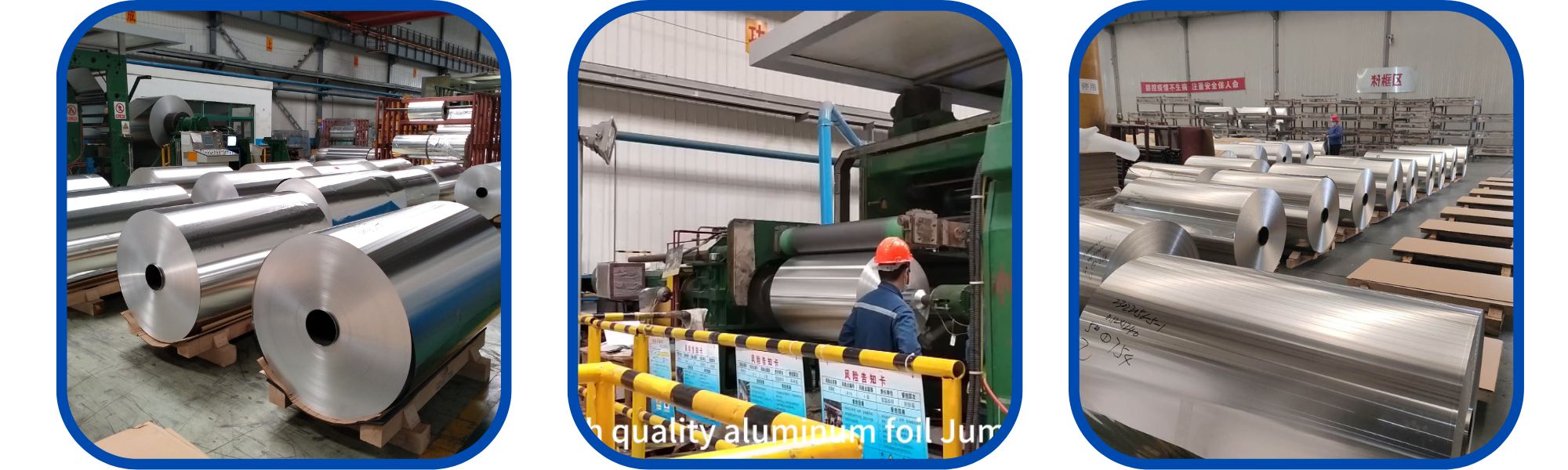
4.8079 Aluminum foil Supplier Customer Support & Relationship Building
8079 Aluminum Foil suppliers cement long-term partnerships through exceptional after-sale support, consulting and continued education including:►Quick reply: HTMM will communicate with customers in a timely manner after receiving the inquiry. 8079 Aluminum foil suppliers will give priority to the response to customers in time, doubt and assistance requests. This helps to build trust and show its commitment to meet customer needs. Use active methods to identify and solve problems.
►Customized service: Understand the needs of each customer and provide effective solutions. The excellent after -sales support revolves around customer satisfaction. We give priority to customer feedback, actively seek methods to improve satisfaction, and constantly adjust their support strategies to meet the development of continuously developing customer needs.