Seamless aluminum foil refers to a continuous roll of aluminum foil without seams or seams, which ensures uniform thickness and quality throughout the roll. This feature is essential for applications that require high standards, such as lamination processes in the packaging and food industries. The lack of seams minimizes the risk of defects and ensures consistent performance, making it the first choice for food packaging manufacturers.
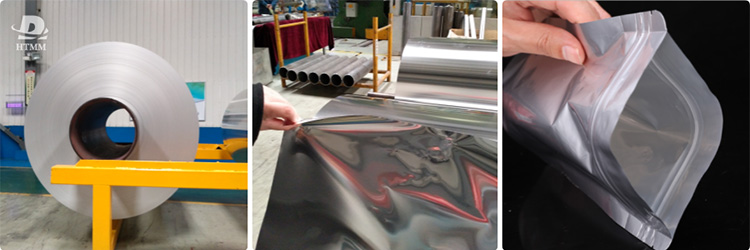
The advantages of choosing seamless laminated foil are: One of the main advantages of using seamless aluminum foil is the consistent thickness of the entire roll of aluminum foil. This uniformity is essential for applications that require precise measurement, such as in food packaging, where barrier properties need to be reliable. The continuity of seamless aluminum foil provides excellent barrier properties to moisture, light and oxygen. This is particularly important in flexible packaging, where product quality is critical. Seams in the foil can lead to weak points, which can compromise the integrity of the packaging. Using seamless foil reduces the risk of such defects, ensuring that the final product meets high quality standards.
1235 refers to an alloy of aluminum foil with an aluminum purity of 99%, mainly made of aluminum (Al) and small amounts of other elements such as iron (Fe) and silicon (Si). The 7-micron composites used in HTMM plants are mostly 1235 alloys, which are widely used in various applications, including flexible packaging and lamination. It contains at least 99.35% aluminum, so it has high plasticity and ductility. Of course, we can also provide customers with 8079 alloy and 8011 alloy composite aluminum foil for lamination. 8011 aluminum alloy has higher tensile strength and better corrosion resistance, making it suitable for applications that require higher strength and corrosion resistance. On the other hand, 8079 aluminum alloy has higher elongation and flexibility, making it an ideal choice for applications where formability, ductility and excellent barrier properties are critical.
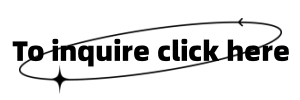
1235 Aluminum foil has high reflectivity, making it ideal for thermal insulation applications. It reflects heat and light, which is very beneficial for packaging solutions that require temperature control. This type of aluminum foil has excellent moisture, gas, and odor barrier properties, making it ideal for food packaging, such as snack bags, pouches, and wraps. Its barrier properties make it ideal for packaging food, extending shelf life, and maintaining freshness. When customers need aluminum foil for liquid packaging (Tetra Pak type packaging), 1235 alloy is a good choice. Due to its reflective properties, it is often used in the industrial field to insulate products to improve thermal performance.
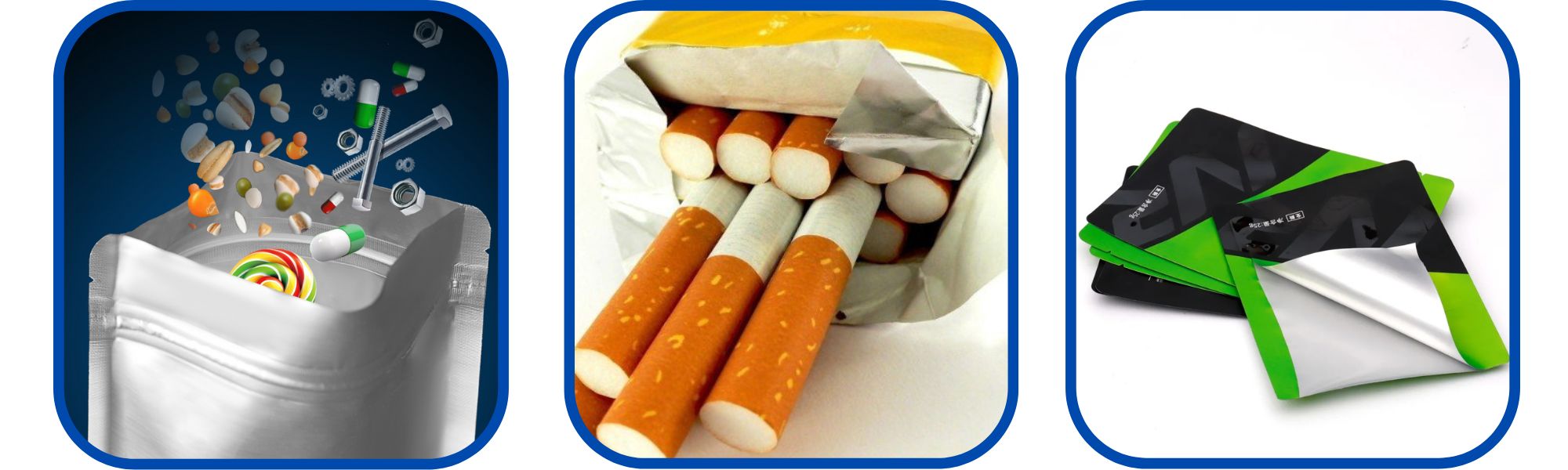
7 Micron aluminum foil refers to foil with a thickness of 7 microns (approximately 0.007 mm). Due to its thin thickness, this thickness is often used for flexible packaging. Although 7 micron aluminum foil is thin, it still maintains a high tensile strength, making it suitable for a variety of packaging applications.
This thickness has excellent moisture and gas barrier properties, making it ideal for food packaging that needs to maintain flavor and freshness. Thinner foils (such as 7 microns) are usually more expensive than thicker foils because this requires aluminum foil 7 micron manufacturers to have good production technology quality control and will also require more raw material consumption to provide a yield rate. After receiving the customer's order, the HTMM factory will go through the processes of aluminum ingot processing, rolling, cooling, annealing, cooling, etc. In the rolling process, our rolling mill uses HONEYWELL thickness control system and ABB plate control system to ensure that the entire rolling process provides customers with different thicknesses of aluminum foil. Regular third-party laboratory tests verify that our laminated aluminum foil meets international food grade standards. Dedicated quality inspectors monitor defects, thickness consistency and alloy purity of each batch of products. Our (HTMM) factory has third-party quality inspection certificates such as Europe, the United States, SVHC, etc. These certificates can prove that our aluminum foil can be well contacted with food and our aluminum foil quality is fully in line with good food grade aluminum foil.
Aluminum foil for flexible packaging includes a series of foils designed for flexible packaging applications. This type of foil is characterized by thinness, flexibility and excellent barrier properties. For example, aluminum foil used for food packaging usually has a thickness range of 7~12mic. Aluminum foil for flexible packaging can be easily adapted to various shapes and sizes for a wide range of products. Effectively protecting the contents from moisture, air and light is essential to maintain product quality, which is why aluminum foil has become indispensable in the food packaging field. Common laminates include paper-aluminum-paper sandwich (PAP), aluminum-polymer-aluminum composites and foil film laminates. The foil layer provides an effective moisture and grease barrier as well as decorative functions to the final laminated product such as food packaging, household packaging, pouches and other packaging films. While there are many benefits to laminating aluminum foil rolls, certain safety precautions must be considered. Aluminum foil should not come in direct contact with acidic or salty foods as this can cause a chemical reaction that results in aluminum transfer to the food. To avoid this, it is recommended to use a barrier such as parchment paper when cooking or storing such foods.
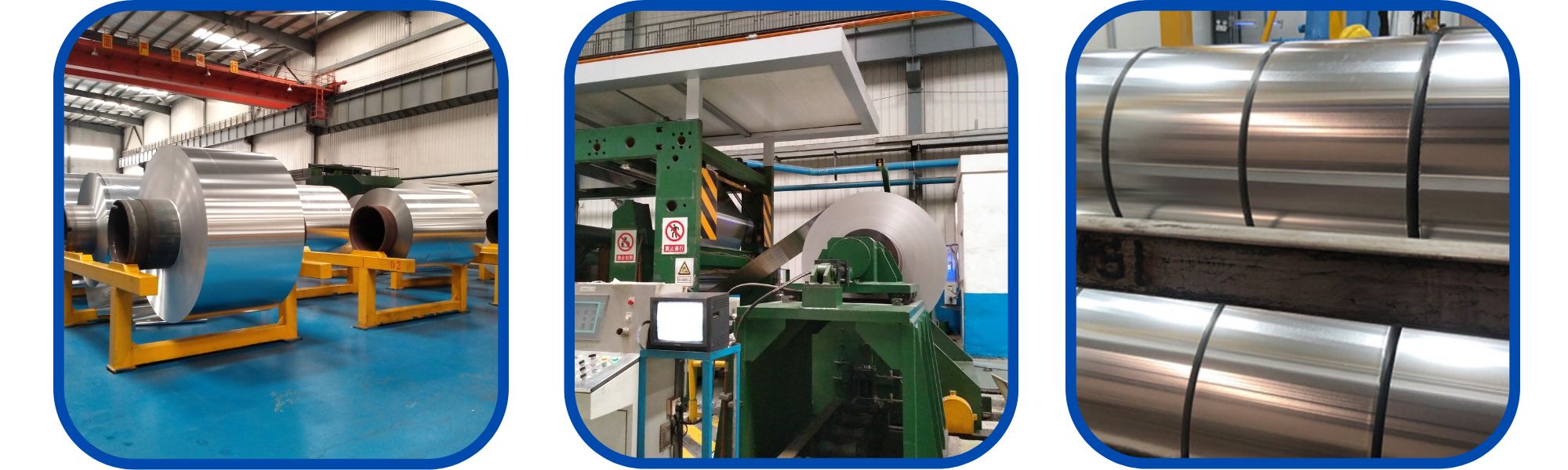
Seamless roll aluminum foil is a must-have material for lamination purposes, especially in flexible packaging applications. With types such as 1235 aluminum foil, 7 micron aluminum foil and aluminum foil dedicated for flexible packaging, manufacturers can ensure the production of high-quality, reliable and beautiful products. The benefits of using seamless aluminum foil include consistent thickness, enhanced barrier properties and reduced risk of defects, making it a preferred choice for various industries. As the demand for high-performance packaging continues to grow, aluminum foil will continue to be a key material to meet the needs of manufacturers and consumers.