Because of its superior barrier qualities, composite aluminum foil is widely used in the packaging business. Because of its moisture barrier, thermal conductivity, and barrier qualities, aluminum foil is frequently used for food packing, cooking, and preservation. It helps food producers keep prices down for packaging without sacrificing product quality. Aluminum foil is used by the pharmaceutical sector to package drugs and medical equipment. Thermal reflecting barriers made of aluminum foil help to minimize heat transmission and energy usage. Because foil is so inexpensive, makers of insulation and HVAC systems may offer economical solutions for industrial, commercial, and residential uses. Aluminum foil is used in the electronics sector for insulation, heat dissipation, and shielding. Superior barrier aluminum foil offers a wide range of advantages to several sectors.
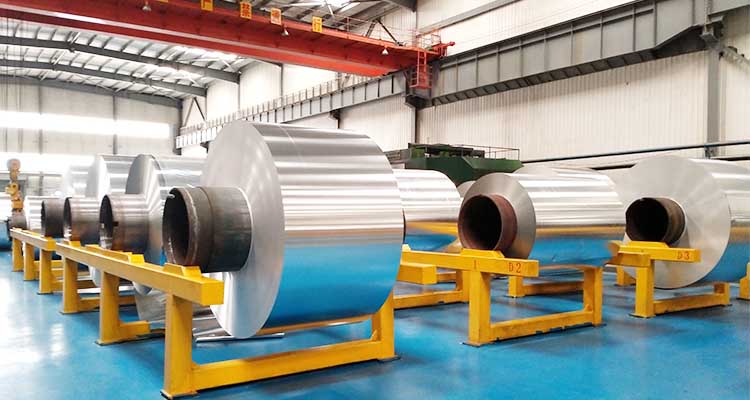
Founded in 2009, HTMM Aluminum has grown into a leading diversified aluminum product manufacturer in China through more than 10 years of development in China and abroad. Composite aluminum foil needs to go through a variety of rolling processes, and has very rich experience in aluminum rolling and processing. Our factory has the most advanced production lines and cutting-edge technology, with an annual total output of more than 80 million tons. We strictly abide by international quality standards such as ISO 9001 to ensure the reliability of our product quality. After receiving the customer's order, our factory will go through aluminum ingot processing, rolling, cooling, annealing, cooling and other processes. In the rolling process, our rolling mill uses HONEYWELL thickness control system and ABB plate control system, which can ensure that the entire rolling process provides customers with different thicknesses of aluminum foil. And for each batch of goods from the customer, we will test the quality of the goods by sampling methods. Our dedicated R&D team is committed to continuous product innovation and customized solutions. Composite aluminum foil, as one of our hot-selling products, has received good reviews from customers.
Property | 8079 Aluminum Foil | 1235 Aluminum Foil |
---|---|---|
Alloy Composition | Contains about 0.7-1.3% Fe and 0.05-0.3% Si | Contains about 0.05-0.15% Fe and 0.05-0.10% Si |
Strength | Higher than 1235 | Lower than 8079 |
Formability | Good | Very good |
Corrosion Resistance | Excellent | Excellent |
Typical Uses | Pharmaceutical packaging, food packaging, battery foil | Household foil, packaging, electrical applications |
Heat Resistance | Good | Moderate |
Workability | Good | Very good |
Surface Finish | Generally bright and shiny | Generally bright and shiny |
Price | Generally higher than 1235 | Generally lower than 8079 |
Tensile Strength | Higher | Lower |
Ductility | Lower than 1235 | Higher than 8079 |

8079 Aluminum Foil is a high-quality alloy that is known for its excellent performance in flexible packaging applications. The elongation of 8079 alloy is better than that of 1235 alloy. Elongation refers to the ability of a material to stretch without breaking. This property makes 8079 more suitable for applications where flexibility and ductility are important, such as packaging material companies mostly use 8079 alloy.
8079 Aluminum Foil is a fantastic choice for preserving perishable goods and delicate items due to its high purity and alloying components, which provide it exceptional barrier characteristics against moisture, light, and gas. The exceptional formability, heat sealing capability, and puncture resistance of this alloy can guarantee the integrity of the contents in the package. The 8079 alloy is well-known for its superior performance and is frequently used in applications that call for strong heat resistance, formability, and barrier protection. This alloy, which is part of the 8000 family of aluminum alloys, is very strong, corrosion resistant, and weldable. Packaging makers typically employ 8079 alloy composite aluminum foil to make yogurt composite packaging and other liquid packaging, such as juice and retort bags;
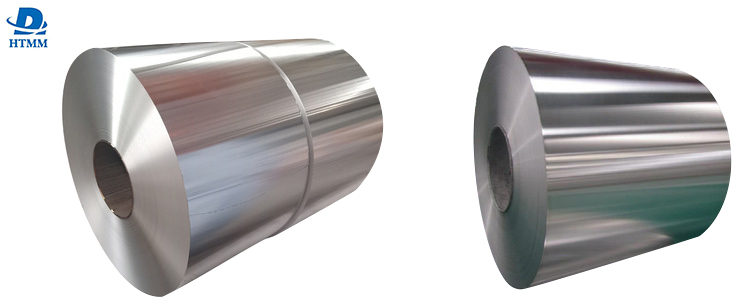
On the other hand, the 1235 alloy has a superior surface quality than the 8079 alloy. Another popular kind of aluminum foil, 1235, is extensively utilized in the packaging sector, particularly for flexible packaging options. 1235 Aluminum Foil is highly regarded for its exceptional performance in heat sealing, printing, and laminating procedures. It is also known for its purity and ductility. This alloy is a great option for packaging consumer items and medications since it is well-known for adhering to stringent food safety rules. This alloy is a member of the 1000 series of aluminum alloys, which are renowned for their electrical conductivity, resistance to corrosion, and adherence to food safety regulations. When producing aluminum paper composite packaging, tobacco packaging, etc., customers frequently use 1235 alloy. and of course, 1235 alloy is also used in the production of liquid packaging.
A crucial ingredient in the creation of flexible packaging materials, aluminum conversion foil serves as a barrier against outside influences that might tarnish the freshness and quality of the packaged items. Aluminum foils 8079 and 1235 are frequently utilized in the production of conversion foils to fulfill a range of requirements in the packaging sector. These foils are made to maintain the best possible product appearance, stop contamination, and increase product shelf life.
The use of aluminum foil in flexible packaging has revolutionized the way products are packaged, stored, and shipped. Aluminum foil is a top choice for manufacturers seeking reliable and sustainable packaging solutions due to its light weight, strong heat-seal ability and resistance to external factors. The versatility of 8079 and 1235 aluminum foils in flexible packaging highlights their importance in maintaining product integrity and meeting consumer demands for convenience and freshness. One important application for composite aluminum foil is lamination. Due to its soft and smooth surface, foil can be easily bonded to other substrates through wet or dry lamination processes. Common laminates include paper-aluminum-paper sandwiches (PAP), aluminum-polymer-aluminum composites and foil-film laminates. The foil layer provides an effective moisture and grease barrier as well as decorative functions to the final laminated product such as food packaging, household packaging, pouches and other packaging films.
When contrasting aluminum foils 8079 and 1235 for use in flexible packaging, a few significant distinctions become apparent. 8079 foil's improved strength and barrier qualities are a result of its alloy composition, which qualifies it for uses requiring robust defense against outside influences. On the other hand, 1235 foil is a great option for packaging that needs intricate graphics and branding features because of its ductility and compatibility with printing techniques.
Additionally, while 1235 foil's thermal conductivity enables effective heat transmission during the sealing process, maximizing production efficiency, 8079 foil's heat-sealing capabilities guarantees the safe closing and preservation of packed items. These foils demonstrate their versatility in flexible packaging solutions with their superior moisture barrier, light blocking performance, and adaptability to different package shapes.
In conclusion, choosing the best aluminum conversion foil material for flexible packaging applications requires a grasp of the distinctions between aluminum foils 8079 and 1235. While 1235 foil excels in ductility and printability to fulfill the industry's broad packaging needs, 8079 foil offers great barrier characteristics and strength. In order to fulfill customer expectations for convenience, sustainability, and product protection, manufacturers may improve the quality, attractiveness, and usefulness of their flexible packaging solutions by utilizing the distinctive qualities of each foil.