When outmatched demands of strength are called for for minimal materials, 18 micron foil fits the bill. From heavy duty backing foils to reinforced insulated packaging, its high yet lightweight caliber works. Upgrading economically produced, cost saving fund products on jumbo reels. Research explores surface treatments that improve gripping without the need for plastics. Anti-fog properties also benefit medical wrapping applications. As with all aluminum, it is 100% recyclable for a truly sustainable solution.
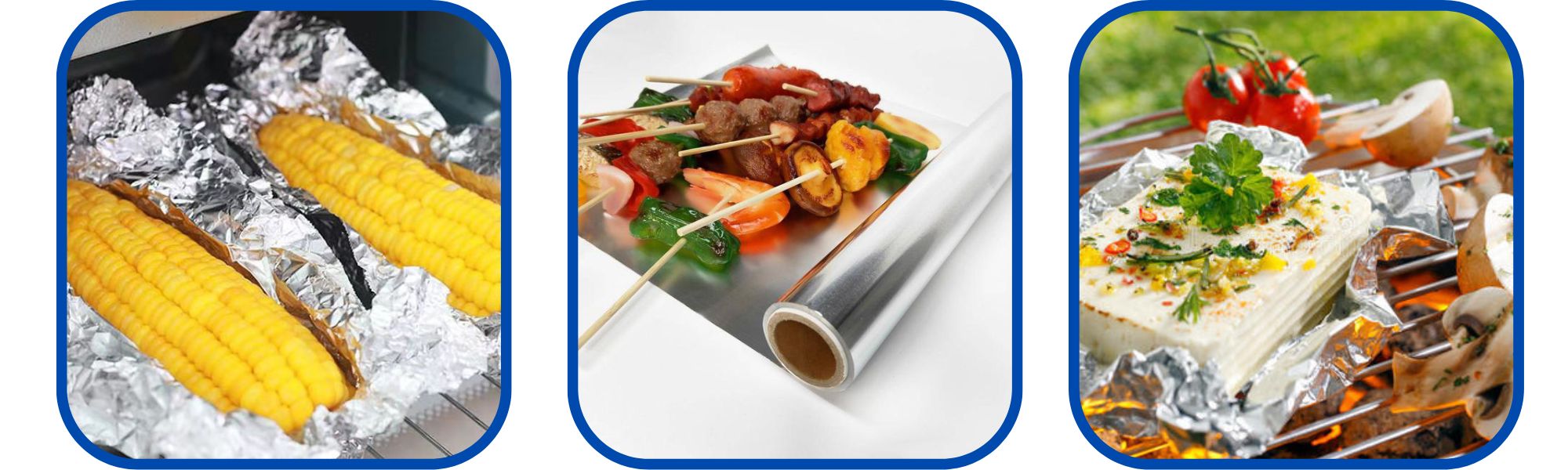
Automotive thermal management similarly exploits the characteristics of aluminum foil 18 micron. It efficiently wicks thermal energy for use in the EV battery envelope. The etched design provides effective light weight to the vehicle structure. The continuous roll maintains the high speed conversion to the rollover section. Building on the innate strength yet renewability of aluminum, further aluminum foil 18 micron developments envision a self-repairing barrier skin that protects against external elements for longevity. Jumbo Roll underpins innovative household products wherever strong foil applications are required.
Producing flawlessly uniform 18 micron foil giant parent reels is critical. This is why process controls use multiple validation techniques. After tension leveling, the laser scans the foils to map any variation in thickness or flatness at microscopic resolution. Thermal imaging additionally analyzes the temperature profile through the foil, detecting abnormalities. The samples are then tested for chemical purity and compound structural integrity by Fourier transform infrared spectroscopy. Only the conforming foil advances to the carefully monitored computer-controlled horizontal winding at set parameters. This multi-check system ensures the highest quality for high-speed production lines.
Adopting this precisely produced 18 micron Aluminum Foil Food Grade Roll Jumbo 8011 format has significant production advantages. Time to form and form equipment increases as less scheduled downtime accommodates huge reel reloads. With higher throughput and minimal wasted material, overall manufacturing costs are notably reduced compared to smaller foil rolls. Regional warehouses consolidate shipments from multiple mills, streamlining logistics. Private label producers have competitive pricing power against major brands. Some savings directly fund innovative projects that introduce traceability systems such as spectral identifiers or nanotagging invisible recycling labeling.
If you are interested Aluminum Foil Food Grade Roll Jumbo 8011 .Please Contact us.
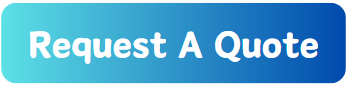
As industry evolves, 18 micron aluminum technology is also advancing to meet changing needs. Researchers test sustainable surface treatments compatible with compostable polymers for renewable food packaging. Applied science also examines nano-additive coatings that can repair microscopic tears or defects to extend shelf life through self-healing mechanisms. If emerging requirements require biodegradability, hybrid material compositions that incorporate compostable components while maintaining the original barrier properties are under development. Overall, the 18 micron aluminum household foil produced on industrial-scale jumbo reels remains essential to its balanced characteristics.
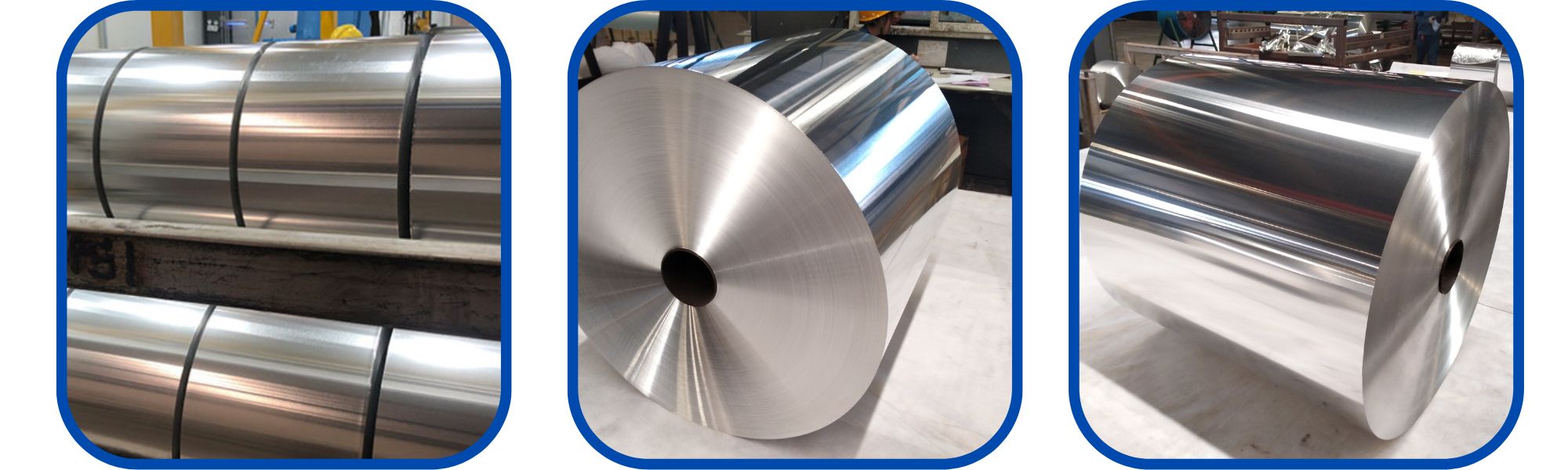
Massive parent reel production of uniform 18-micron Aluminum Foil Food Grade Roll Jumbo 8011 dictates state-of-the-art precision processes. After hot rolling to gauge, computer-controlled leveling equipment applies precisely calibrated pressure gradients to the width and thickness of each foil. This stamps a consistent mood while flattening any imperfections. The foils are then subjected to rigorous inspection using a range of complementary techniques. High-resolution laser profilometry comprehensively maps the entire surface at a microscopic level, detecting even subtle aberrations or flaws. Meanwhile, thermal imaging analyzes temperature uniformity across samples, identifying abnormal regions due to selective trimming. Only qualified aluminum advances to sensitive operation of horizontal winding and slitting in computer-monitored parameters.
The scaling efficiency of 18 micron jumbo rolls creates measurable benefits throughout the household product supply chain. Output on lamination and forming equipment shows a 15-20% increase as changeover intervals between bulk parent reels are reduced. With higher throughput and minimal wasted aluminum, manufacturing costs are significantly reduced versus smaller reel formats. Regional distribution centers consolidate multiple mill shipments, optimizing long-distance logistics. Private label brands gain price competitiveness to challenge the national name. Open Margin sometimes funds next-generation projects that experiment with bio-nanocoatings that provide the self-healing integrity of packaging.
Continuous improvement aims to optimize the sustainable credentials of 18 micron Aluminum Foil Food Grade Roll Jumbo 8011 Alloy. Scientists evaluate surface modification strategies by making aluminum compatible with compostable polymer hybridization, where robustness outweighs the need for ultrathinness, providing viable end-of-life solutions. Biodegradable identifier inks integrated during processing can facilitate industrial compost flows. If the regulatory climate increasingly prioritizes renewal, aluminum is well placed because of the nature of its perpetual recyclability. Overall, industrial-scale roll production maintains an advantageous role for 18-micron foil in the future of affordable, high-performance household essentials.
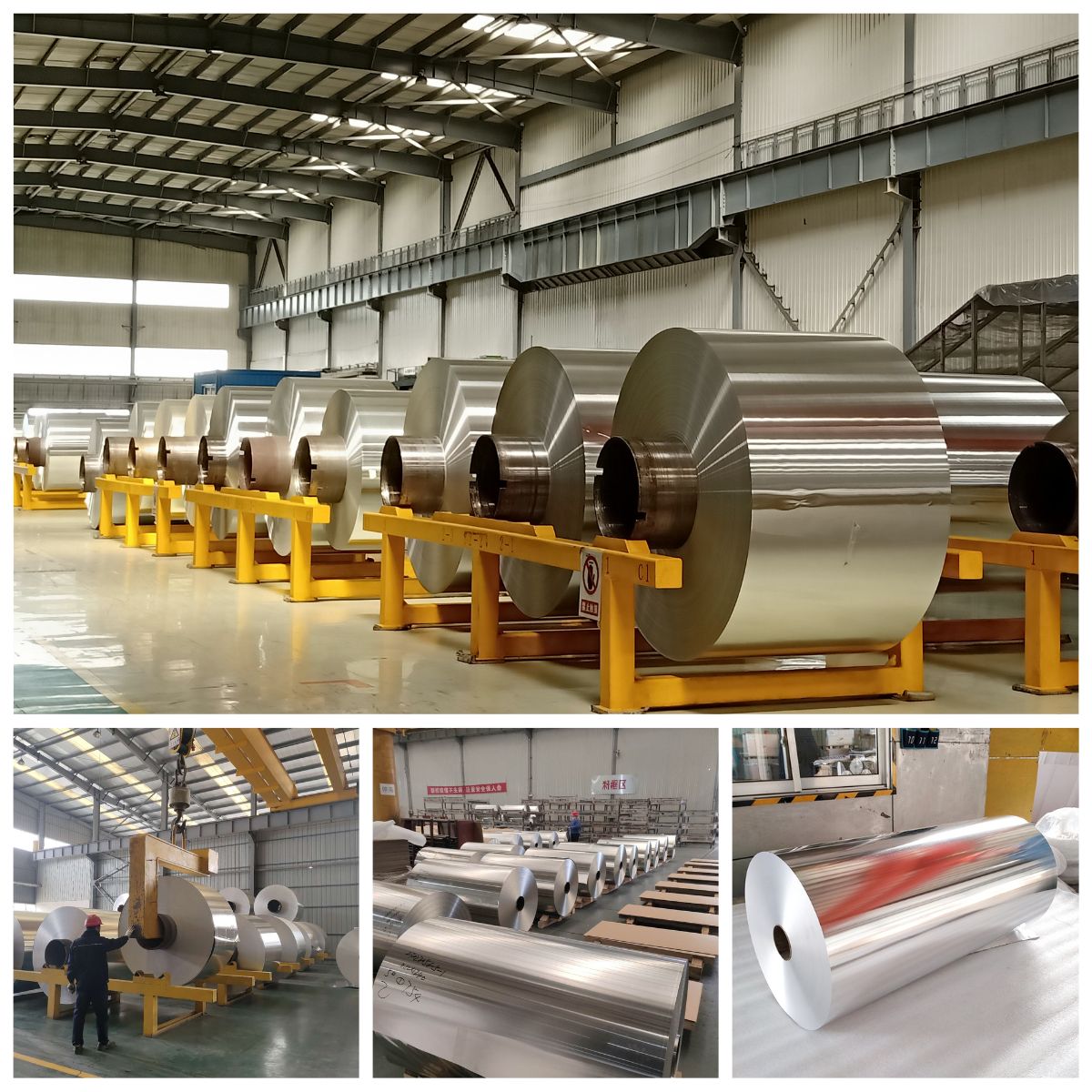
Producing the giant parent reel of 18 micron foil to exacting standards requires sophisticated process engineering. After a tension leveling foil to normalize the temper, the laser executes a microscopic surface scan to map any imperfections, defects or inconsistencies. Meanwhile, the thermal camera analyzes the infrared signature through the sample to identify abnormal areas due to selective trimming prior to slitting. Rigorous characterization via Fourier transform infrared spectroscopy and X-ray fluorescence spectroscopy also validated chemical homogeneity and purity. Only qualified aluminum achieves the sensitivity of computer-guided horizontal windings under strict controls thus minimizing fault accumulation. This multi-check system ensures 18 micron Alu foil performance as required for high-precision production lines.
The scaling provided by the 18 micron Aluminum Foil Food Grade Roll Jumbo 8011 Alloy reaps numerous economic and environmental benefits. Output on downstream equipment increases by 15-20% due to reduced changeover intervals between small format versus bulk parent reels. With higher throughput and reduced wasted aluminum, production costs for all stakeholders decline markedly. Regional distribution centers consolidate multiple mill shipments, streamlining logistics’ carbon footprint. Privately owned brands enjoy pricing parity with nationally recognized names. Margin sometimes funds innovative projects that establish closed-loop recycling identification such as nearly invisible nanotagging or spectral tracing of aluminum sources. Overall, industrial efficiencies from rigorous Aluminum Foil Food Grade Roll Jumbo Good Quality production and continuous improvements in 18 micron Aluminum Foil Food Grade Roll Jumbo Good Quality technology promote more sustainable household essentials worldwide.