What is Aseptic Packaging?
6.3 Micron Aluminium Foil For Aseptic packaging refers to the process of packaging sterilized or ultra-heat treated (UHT) product in a sterile container under controlled, sterile conditions to extend its shelf life without refrigeration. It involves the following key steps:
UHT treatment: The liquid dairy product is heated to 135–150°C for 1–4 seconds to kill pathogens and microorganisms. This sterilizes the product without cooking or altering its taste.
Aseptic filling: The sterilized product is pumped from the UHT plant through sterile pipes into the sterile, pre-sterilized container under an aseptic environment.
Hermetic sealing: The container is quickly sealed under aseptic conditions to avoid contamination.
Container design: Containers like cartons/pouches are designed for food contact compliance and provide an effective barrier against oxygen, moisture and light.
The airtight, hermetically sealed packaging combined with product sterilization allows unrefrigerated shelf life of 3-6 months. This has revolutionized packaging in the dairy industry as it enables transportation and storage of products without refrigeration infrastructure.
Why is Alu foil for aseptic packaging important for Aseptic Packaging?
For effective aseptic packaging of dairy products, the container material needs to act as an excellent barrier against external factors like oxygen, moisture and light which can cause spoilage. Alu foil 1235 fulfills this role very well due to its unique properties:
Oxygen barrier: Alu foil 1235 is highly impervious to oxygen transmission. This protects the UHT treated products from recontamination and oxidation reactions that lead to rancidity.
Moisture barrier: Alu foil manufacturer is practically impermeable to moisture. This prevents condensation inside the pack and protects the product from drying out.
Light barrier: Alu foil manufacturer completely blocks ultraviolet and visible light rays. Light exposure can cause quality deterioration in dairy products through vitamin destruction and rancidity.
Chemical resistance: Aluminum is highly chemically resistant and does not interact with food. This maintains product safety and shelf life.
Thermal stability: It can withstand sterilization and packaging processing temperatures without decomposition.
Flexible and formable: Thin foils can be easily thermoformed into cartons, pouches and other packaging shapes without breakage.
Recyclable: Aluminum can be infinitely recycled without loss in quality, making it environmentally sustainable.
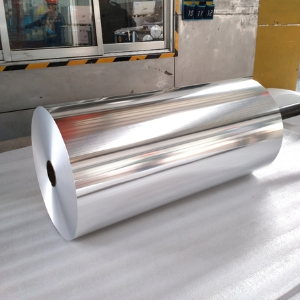
6.3 Micron Aluminum foil for Aseptic Packaging
For aseptic packaging applications in dairy, the ideal thickness of aluminum foil ranges between 6-9 microns. However, 6.3 micron foils are widely used due to their excellent barrier properties and cost efficiency. Some key advantages of using 6.3 micron foil laminates are:
Superior Barrier Performance
At only 6.3 microns, the aluminum foil layer is very thin but still delivers high barrier protection required to pasteurize dairy products. Oxygen transmission rates are as low as 0.01 cc/m2/day which is adequate for extending shelf life to 3-6 months without refrigeration.
Formability and Strength
The 6.3 micron thickness allows excellent thermoformability into packages without breakage. At the same time, it provides sufficient stiffness, rigidity and puncture resistance for carton/pouch packaging on high-speed lines.
Cost Effectiveness
Thinner foils require less aluminum for the same surface coverage area compared to thicker gauges. At large commercial scales, the reduced material usage directly cuts raw material costs. The cost-to-performance ratio of 6.3 micron foils is very competitive for aseptic dairy applications.
Sustainability
Using minimum aluminum just sufficient to provide the barrier performance lowers the environmental footprint compared to thicker foils. The reduced use of primary aluminum saves energy during production while enabling aluminum's infinitely recyclable properties.
Coextrusion Compatibility
6.3 micron aluminum foil lends itself very well to coextrusion lamination techniques. It can be smoothly coextruded with polymers like polyethylene to produce barrier laminates for flexible packages. This composite structure enhances mechanical properties further.
Consistent Quality
Advancements in foil rolling and processing technology enable precise control over 6.3 micron gauges within tight thickness variations. The consistency in barrier properties batch-to-batch ensures uniform shelf life is maintained across packages.
If you have any request about 6.3 micron aluminum foil .please contact us.
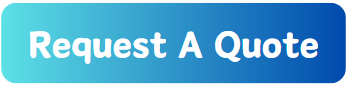
Types of 6.3 micron Aluminum Foils for Aseptic Packaging
There are different types of 6.3 micron aluminum foils available depending on surface treatment and lamination structure:
Natural Foil
The basic form is an untreated or mill finish foil with no coatings. It has acceptable barrier but higher risk of pinholes during processing. Mainly used for rigid containers.
Treatment Foil
Surface treated by anodization or semi-conversion coating to enhance adhesion and formability. Provides improved puncture resistance for flexible pouches.
Slip Foil
Coated with a thin organic layer like silicone to reduce friction for converting and printing. Suitable for high speed conversion lines.
Laminate Foils
Coextruded with polymer layers like PE or Nylon to form composites with balanced barrier-mechanical properties. Ideal for all flexible packaging structures.
Coated Foil
Coated with additional barrier polymers on one or both sides to further boost barrier and enable reclosability. Used in applications demanding highest shelf life.
Bi-Axially Oriented Foil
Processed films with polymeric/aluminum/polymeric structure having extra stiffness and puncture resistance due to molecular alignment.
Production of 6.3 Micron Aluminum Foil
The aluminum foil rolling process to produce 6.3 micron gauges involves the following key stages:
Aluminum Ingot Production
High purity primary aluminum ingots are produced by electrolytic smelting of alumina. India is a major supplier of ingots for foil mills globally.
Aluminum Rolling
Ingots are heated and fed into multi-stand hot rolling mills which successively reduce thickness through controlled compressive forces. Thickness is brought down to around 150-250 microns.
Cold Rolling
Sheets enter a series of heavy manned cold rolling mills which further reduce thickness through intense compression without heating. Multiple passes reduce thickness to the target gauge.
Coil Winding
Long coils of 6.3 Micron Alu foil are tightly wound under tension onto large drums ready for downstream processing like slitting, testing and packaging.
Quality Control
Stage-wise quality checks on thickness uniformity and surface defects are conducted using advanced instruments. Only foil batches meeting tight tolerances are approved.
Slitting and Packaging
Coils are uncoiled and slit to standard widths, securely wrapped and packed for transport to converter lines or storage under controlled conditions.
Strict quality standards ISO 9001 are followed to ensure consistent 6.3 Micron Alu foil gauges within +/-0.1 micron tolerance to fulfill dairy packaging requirements. State-of-the-art mills can produce 50,000-100,000 tons annually.
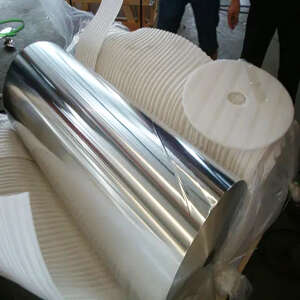
Application of 6.3 Micron Alu foil in Dairy Packaging
The aseptic packaging industry uses 6.3 Micron Alu foil as the primary laminate material in various structures and formats:
Carton Packs
Paperboard cartons are the most common format. The Alu foil for aseptic packaging is ultrasonically welded or glued between an inner polyethylene layer and outer paper-foil-paper or poly-foil-paper composite. Rigid round, square or rectangular packs of UHT milk are made.
Pouches
Stand-up pouches are made of three-layer foil-PE-foil or PE-foil-PE laminates. Horizontal filling pillow pouches use similar structures. Pouches offer highest shelf life for ultra-sensitive products like cream and flavored milk.
Bottle-type Containers
Some pouches like Flexibags mimic bottle shapes for ease of handling. Foil-PE-foil laminates are thermoformed or deep drawn into robust polyethylene bottles replacing traditional glass or cans.
Bag-in-Box
Large volume packs for foodservice use bag-in-box type pouches enclosed inside corrugated or paperboard boxes for stacking and transportation.
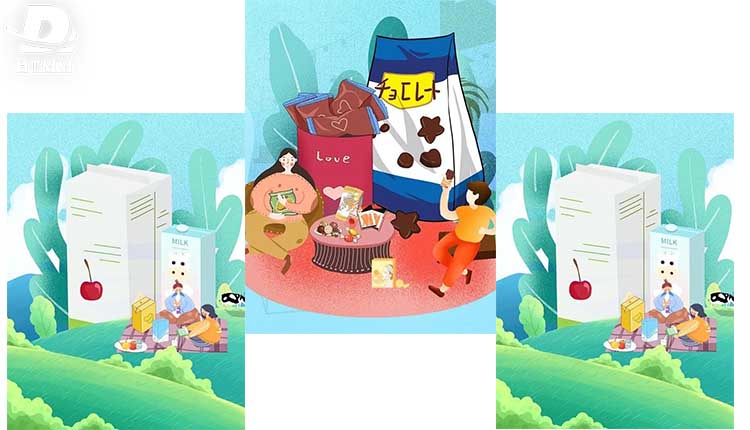