Chocolate packaging foil roll is one of the most widely used materials in homes and industry around the world. Its lightweight yet durable qualities make it perfect for wrapping, baking, cleaning and more. Today chocolate packaging foil roll is taken for granted on kitchen counters, but its development and rise to ubiquity tell a fascinating story. This article will explore the history of chocolate packaging foil roll production, innovations that expanded its applications, and how it transformed formerly labor-intensive tasks into simple one-step solutions. Special focus will be given to chocolate luxury wrapping foil's enduring role as the premier material for luxury chocolate wrapping and packaging.
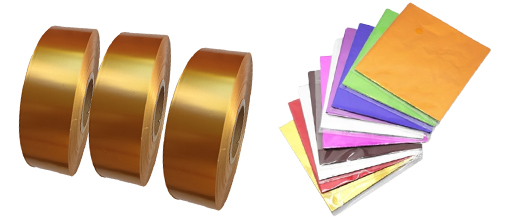
The Early Years of Aluminum Foil
Aluminum Foil in its natural bauxite ore state has been utilized for centuries to produce pottery glazes and other materials. However, extracting pure aluminum metal from bauxite proved exceptionally difficult and expensive prior to the late 19th century. The key development enabling mass aluminum production was the Hall–Héroult process which electrolytically separates the metal from ore. When patents for this process expired in 1886, firms launched major aluminum smelting operations.
Early aluminum sheets and chocolate luxury wrapping foil were produced by casting or rolling ingots into thin gauges. The exceptionally malleable quality of pure aluminum allowed precision milling not possible with other metals. However, raw aluminum oxidized quickly, requiring protective coatings to prevent deterioration. As production expanded in the 1910s-20s, manufacturers experimented with lacquers, waxes and oil treatments to stabilize chocolate aluminium foil for emerging applications.
An important breakthrough came in 1912 when Alcoa developed a secondary rolling process enabling ultra-thin foil gauges as low as 0.0045 inches thick. This “foil mill” successfully mass-produced lightweight yet sturdy sheets suitable for wrapping without tearing or puncturing. Advances in anodizing and other finishes stabilized raw aluminum ensuring its shelf life for commercial and household use. By the 1920s, the chocolate aluminium foil era was underway.
Original Uses of Chocolate Packaging Foil
Among the earliest major applications of lightweight chocolate packaging foil was cigarette packaging starting in the late 1910s. Prior to foil, tobacco companies used waxed or laminated papers which did not seal as securely or simply. Foil's moisture barrier properties also helped extend cigarette freshness. Aluminum wrappings for spices, cosmetics and medications followed as manufacturers recognized foil's preservation abilities. Food producers likewise adopted foil as an excellent barrier against moisture, oxygen and light compared to other materials.
In the critical post-World War II era, aluminum emerged as a strategic material for its lightness, production capacity and anticorrosive benefits. As production surged, household uses proliferated spurred by marketing focused on hygiene, convenience and thrift. Foil quickly became a kitchen workhorse for cooking, storing leftovers, scrubbing pots and baking due to its ability to shape easily while resisting heat and wear. While early aluminum utensils tarnished concerns, durable foil overcame these issues revolutionizing common tasks.
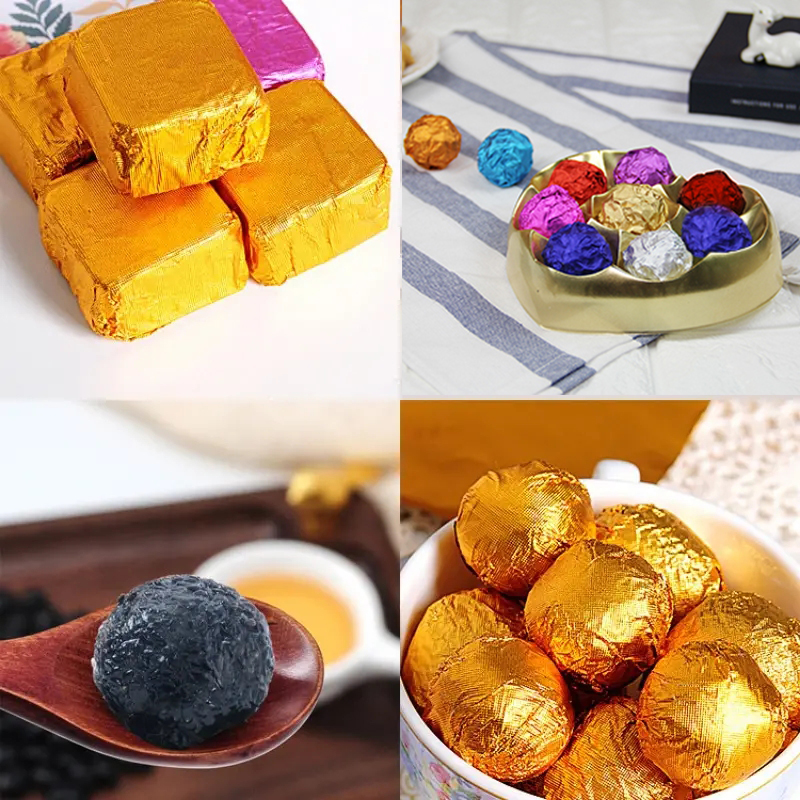
Rise of Foil as a Luxury Chocolate Wrap
Significantly, aluminum foil helped elevate perceptions of premium chocolate candies in the emerging consumer culture. In the 1920s, luxury European brands like Godiva, Lindt and Neuhaus adopted lightweight foil as the optimal high-end wrap and presentation material. Precisely formed foil cups, trays and ribbons beautifully displayed chocolates for gifting while maintaining freshness. Its mirror shine associated luxury compared to papers prone to smudging or dulling. By World War II, premium chocolate was near exclusively wrapped in foil sheets printed with brand iconography.
The postwar years saw foil quality and designs rapidly improve through lithography, stamping and embossing. Holiday foils printed with festive motifs maintained premium perceptions year-round. Meanwhile, industrial developments like the first roll-to-roll process and thinner gauges reduced costs, enabling branded foil wraps for drugstore chocolates. By the 1960s, even basic candy bars relied on foil's shelf impact, establishing it as the standard chocolate wrapper globally. Today, opulent foil-wrapping remains signature of high-end bars and bonbons seeking to elevate a consumable luxury experience.
Contemporary Uses of Aluminum Foil
While foil applications have evolved, it remains ubiquitous in kitchens worldwide for its unique thermal conductivity, lightweight moldability and barrier properties superior to plastics for many tasks. Here are some leading modern uses:
Food preparation - Foil is integral to grilling, baking, roasting and simmering dishes. Its ability to shape into pans and protect surfaces from flames, spatters and grease makes it irreplaceable.
Storage - Considered the optimal wrap for sealing in freshness of leftovers, cheeses, sandwiches and more due to its complete moisture and gas barrier. Crucial for protecting chocolate, baked goods and other snacks.
Cleaning - Heavy-duty duty foil powers scouring of pots, pans and ovens without scratching or retaining odors like sponges. Also ideal for carving tools needing flexible backings.
Crafts and gifts - Creative projects rely on foil for molding, crimping, stamping, embossing and coloring in artworks, flowers, bows and uniquely wrapped presents.
Luxury wrapping - High-gloss foil remains the gold standard for premium chocolate and confectionery brands seeking to convey craft, artistry and indulgence through bespoke sheets.
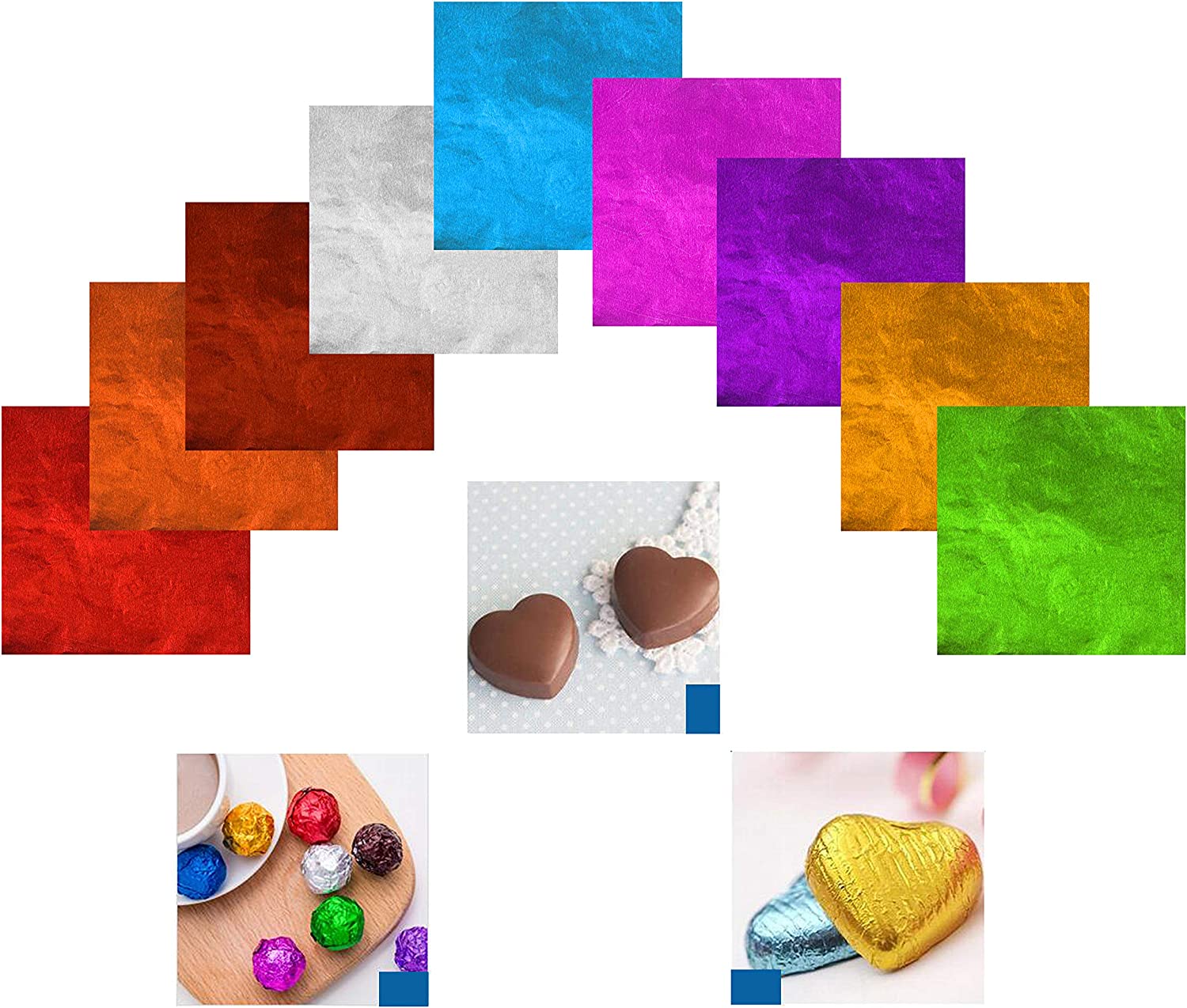
Sustainability Measures
While aluminum production requires extensive energy, manufacturers focus on sustainability. Many foils contain post-consumer recycled scrap which requires 90% less energy versus primary aluminum. New certified compostable foil options use sugarcane or potato starch barriers. Producers prioritize reduced thickness, downgauging to minimal necessary levels.
Compared to single-use plastics, foil efficiently recycles multiple times with minimal quality loss into new foil, cans and other semipermanent goods. Many municipalities accept foil as a lightweight yet valuable scrap. Major companies advocate recycling programs and consumer education ensuring foil does not end up in landfills. Considering aluminum's infinite recyclability and versatility aluminum foil remains an eco-friendly workhorse material for discerning households and industries alike.
The Future of Aluminum Foil
Looking ahead, new applications, alloys and production methods will expand foil's indispensable role. Areas of development include:
andards worldwide.