The following process capitalizes on the versatility of Printed coated Aluminium Foil. Deep drawings mold tracks into seamless vessels. Laser cutting creates complex venting patterns that allow steam to escape during cooking while maintaining barrier integrity. The coatings researchers developed an oxidation-resistant topcoat with an extended shelf life of up to 5 days at ambient temperature. The partnership with the chefs designed food modules optimizing flavor and nutrition within the tray footprint for 10,000ft altitude. The new casing hints at spice to offset the muted taste experienced in the pressurized cabin.
.jpg)
As markets globalize, the demand for internationally sourced airline meals increases.Coating Aluminium container Foil supports expanded offerings in a sustainably compliant manner. The master relay enables region-specific line conversion by minimizing waste. Their recyclability matches the airport’s renewability mandate. The new surface oxidation barrier technology preserves food through additional distribution center relocations allowing for just-in-time production. Overall, the high-speed formability, barrier and compliance of Coating Aluminium container Foil delivers indulgent quality food worldwide at Avery. single. flight.
Aluminum Foil Coatings Suppliers Producing master reels of lacquer-coated foil consistent at 40 microns . Rolling is followed by rigorous annealing and tension leveling to achieve balanced physical properties. Lasers scan microscopic surface variations and thermal cameras detect irregularities, informing selective trimming for flaw removal. The giant reels then pass through controlled high-speed windings while maintaining dimensional stability. To ensure consistency with feeding lines in excess of 500 trays per minute, the Printed coated aluminium foil mimics the delivery cycle to test durability.
Using master reels streamlines global food production. Regional line conversions take only minutes between the parent reel versus the smaller roll. Scales output to support expansion paths, with 15-20% more throughput. Less waste also means less environmental impact. Now chefs develop previously impossible inspired dishes, such as authentic tandoori chicken elevate the in-flight experience. The new coating withstands distribution transfer, maintaining integrity over the continental journey.
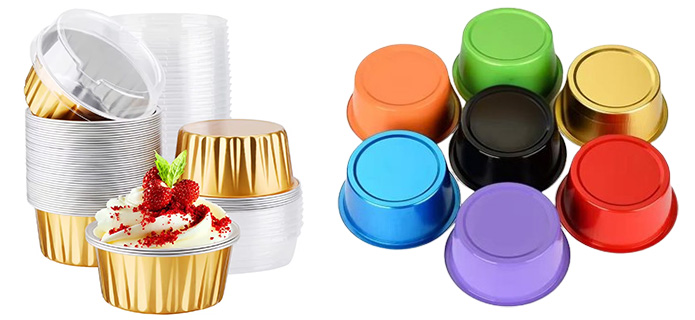
Improvements are aimed at more sustainable stewardship. Bioresin hybrid development can produce compostable structures without compromising functionality. Rare earth substitution verifies the removal of heavy metals from the pigment while retaining opacity and color. If regulations are to be robust, the eternal recyclability of aluminum places them superbly. Overall, the strong yet renewable lacquer foil enables a vision of locally sourced gourmet wellness even at 40,000 feet, connecting cultures across the sky.
Mass parent reel production of compatible foils requires sophisticated process engineering. Lasers scan microscopic surface variations and infrared cameras detect thermal abnormalities through the sheet, informing selective trimming. The thickness is tested under a calibrated pressure of 10 tons using beta-backscatter instrumentation with an accuracy of 5 nm. Only the conforming foil proceeds to tension leveling, providing balanced mechanical properties under computer control. The horizontal winding in modulated parameters then maintains dimensional stability through kilometers of very thin lacquered material.
This precision ensures compatibility with high-speed airline food packaging lines. Operators experience 15-20% increased throughput compared to smaller reel formats, increasing feed volume to serve the expanding global airline network. Regional facilities convert parent reels in just minutes versus transferring between multiple small rolls. Low-waste products can also cut environmental impact. Fund innovations such as intelligent time/temperature indicators that activate when containers are breached to maintain freshness through cost savings.
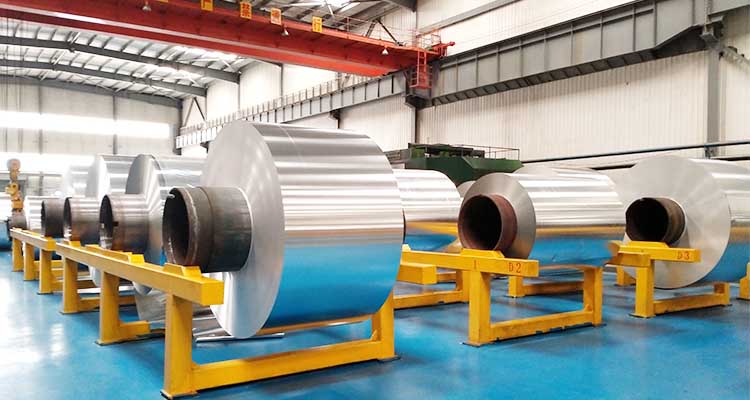
Looking ahead, progress aims to optimize sustainability. Scientists evaluated resin hybridizing lacquer foils with bio-based materials to provide compostable structures where regulations require them. Rare earth substitution research aims to replace heavy metals in pigments without affecting color stability through rigorous testing. The collaborations explore the use of bio-nanocoatings that enable self-healing functionality to maintain integrity throughout critical supply chains. The eternal recyclability of aluminum positions it strongly if policies are to be strong. Overall, the mass production of strong yet renewable lacquer foil promotes in-flight dining worldwide on ever-expanding routes.
Producing the giant parent reel of Lacquer Aluminum Foil to exacting standards requires sophisticated process control. After annealing and leveling the sheets to nano-level flatness, the laser scans the microscopic surfaces across the full width together with FTIR spectroscopy analyzing the chemical homogeneity. Any irregularities are mapped and selectively trimmed before high-precision horizontal windings under harsh environmental conditions. Only fully qualified products proceed to rigorous durability testing, mimicking the intercontinental supply chain cycle.
The scaling advantage of mass reels has a massive impact. For food packagers using automated conversion lines built for jumbo formats, yields increase by 15-20%. The transition time between reels is only minutes versus smaller diameters. Less scrap also reduces the carbon footprint. Cost savings researches intelligent indicators activated by container breakage, maintaining the optimal temperature indicating freshness. Compostable resin innovation targets sustainably compliant structures wherever regulation is strong.
Collaboration makes progress in reusable pack design. The pilot program tests deposit schemes that incentivize passengers to return packaging for industrial cleaning and refilling. Applied research aims to optimize processes and logistics. If the programs scale, the eternal recyclability of aluminum positions it as a superior recyclable material well into the future. Scientists also evaluate surface performance by releasing new antimicrobial properties without compromising barrier function. Overall, rigorous production combined with mass reel supply underpins a globally connected healthy food service that maintains aviation’s role as a catalyst for cultural exchange.
The massive parent reel production of Lacquer Aluminum Foil consistent at 40 microns attracts precise control. After gauging, the tensile layer precisely impresses standard features across the sheets using computer-monitored rollers. The laser then performs extensive microscopic surveys, analyzing individual data points down to sub-nanometer tolerances across kilometer-wide material. Any variance outside the tight specification triggers selective trimming under high-power enhancement. Only qualified Aluminum Foil Coatings Suppliers provide good product.
These systems ensure optimum performance through high-volume airline food assembly lines. Conversion facilities using taller reels than workers experience upwards of 20% accelerated throughput compared to smaller diameter rolls. Fewer changes between such large parent reels translate into higher throughput that meets exponentially growing passenger demand. Manufacturers realize reduced unit costs to fund cutting-edge research that advances sustainability. Pilot programs currently evaluate reusable carton deposit return schemes balancing consumer behavior with optimized industrial recycling logistics through jumbo reel provisioning. Should global reuse scale, the resulting reduced environmental impact will reinforce the essential yet carefully managed role of aviation that connects global travelers to genuine hospitality even at cruising altitude.