What are the benefits of 1235 aluminum foil 7 Micron?
At its core, the 7µ aluminum foil acts as a superior barrier within the flexible packaging structure. It blocks contaminants such as oxygen, moisture, grease and oil from harmful products while retaining freshness characteristics such as fragrance and nutrients. The non-corrosive nature of 7µ Al foil also protects against chemical interactions. Its high reflectivity helps regulate temperature, maintaining steady state for product safety and durability. In addition, state-of-the-art aluminum metallurgy has produced 7µ-even alloys with enhanced properties such as enhanced formability or barriers as well as barriers compared to standard 7 microns aluminum foil.Leading Aluminum foil suppliers develop 7µ Alu foil into usable components through additional modifications such as printing, treatment and compositing. This prepares the aluminum for its specific end use while maintaining its barrier efficiency. They validate products that meet demanding regulatory requirements for food contact and consumer safety. Qualified 7μ Alu foil enables innovative, high-performance and sustainable flexible packaging solutions through technical support in the value chain. Overall, the ultra-thin 7 microns aluminum foil offers unparalleled barrier benefits that boost both product and packaging lines.
Advanced metallurgy continues to favor 1235 aluminum foil. New alloys with minerals such as silicon produce highly structured grades that laminate easily without cracking to create a perfectly smooth surface. The addition of trace graphene creates a self-healing coating while maintaining integrity over the packaging life cycle. The electrolytic thin film deposition applies a thick but highly effective functional polymer coating of only a few molecules. Such innovations maximize the benefits of 1235 aluminum foil while using less raw material.
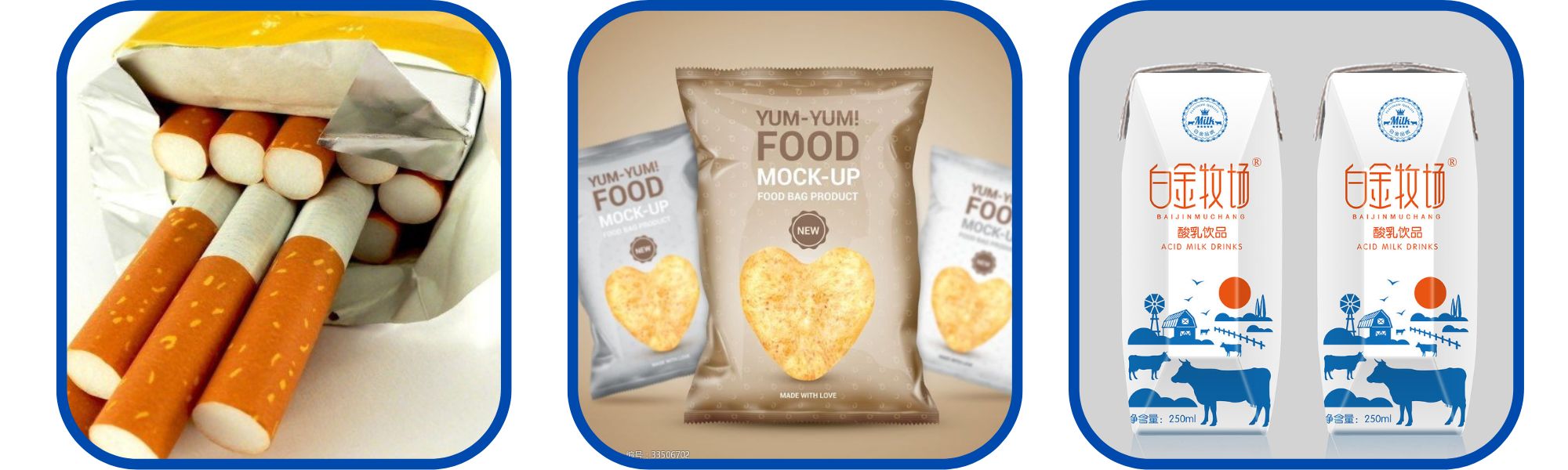
Leading Aluminium Foil manufacturers are subject to stringent certification regimes. ISO 9001 ensures consistent processes that meet customer requirements. FSSC 22000 validates hygienic practices for food contact applications. Supply chains comply with GFSI standards such as the SQF, which examines social and environmental standards. On-site quality labs perform extensive testing at each stage validating the alu foil 7 micron composition, barrier characteristics and regulatory compliance to ensure performance.
Industry 4.0 technology digitally optimizes alu foil 7 micron production. Automated fault detection through Ai reduces waste. The I4.0 machine controls variables such as thickness and coating weight with great precision. Digitally networked manufacturing and quality systems capture big data insights that lead to continuous improvement. Real-time process monitoring enables rapid corrective actions to maximize uptime and productivity.
Collaborative R&D accelerates beneficial innovation. Cross-industry partnerships leverage combined expertise to solve shared packaging challenges. University alliances cultivate the next generation of aluminum scientists. The open innovation crowdsourcing platform leads to new 7µ foil solutions from different perspectives. The joint research centers expedite the piloting of high-impact sustainability enabling technologies.
Overall, advanced aluminum foil for flexible packaging components paired with responsible manufacturing sustain packaging innovation. Strategic commodity stewardship future-proofs the role of this vital substrate in supporting global food security, consumer wellness and supply chain resilience.
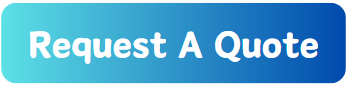
Testing new materials and laminate structures is critical for validating performance. Aluminium foil Manufacturers undergo rigorous lab testing that mimics real-world distribution cycles. The samples undergo thermal shock, vibration, shrinkage and chemical contact testing to identify any weaknesses such as delamination or barrier breakage. Partneringpackaging engineers subject prototype pouches and other formats to durability tests such as drop tests and impact resistance quantification. The Quality Manager additionally oversees the validation of regulatory compliance through analytical evaluation. This extensive vetting procedure ensures that only the highest performing 7µ Al foil innovations reach the market.
Sustainability remains a key driver of aluminum foil for flexible packaging development. Scientists explore bio-based or compostable polymer blends that enable single-component structures for improved recyclability. The digitally optimized ‘jigsaw piece’ laminate design optimizes product yield by reducing foil gramage. Nano-additive coated 7µ Alu foil shows promise in replacing virgin with recycled materials. Energy managers curb greenhouse gas emissions by transitioning production to renewable sources. Discussions with end-of-life stakeholders inform a more circular product design strategy. Overall, a balanced multi-approach to 7µ Alu foil innovation promotes both performance and environmental stewardship by supporting global packaging needs now and well into the future.

7 Micron Aluminium Foil is a Good lamination Grade Raw Materials
Advanced coating techniques maximize the potential of 7µ Aluminum foil laminates. The barrier resin nano-coating, which is only one hundredth of a micron thick, provides highly effective moisture and gas protection comparable to thick plastic. Printed micro-embossing imbues tactile textures that help users open packages while preserving an ultra-smooth surface ideal for high-speed lamination. Photocatalytic and antimicrobial additions to the coating extend product shelf life by neutralizing contaminants. The continuous development of new coating materials and precisely controlled deposition expands the functional properties that 7µ Al foil brings to flexible packaging.
Digital prototyping virtualizes design and testing processes, accelerating innovation. FEA simulations subject virtual 7µ Alu foil laminate structures to a myriad of stresses, evaluating performance prior to physical prototyping. Multi-parametric modeling optimizes material specifications and processing parameters. AR/VR visualization improves collaboration among global stakeholders. The digital twin of the production line evaluates the efficiency impact from new products to refine uptime. Machine learning algorithms comb datasets to predict faults and schedule maintenance earlier, maximizing equipment lifecycle.
As environmental and social governance mandates tighten, leading 7µ Aluminum foil suppliers are actively pioneering responsibly engineered solutions. Cross-laminate designs integrate recycled material at a higher rate than mono-materials. Zero-waste manufacturing techniques re-enter all scrap and by-products into the process. Sustainable source and renewable energy powering facilities receive rigorous third-party certification validating ESG best practices. The Community Assistance Program strengthens local circular economies by recycling flexible packaging. Strict stewardship enables resource-efficient innovation for global health and prosperity by safeguarding the future of 7μ Alu foil.
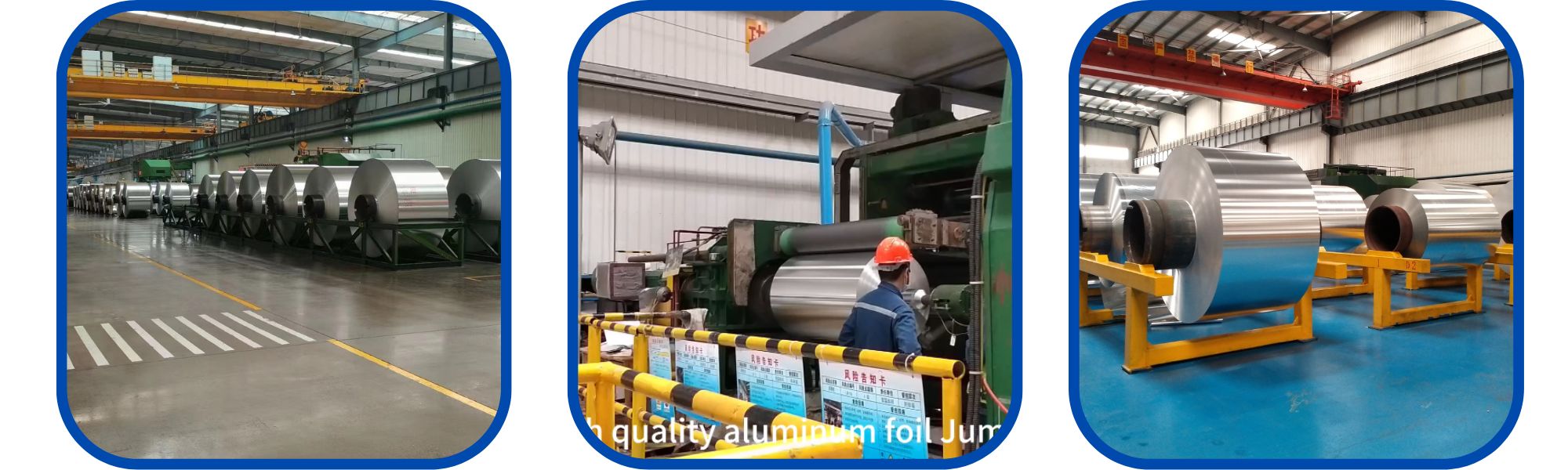
Advances in materials research are exploring new frontiers for ultrathin 7 micron aluminum foil laminate applications. Biomimicry evaluates naturally occurring smart materials such as butterfly wings or beetle cocoons for the inspiration of next generation functional development. For example, structural color inventions can provide color effects without ink to help consumers identify content. Research on stimulus-responsive foils investigates changes in shape memory behavior or selective permeability from triggers such as temperature, pH or electromagnetic waves. This could enable applications such as active food freshness indicators or packaging that selectively "breathe" the environment favorable to the item. In addition, new manufacturing methods on the horizon such as molecular metal deposition can manufacture 7 micron Alu foils with complex three-dimensional nanostructures over large areas to maximize properties such as gas and aroma barriers using less material. Cutting edge fundamental investigations in physics will certainly reveal additional ways to optimize performance both for packaging and beyond. The sustainability assessment will guide the commercialization of these innovations to support global megatrends in health, access and environmental protection.