8011 aluminum foil roll have been utilized for many construction and insulation purposes for decades. One use that is growing in popularity is employing 8011 aluminum foil roll specifically for roof insulation applications. While traditionally roof insulation has utilized fiberglass blankets, cellulose, or spray foam, 8011 aluminum foil roll insulation brings a number of advantages to the table. This article will explore in-depth how 14 micron aluminum foil rolls can be used effectively for roof insulation, comparing 14 micron aluminum foil to other common insulation materials, detailing installation techniques, and outlining the main benefits it provides.
What is aluminum foil for roof ?
Aluminum foil for roof is a type of aluminum used commonly for foil production. It has a thickness of 0.014mm or 14 microns. This ultra-thin gauge makes it lightweight and flexible, allowing it to conform easily to uneven surfaces. 8011 aluminum also has a superior ability to reflect solar radiation, with an emissivity rate between 0.03 to 0.05. This means aluminum foil for insulation reflects over 95% of radiant heat.
Beyond roof applications, aluminum foil for insulation is frequently employed as household foil for cooking and wrapping food. It's also used for thermal management in vehicle and aircraft manufacturing. As building wrap, it can provide an air and vapor barrier. For roof insulation specifically, its ultra-thin yet highly reflective nature is well-suited. Aluminum foil rolls are inexpensive to produce at scale and have an extremely long shelf life when protected from damage or moisture.
How does aluminum foil insulation work?
The insulating properties of aluminum foil work through two mechanisms: reflection and conduction. When infrared and visible light rays from the sun hit an aluminum foil surface, the vast majority of that radiation is reflected away rather than being absorbed. Some is also transmitted through the foil. This reflective ability is what contributes most to aluminum foil's high R-value as a thermal insulator.
The other factor is that aluminum foil is an excellent conductor of heat. However, its ultra-thinness means there is very little bulk or mass to conduct heat through. Heat that does manage to pass through the foil layer dissipates quickly thanks to its narrow width. The small air gaps that exist when aluminum foil is installed also help slow conductive heat transfer.
Combined, the high reflectivity and conduction properties of aluminum foil make it akin to multiple air gaps stacked together as an insulator. By reflecting sunlight and preventing it from being absorbed and transferred into the roof structure beneath, aluminum foil roll insulation provides an extremely effective thermal barrier.
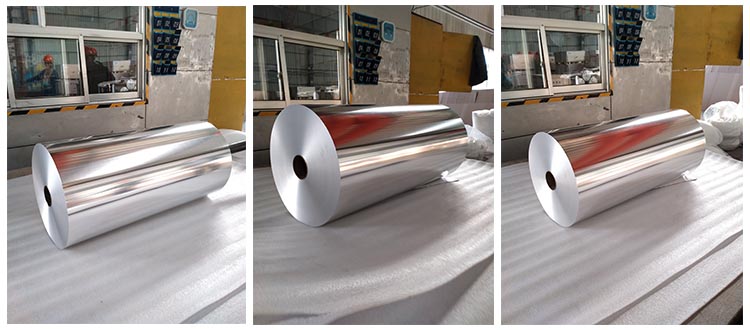
Foil Rolls For Roof Insulation
There are a few key factors to consider when selecting the right 8011 aluminum foil rolls for roof insulation applications:
Thickness - For roofing, stick with true 8011 aluminum foil rated at 0.00093 inches thick. Thinner gauges risk damage, while thicker foil loses some reflectivity.
Width - Most common widths are 48, 60, or 96 inches to match standard roof decking. Narrower rolls may require more seams.
Texture - Choose either a crumpled or wrinkled texture for improved drapability over uneven surfaces. Smooth foil can ripple more easily.
Packaging - Foil insulation should be packaged in tear-resistant bags or boxes to prevent damage before and during installation.
Cost - Price per square foot of coverage is generally low for aluminum foil. Compare various manufacturers and roll dimensions.
Reflectivity - Aim for emissivity ratings below 0.05 for maximum heat deflection ability.
With the right aluminum foil gauge, width, texture, and packaging for the job, the material can be easily installed for superior roof insulation.
Common uses of 8011 aluminum foil rolls for roof insulation
There are a few primary ways that 8011 aluminum foil rolls are employed as roof insulation:
Underlayment - Installed underneath roof shingles, shakes, tiles, or standing seam metal panels. Acts as a secondary water barrier and additional thermal break.
Cavity liner - Laid in attics or over roof decks before installing fiberglass batts or spray foam. Reflects radiant heat back through the roof plane.
Single-ply roofing - Used as a vapor barrier and insulation combined under TPO, PVC, or EPDM membrane roofing systems.
Metal buildings - Provides a cost-effective thermal barrier under corrugated steel, aluminum, or copper roof panels.
Low-slope applications - Effective R-value on commercial flat or low-pitched roofs subject to heat gain.
Retrofits - Can upgrade outdated or degraded fiberglass insulation in existing roofs structures.
By fitting between roofing materials and decks or within attic cavities, aluminum foil rolls block heat transfer into living spaces beneath.
Installation of 8011 aluminum foil roof insulation
Proper installation techniques are important to achieve the full reflective benefits of aluminum foil roof insulation. Generally, the process involves:
Preparation - Ensure decking is dry, clean and smooth before installation. Foam fill imperfections.
Unroll foil - Extend fabric downward if applicable to prevent convective air movement.
Seam taping - Use reinforced tape rated for aluminum at all joints and seams. Tape liberally.
Securing edges - Adhere perimeter edges to prevent wind lift and seal edges.
Cavity installation - Unroll horizontally with 6" overlaps in attic bays. Tape seams.
Underlayment application - Adhere directly above deck, overlap shingle edges. Tuck beneath.
Inspect for gaps - Check full coverage is achieved without holes after installation.
Proceed with roofing - Apply final roofing materials over foil directly afterwards.
Proper seaming and taping is crucial. The foil should lay flat and taut without creases that reduce reflectivity. Adequate securing prevents movement over time as well. With care taken during application, aluminum foil delivers optimal insulating performance.
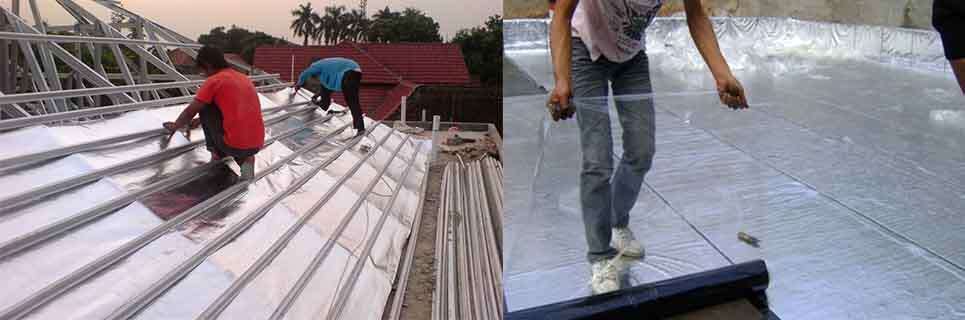
Benefits of aluminum foil roof insulation
There are numerous advantages that aluminum foil roll roof insulation provides over traditional fiberglass and other common insulation materials:
Reduced cooling costs - By reflecting 95% of radiant heat, foil keeps interior roof surfaces and attics much cooler. This directly lowers air conditioning bills.
Higher R-values - A single layer of aluminum foil has an R-value around R-3. Multiple layered has R-values exceeding R-6 per inch. Fiberglass only achieves R-3 at 1.5 inches.
Lightweight - Aluminum foil is considerably lighter than fiberglass or spray foams. Easier for one person to install rolls.
Inexpensive - Material and installation costs for aluminum foil insulation are among the most affordable options.
Non-irritant - Fiberglass can irritate skin and lungs during application. Aluminum poses no known health hazards.
Moisture resistance - Will not decompose, sustain mold growth, or lose R-value if roof leaks occur.
Long-lasting - With protection from physical damage, aluminum foil maintains reflective properties for decades.
Vapor permeable - Allows moisture vapor to escape while keeping airflow low and radiant heat out.
Recyclable - Post-consumer aluminum foil scrap has a high recycling value at end of service life.
Consistently outperforms other roof insulations in summer heat retention testing. The ultra-thin yet highly radiation-reflective qualities of aluminum foil make it a top-performing insulator.
Additional benefits for roofing contractors include fast and easy installation versus blown-in materials. Aluminum foil applications often take half the time of fiberglass. Product costs also tend to be very competitive per square foot. With similar R-values yet improved performance, aluminum foil rolls deliver strong value as a roof insulation solution.
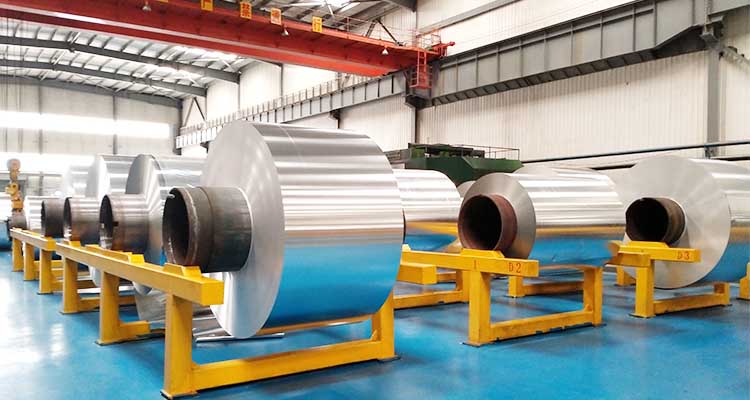
Long-term energy savings
One of the biggest benefits of using 8011 aluminum foil roll roof insulation is the substantial long-term energy savings it enables. By reflecting away the vast majority of radiant solar heat before it can enter and transfer through the roofing system, aluminum foil greatly reduces the thermal load placed on a home's HVAC system. This in turn lowers both electricity consumption and wear and tear on HVAC equipment over many cooling seasons.
Several studies have been conducted to quantify such energy savings. In Florida, using aluminum foil under shingles was found to reduce attic temperatures up to 30°F and cut home cooling costs by 20-30%. Scientists at Oak Ridge National Laboratory also tested various insulations, concluding reflective radiant barriers like aluminum foil perform best at elevated temperatures. They estimated using it nationwide could save $1 billion per year in energy costs.
Individual homeowners have seen reductions in their monthly electricity bills of 15-25% by upgrading to aluminum foil insulation during attic remodels or roof replacements. Extrapolated over a 30-year roof lifespan, such savings often outweigh the higher material cost of other insulations. The payback period on the up-front investment in higher performing aluminum foil is also typically under 3 years.
Beyond direct cooling energy reductions, aluminum foil insulation preserves indoor climate control system functionality for longer overall. By not overworking air conditioners in extreme summer heat, their operational lifespan is extended, as is that of furnaces in winter. Deferred replacement of HVAC equipment yields even more savings beyond reduced energy bills alone.