Sophisticated unwinding and winding apparatus is required to precisely guide such vast meshes of extremely thin foil. The tension must remain consistent throughout the width to prevent errors. Temperature differences are carefully controlled and edge trimming maintains dimensional consistency. X-ray inspection verifies integrity. The resulting huge rolls, weighing several tons, are then transported on custom-built reels and shafts.
Downstream converting operations also realized major efficiencies from ALUMINIUM foil Jambo reels. Continuous laminators, packaging machines and thermoformers stretch standard widths without interruption, reducing changeover times. Manufacturers benefit from increased productivity and product yields. Operating costs are lower when waste and inventory are reduced. Substantial savings are passed on to end users in industries such as food and pharma where aluminum foil plays a key role.
Ongoing research further optimizes the jumbo reel process. New lubricants and coatings improve handling of extra wide gauge variations. The automated system speeds up quality checks and edge trimming. Some mills experiment by laminating multiple foils simultaneously to multiply the productivity boost. Partnerships with OEMs customize unwinds and slitters for maximum performance.
Overall, Jumbo Relay established a new paradigm for aluminum foil production and conversion. Their introduction reaped maximum benefits throughout the value chain. And continued innovation targeting wider parent rolls or rapid change will strengthen the competitiveness and versatility of aluminum foil for developing markets demanding higher performing barrier products. Jumbo reels make this niche difficult.
Jumbo rolls of aluminum foil typically range from 200 or 1500mm in width. This huge width allows for a significant increase in efficiency by maximizing the amount of material wound on a roll. By condensing the foil into very wide rolls that are later torn into narrow widths suitable for packaging and other conversion lines, logistical and operational advantages are achieved.
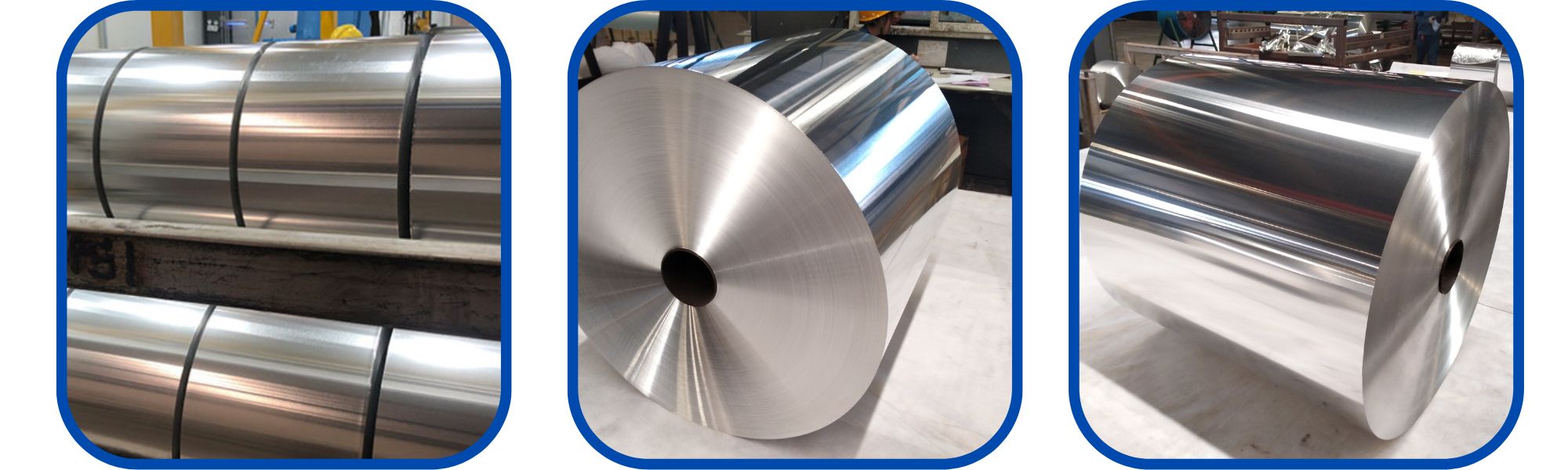
The sheer size of the 1,000m-wide jumbo roll creates new challenges throughout the production process. Special heavy-duty winding and slitting machinery with expanded width parameters must be used. Temperature, tension and layer shrinkage must be strictly controlled through the entire roll diameter to ensure uniform and defect-free quality in the Aluminum Foil Large Rolls For Food Grade. Transporting and handling the massive roll, which can weigh several tons, also requires stable reels and shafts designed for wider and heavier rolls.
Once the width, length, and thickness of the 8011 Aluminum Foil Large Rolls are known, the total area of the foil on the roll must first be determined to calculate the diameter of the roll. The width of the foil is given simply, and the length refers to how much foil is wound on the roll. To get the total area, you multiply the width by the length. Then using the thickness you can calculate the volume of the aluminum by multiplying the area by the thickness.
Now that you have the total volume of the aluminum wound on your roll, you can use it to calculate the required diameter. First, assume that the foil is rolled into a perfect cylinder around the central core. Then use the formula for the volume of a cylinder: V = πr^2h. In this case, the height 'h' is just the thickness of the foil, so change that value in . You want to solve for the radius 'r', and you already know the volume. Plug in all the values and solve the equation for r to obtain the radius of the roll.
Once you calculate the radius, you can also easily convert it to the diameter of the roll by multiplying the radius by 2. Material, make sure it will all fit the width of the supplied roll without being too loose or tight.
Aluminum Foil Large Rolls For Food Grade designed for direct food contact requires the highest purity standards. The 8011 grade designation indicates that the foil is manufactured from aluminum that meets all FCC and international structure specifications for safety in culinary applications. When wound into five-metre-wide jumbo rolls, 8011’s purity and durability ensure its suitability for rapid packaging and food service equipment requiring nonstop production.
Strict process control is required to produce flaw-free 8011 ALUMINIUM foil Jambo reels. Sophisticated winding devices precisely guide the ultra-thin foil, maintaining uniform thickness and mechanical properties across vast widths. Sophisticated quality checks between each production step identify any blemishes for removal to protect the continuous running time of the downstream equipment. The result is that huge rolls weighing up to five tons provide thousands of hours of material for thermoformers, leading machines and other lines running day and night.
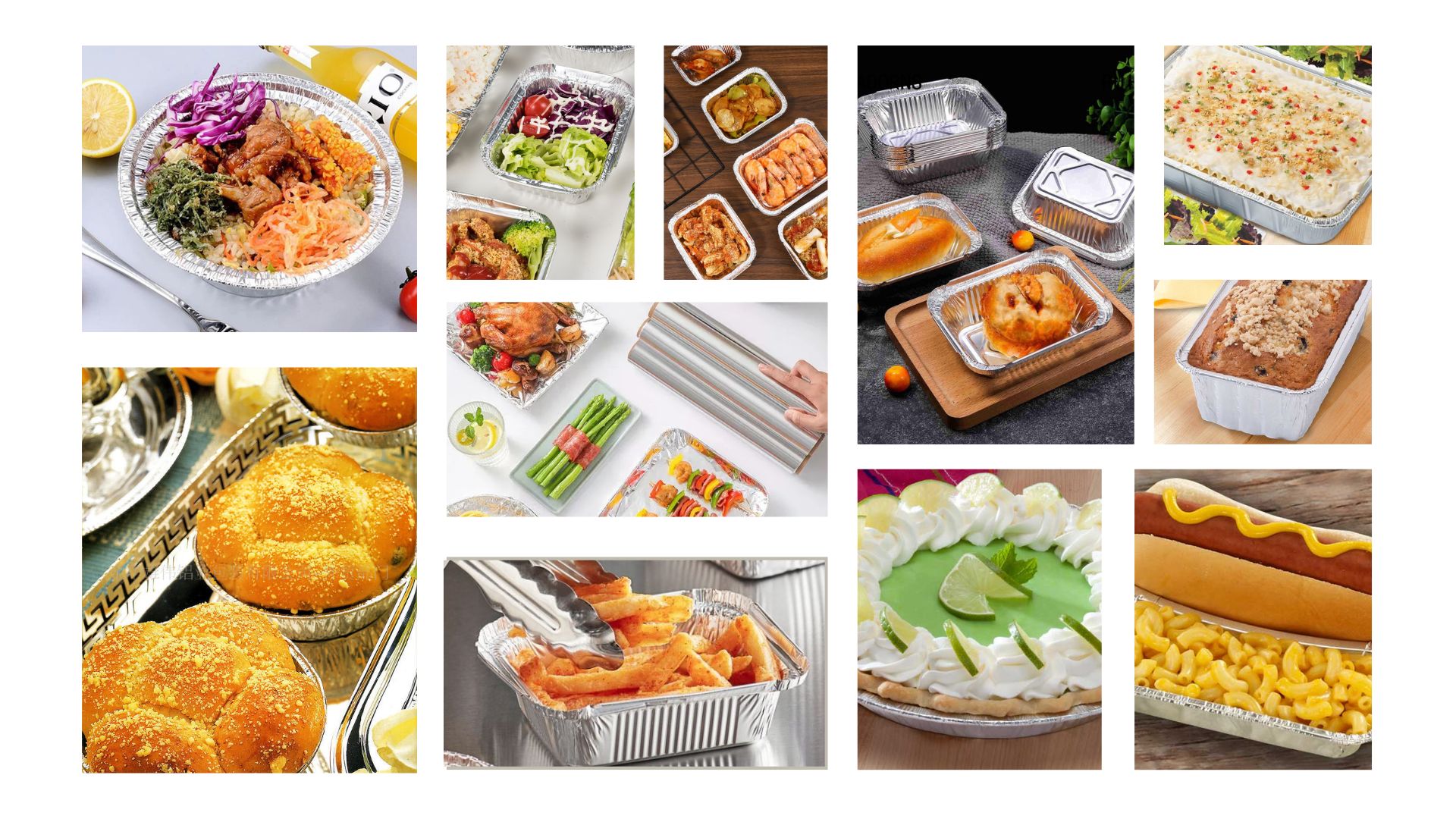
The immense size of the 8011 ALUMINIUM foil Jambo reels maximizes handling efficiency. Minimal downtime is required to reload the parent reels for equipment replacement. Combined with the production of more products that reduce waste, manufacturing costs are significantly reduced. Regional distributors further streamline logistics by consolidating multiple customer orders into a single truckload. Bakers, manufacturers and food service operations gain a competitive advantage through an assured supply of the highest purity 8011 8011 Aluminum Foil Large Rolls approved for direct contact culinary applications.
Meeting the stringent purity specifications required by global food safety regulators is no small task, but critical for Aluminum Foil 8011 For Jumbo Rolls intended for food contact applications. The supply chain is carefully controlled through multi-stage refining and rolling from the source of the raw metal. Production lots undergo rigorous testing in independent laboratories, including ICP-MS analysis that detects trace elements and tissue culture assays that evaluate cytotoxicity. Only foils that meet all criteria qualify for the 8011 jumbo roll format which ensures consistent, premium quality.
Operations using 8011 ALUMINIUM foil Jambo reels benefit from much higher product yields than smaller standard reels. Continuous form-fill-seal lines realize 15-20% increased output. Leading machines report 10% more speed over 10,000 hours of running time than conventional reels. Batch bakeries benefit from larger press mold tin runs or extended sheet pan production windows. Regional warewashers consolidate loads for caterers and food trucks, redirecting cost savings into the local economy.
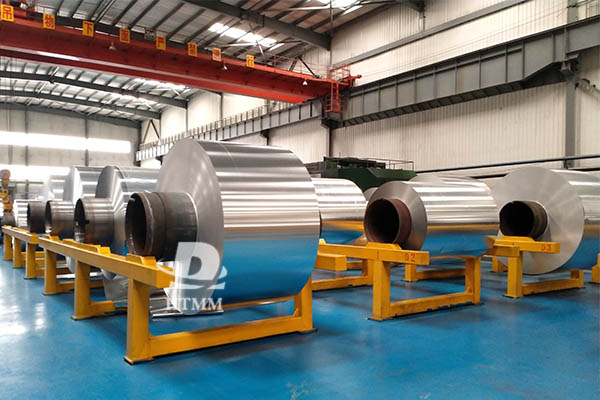
As food production demand evolves, R&D further enhances the multiplicity of Food Grade Aluminum Foil 8011 Roll Jumbo. Surface treatment increases thermal resistance for extended retort processing. Laser etching tests customization without sacrificing barrier features. Future 8011 innovations may explore antimicrobial properties or controlled-release antioxidant evoked nanoparticles that maintain shelf life. Regardless, ultra-pure Food Grade Aluminum Foil 8011 Roll Jumbo remains the gold standard for applications that require long-term, flaw-free contact with consumables.