The flexible packaging industry has seen tremendous growth in recent years as more consumer products migrate to lightweight, portable and peel-away packaging formats. A key enabler of packaging innovation has been advancements in ultra-thin metal Converter Foil, with aluminum emerging as a promising material for these applications. Converter Foil as thin as 6 microns are now making new designs possible while providing processing and sustainability advantages over traditional materials.
What is Converter Foil?
Converter foil serves as a substrate coating that can be printed, laminated or otherwise decorated to impart functional properties to a packaging film. In flexible packaging, this typically involves bonding an aluminum, paper or plastic layer to films made of materials like polyethylene, polypropylene or polyester.
Flexible packaging Aluminum Foil acts as a barrier to moisture, gases, light and flavors while also enabling printing and metallization. It "converts" an ordinary film into a high-performance packaging structure. Flexible packaging aluminum foil in the 9-12 micron range have long been standard, but 6 micron foil expands the possibilities.
Brand Name | 6 Micron Converter Foil 1235 For Flexible Packaging |
Material | 1235 |
Temper | 0 |
Thickness | 0.006mm ( 6 Micron ) |
Width | 200-1500 mm |
Coil ID | 76、152 mm |
Coil Weight | 350-500 kg |
MOQ | 5 ton |
Payment | 30% deposit in advance,the balance against B/L copy. 100% irrevocable L/C |
Advantages of 6 Micron Aluminum Foil Jumbo Roll
Thinner gauges of aluminum bring noteworthy benefits compared to conventional foil weights:
Increased Packaging Efficiency - Downgauging to 6 micron aluminum foil jumbo roll allows more product and liners to be packed into the same shipment volume, lowering transport costs.
Higher Functional Properties - At only 1235 aluminum foil jumbo roll, aluminum provides superior barrier with hardly any thickness penalty. This supports growing demand for extended shelf-life foods.
Improved Sustainability Profile - Less aluminum material is extracted, manufactured and disposed of per package unit. Overall lifecycle impacts like emissions are reduced.
Enhanced Optical Properties - Six micron metallization delivers brilliant, high-fidelity printing with a silky-smooth appearance much like paper or plastic.
Superior Forming Capabilities - Ultra-thin 1235 aluminum foil jumbo roll is highly flexible, formable and printable for complex package shapes like stand-up pouches with precise edges.
Higher Speed Processing - Thinner gauges allow faster line speeds in lamination, printing, slitting and other converting operations with less risk of web breaks.
While Aluminum foil 6 micron presents more handling and processing intricacies than thicker Aluminum foil 6 micron, its technical and economic advantages have spurred flexible packaging makers to invest in working with material this thin.
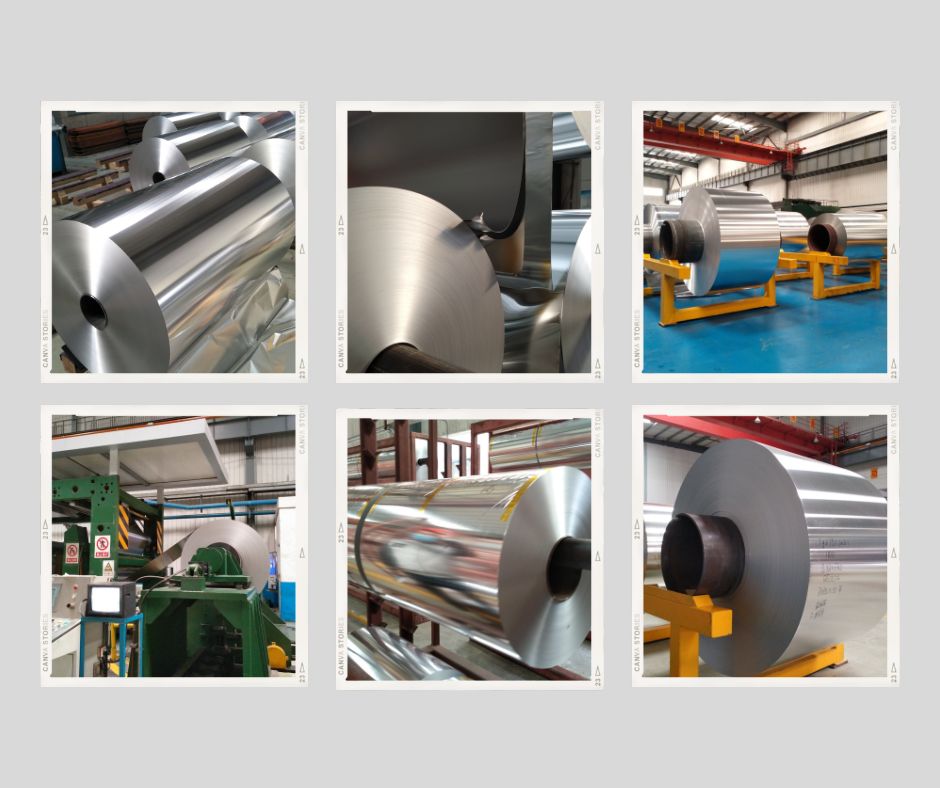
Lamination Considerations for 6 Micron Foil
Transitioning packaging films from conventional weights like 10-12 microns to 6 micron aluminum requires refinements to the lamination process:
Adhesion Promoter Systems - Ensuring optimal bond strength between such an ultra-thin foil and various polymer films calls for promoter chemistries verified for 6 micron performance.
Film and Foil Cleaning - Any residual contamination, even on the microscopic level, could lead to defects. Aggressive cleaning protocols must remove all trace contaminants.
Press Calibration - Pressure, temperature, dwell time and cooling rates all require precise tuning to overcome stresses inherent to working with material this lightweight.
Wrinkle Prevention - Special attention is needed to eliminate any unevenness that could compromise appearance, barrier or convertibility downstream.
Optimal Roll Tension - Proper unwind and rewind tensions must be established to prevent breaks or thickness variations across huge reels.
Real-Time Process Monitoring - Sensors provide data to refine lamination profiles ensuring consistent 6 micron bonding across entire wide web widths.
Automation and Integration - Fully connected machinery minimizes manual handling susceptibility to static, dust or scratches during transfer between steps.
With validation testing, optimized lamination processes for 6 micron converter foils are now delivering promising results around defect reduction, yield improvement and line efficiency.
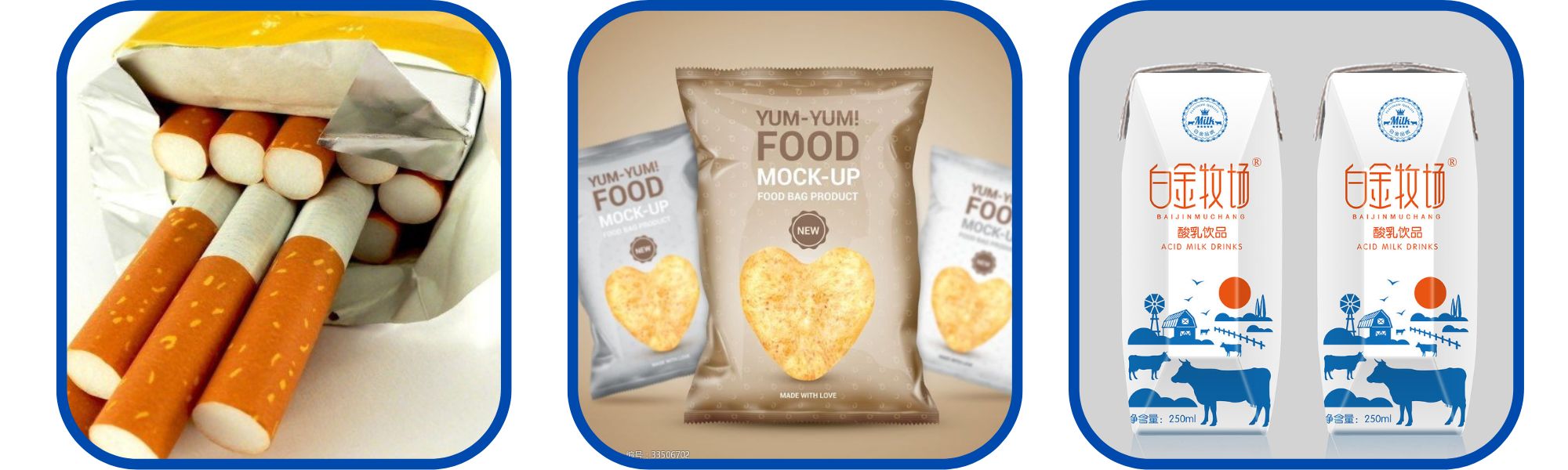
Further Opportunities of 6 Micron Technology
As familiarity grows with ultra-thin 6 micron aluminum lamination, new pathwaysmay open for flexible packaging innovation:
Novel Film Structures - Multilayer buildups with ultra-thin aluminum or metal/polymer composite layers could enable sophisticated packaging functions.
Precision Pattern coating - Roll-to-roll imprinting or selective metallization processes create intricate patterns for enhanced graphics, consumer interaction or product tracking/authentication.
Improved Recyclability - At 6 microns, aluminum forms a far thinner recyclable component of multi-material laminates compared to traditional thicknesses.
Active/Intelligent Packaging - Ultra-barriers and printed electronics using 6 micron platforms may enable indicators, timers or sensors to provide information on product quality and integrity.
New Design Dimensions - Forming complex geometries with 6 micron foil allows for clamshells, folding cartons and other formats beyond pouches to blossom.
With further refining, 6 micron converter foil may ultimately enable more sustainable, feature-rich and economically viable packaging constructions than previous generation materials. Its adoption continues to expand across global markets.
In summary, the 6 micron thickness breakthrough provides numerous technical and commercial drivers for increased utilization of aluminum foil in flexible packaging applications. As a foundational material, its continued advancement bodes well for evolving the entire packaging industry towards higher performance standards.
Packaging plays an important role in preserving food and other products while also protecting them from external factors like moisture, oxygen, and microorganisms. Flexible packaging is widely used for food, consumer goods, medical supplies and other applications due to advantages like low cost, light weight, and the ability to take on various shapes. Metallized films enable flexible packaging materials to provide protection from factors like oxygen and moisture. Specifically, 6 micron converter foil 1235 has become an important metallized film for flexible packaging applications.
What is Converter Foil 1235?
Converter foil 1235 is a 6 micron aluminum foil that is coated on one side with a thin layer of polyethylene. The polyethylene coating enables the aluminum foil to be bonded or laminated to flexible packaging substrates like films, papers, and foils using coating, lamination, or extrusion processes. The polyethylene barrier coating prevents interaction between the reactive aluminum and packaging substrates or inks. It provides excellent adhesion for lamination and extrusion coatings.
The 6 micron (0.00000236 inches or 0.00006 mm) aluminum foil core provides barrier attributes to block gases like oxygen and moisture as well as light. This thin yet effective foil allows for packaging films to remain flexible while gaining enhanced barrier properties. The 1235 designates this particular converter foil as having a gauge of 0.00006 mm (6 microns) of aluminum with a 0.05 mil (1.27 micron) coating of low density polyethylene (LDPE) on one side.
Applications in Flexible Packaging
Converter foil 1235 has found widespread use in food, medical and various consumer packaging applications due to advantages like flexibility, barrier properties and cost effectiveness. Some key applications include:
Snack food packaging - Potato chips, crackers, cookies and other snacks benefit from the moisture and oxygen barrier of converter foil 1235 laminated packaging films and foils to extend freshness.
Fresh meat packaging - Converter foil provides an effective oxygen and moisture barrier to retain color and extend shelf life of packaged fresh and processed meats.
Cheese packaging - The foil helps block oxygen to maintain quality and prevent rancidity in packaged cheeses.
Liquid packaging - Converter foil can be laminated to films for aseptic and non-aseptic packaging of juices, milk, sauces and other liquid foods.
Pharmaceutical blister packs - Blister packs for medicines, supplements and medical supplies take advantage of the barrier properties of foil laminated films and foils.
Cosmetic packaging - Pouches, stick packs and other packages for creams, lotions and potions use foil laminates for extended shelf life.
Tobacco packaging - Foil is commonly used in packaging for cigarettes, cigars and other tobacco products.
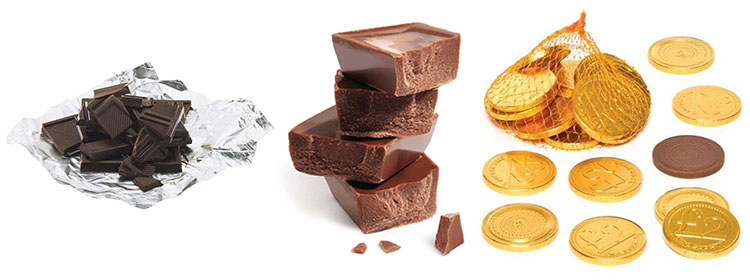
Benefits Over Uncoated Foil
There are some key advantages that the PE coated 6 micron foil (converter foil 1235) has over uncoated aluminum foil for flexible packaging applications:
Compatibility - The PE coating allows direct bonding to polymer packaging substrates like films and papers using existing coating, laminating and extrusion equipment without delamination issues. Uncoated foil needs a bonding layer.
Printability - The smooth PE surface works well with printing inks compared to the rough uncoated foil surface, allowing for colorful graphics and labeling.
Flexibility - The ultra thin 6 micron foil with PE keeps packaging film flexible rather than becoming stiff like uncoated foil lamination. This is important for form fill seal processes.
Barrier - While uncoated foil provides strong gas and moisture blocking, the PE coating adds an excellent low permeability barrier layer without compromising the overall high barrier attributes.
Adhesion - PE tightly bonds foil to substrates rather than relying on an adhesive layer. This ensures long term adhesion without risk of delamination over packaging life.
Producing Converter Foil 1235
Converter foil 1235 is produced through a series of coating and laminating processes. High purity aluminum is first cold rolled into ultra thin foil blanks. These blanks are then continuously coated on one side with a thin layer of melted low density polyethylene using roller coating equipment.
After the peel coated foil exits the nip rolls, the two layers quickly bond and set as the PE coating cools and solidifies. A corona treatment may be applied to the PE coated side to enhance surface energy for adhesive bonding.
Quality control checks ensure the foil gauge is closely maintained at 6 microns and the uniform PE coating thickness meets specifications, usually about 1 micron. The foil is then wound onto large rolls for shipping to packaging film and laminate producers. There it is bonded to polymer films or foils through processes like extrusion, dry bond lamination and wet laminating adhesives.
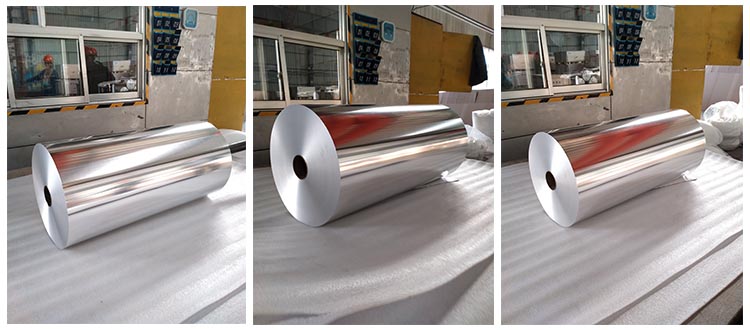
Sustainability Considerations
Use of thinner 6 micron foil with its performance and cost benefits has led flexible packaging to use less material overall compared to alternatives like rigid packaging. However, sustainability efforts focus on increasing recycled content and ensuring aluminum foil packaging is designed for maximum recyclability at end of product life.
Key sustainability strategies for 6 micron converter foil 1235 and the packaging films it enhances include:
Curbing use of virgin aluminum through increased recycling
Designing packaging to separate aluminum foil for recycling after use
Use of renewable energy and reducing emissions in aluminum production
Developing mono-material flexible packaging for improved recycling
Lifecycle analyses comparing environmental impacts to alternative packaging
Education promoting post-consumer recycling and waste reduction
Conclusion
Ultra thin 6 micron aluminum converter foil 1235 with its polyethylene coating has become widely used in flexible packaging applications to deliver effective moisture, oxygen and light barriers at low cost. Key attributes like compatibility, printability, and flexibility along with strong gas and moisture blocking properties make it preferable to uncoated foil for applications in food, medical, tobacco and various consumer packaging. Ongoing innovation continues to advance the sustainability profile of aluminum foil flexible packaging.