The Primary Aluminum Foil Raw Material : Bauxite Ore
All aluminum begins as bauxite ore, an aluminium-rich mineral typically found in the topsoil of tropical and sub-tropical locations like Australia, China, Brazil and Guinea. Bauxite is composed of hydrated aluminum oxides, hydroxides and occasionally silica minerals in impure forms that have undergone laterization - the weathering of rocks under hot, wet tropical conditions. Worldwide reserves of bauxite are estimated to exceed 29 billion metric tons, ensuring stable long-term supply of this critical raw material.
To extract pure aluminum from bauxite, the ore undergoes an energy intensive industrial process called the Bayer process. Crushed bauxite is mixed with sodium hydroxide (lye) under high pressure and temperature to dissolve the aluminum foil container raw materials hydroxides and oxides. The aluminum-bearing liquor is then separated from insoluble residues through settling. Impurities like iron oxides remain behind as red mud waste, while the purified liquor is treated with seed crystals to precipitate aluminum hydroxide. Aluminum Foil 3003 Container Foil Raw Materials is then blended with fluxing agents and heated to above 660°C in reduction cells to liberate aluminum through electrolysis.
The aluminum produced has 99% purity and is cast directly into ingots weighing between 25-150 kg each. These aluminum ingots are the primary feedstock for further refining and processing into end-use forms like aluminum foil. Their extremely high purity ensures compliance with stringent food contact material standards.
Refining Aluminum Ingots for Aluminum Foil 8011 Container Foil Raw Materials
Food grade Aluminum Foil Food Grade Roll Jumbo For Food Containers demand exceptionally high purity levels, so additional manufacturing steps are required to refine the aluminum ingots to specifications for 8011 material. These include:
Remelting and holding - Ingots are remelted under protective atmospheres to dissolve any inclusions and maximize uniformity. Precise temperature controls during holding homogenize the alloy chemistry.
Gas or flux degassing - Entrained gases like hydrogen are removed through either fluxing with chlorine/chlorides or proprietary gas atomization processes to make aluminum malleable for rolling.
Alloying additions - Precise metered amounts of alloying elements like magnesium, manganese, silicon or zinc are added to strengthen final foil properties as permitted by regulations.
Continuous casting - Molten aluminum is poured into a water-cooled drum and solidified rapidly into long thin slabs for rolling from a single cast. This improves grain structure.
Hot and cold rolling reductions - Multiple sets of heavy duty mill rolls progressively thin aluminum slabs at elevated temperatures followed by room temperature passes to final gauges.
Coil winding, inspection and packaging - Precision gauge controlled Aluminum Foil Food Grade Roll Jumbo For Food Containers is tension leveled, slit/sheared to width, tested for defects and quality, then coiled and shrink wrapped for shipment to customers.
Strict control over chemistry, purification steps, casting and rolling parameters ensures 8011 foil chemistry meets 99.5% minimum aluminum composition by weight as specified by the Aluminum Association. Further quality oversight during handling and storage protects purity prior to forming container components.
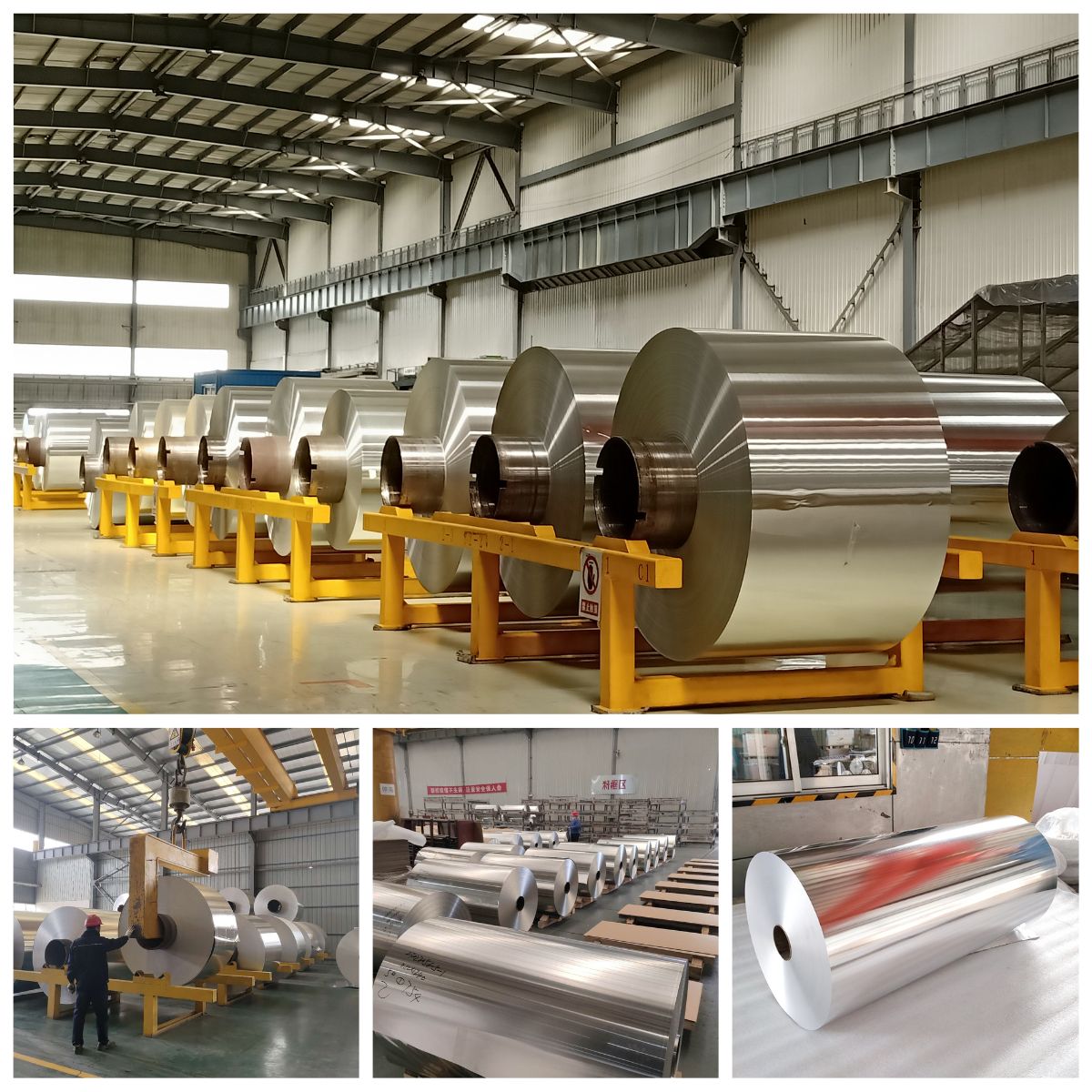
Implications of Aluminum Chemistry for Food Contact
While aluminum foil composition is specified as "Food Grade" or "Food Contact Compliant", rigorous controls over alloy composition and manufacturing refinement are required to safely meet international food safety standards:
FDA Regulations (21 CFR) - Sets upper thresholds of just 0.1% by weight for any single impurity and 0.5% total for all incidental additives in aluminum which may contact food under Conditions of Use A-H.
EU Directives - Similarly limits impurities to 0.1% for a single element and 0.5% total with aluminum >99.5% purity under Framework Regulation (EC) No. 1935/2004.
BfR Recommendations (Germany) - Classify aluminum as physiologically safe for direct food contact when produced to Good Manufacturing Practices and composition limits defined.
Foil producers carefully monitor chemical analysis throughout processing to guarantee composition falls well within regulatory acceptance levels. Ensuring absolute minimum levels avoids unwanted elements potentially migrating from packaging into sensitive food products over shelf life. Specific production certifications like ISO 22000 also help build consumer and customer confidence in food grade aluminum's remarkable safety record.
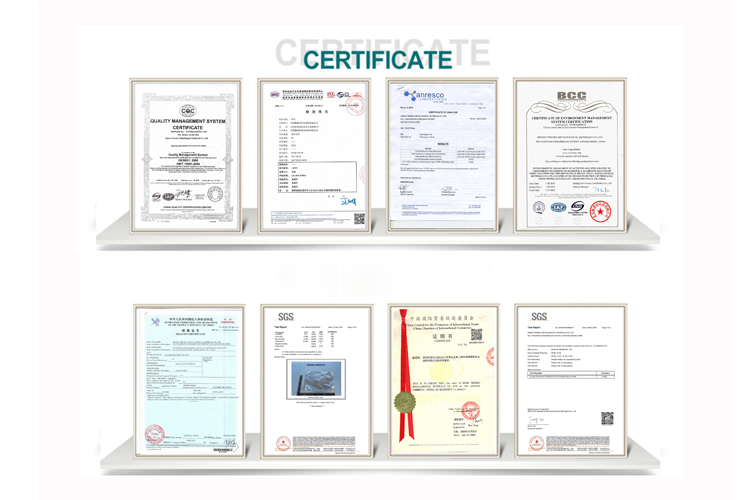
Converting Jumbo Foil Rolls into Trays and Containers
Bulk aluminum foil is not suitable in its coil form for direct food packaging applications. Further processing steps shape continuous jumbo rolls of grade 8011 foil into finished trays, containers and other forms optimized for various food products and storage scenarios:
Roll uncoiling and tension levelling - Unwinds long continuous strip of foil roll at high speed into the conversion line.
Precision slitting - Shears foil to formatted widths required for particular final container dimensions.
Custom die cutting - Razor sharp rule dies stamp blank components for each container's walls, lids, tabs etc per programmed patterns.
Forming - Components are assembled into desired 3D tray geometries using various thermoforming, press molding or folding techniques.
Edge sealing/crimping - Heat or adhesive bonds raw edges together on three sides to complete tray enclosure except access opening.
Decorating - Optional printing, lacquering or surface treatments according to product or brand specifications.
Inspection, cleaning, packing - Quality assurance scans detect flaws before nesting clean trays into cartons or bulk bins for shipment to fillers.
In skilled hands, an ingenious variety of stock and custom aluminum foil trays, clamshells, wrap-arounds and other efficient package designs emerge tailored for particular market applications. All hygienically fabricated solely from versatile food compliant raw materials.
Quality Assurance and Safety Testing
Despite aluminum foil's outstanding safety record, manufacturers subject conversion lines and finished packaging structures to rigorous testing to validate ongoing compliance with all regulations as production conditions evolve:
Chemical analysis - Periodic ICP-OES spectrometry precisely verifies aluminum purity and maximum allowable levels of incidental additives are not exceeded batch-to-batch.
Microbial screening - Hygiene swabbing validates manufacturing and packaging areas are free of detectable pathogen contamination like Listeria, Salmonella, E. coli.
Extractable metals testing - Accelerated conditions mimicking long-term food storage are used to quantify miniscule metal migration levels from foil into solvents.
Adhesive qualifying - Any glues, inks or resins also undergo comprehensive approval testing to confirm their safety, chemical makeup is accurately disclosed and components will not leach or migrate.
Package integrity analysis - Burst tests, puncture strength measurements, seal reliability assessments etc. confirm trays structurally withstand common handling and distribution environments to protect enclosed food items.
This multilayered verification serves to prevent quality lapses in raw materials, manufacturing practices or finished package performance that could potentially undermine food safety - the utmost priority for aluminum foil grade 8011 used ubiquitously in global food industries. Certifications like SQF and FSSC 22000 further underpin reliability.
Applications of Food Grade Aluminum Foil Containers
From grocery store shelves to industrial food production lines, the durable yet hygienic properties of aluminum foil food containers enable handling and storage of a vast array of consumables. Here are some typical applications:
Meat/fish/deli trays - Individually portion controlled overwrap for luncheon meats, cheese, smoked salmon etc in delis and packaged goods aisles.
Snack/baked goods - Enclosure for crackers, chips, cookies, frozen appetizers, muffins and similar portions demanding food safe transport and merchandising.
Produce - Containers for retailed spinach, salad mixes, berries and other perishable items with built-in moisture barrier.
Ready/convenient meals - Retail clamshells keep pre-made lasagnas, pot pies, noodle dishes safe and stable ready for microwaving.
Industrial food processing - Portioning trays for meat/cheese/dairy products to facilitate assembly of multi-ingredient entrees, sandwiches prior to cooking or freezing stages.
Foodservice use - Disposable serving trays, warming pans, chafing dishes for meals in hospitals, schools, retirement facilities with microwave/oven/warmer compatibility.
Pharmaceutical packaging - Specific designs for encapsulated supplements, herbal/vitamin tablets requiring breathable yet contamination-preventing primary enclosures.
All rely on aluminum foil's favorable functional properties, formability into sanitary enclosures and assured compliance with international food safety standards. Grade 8011 is a cornerstone material for the global food and consumer goods economy.
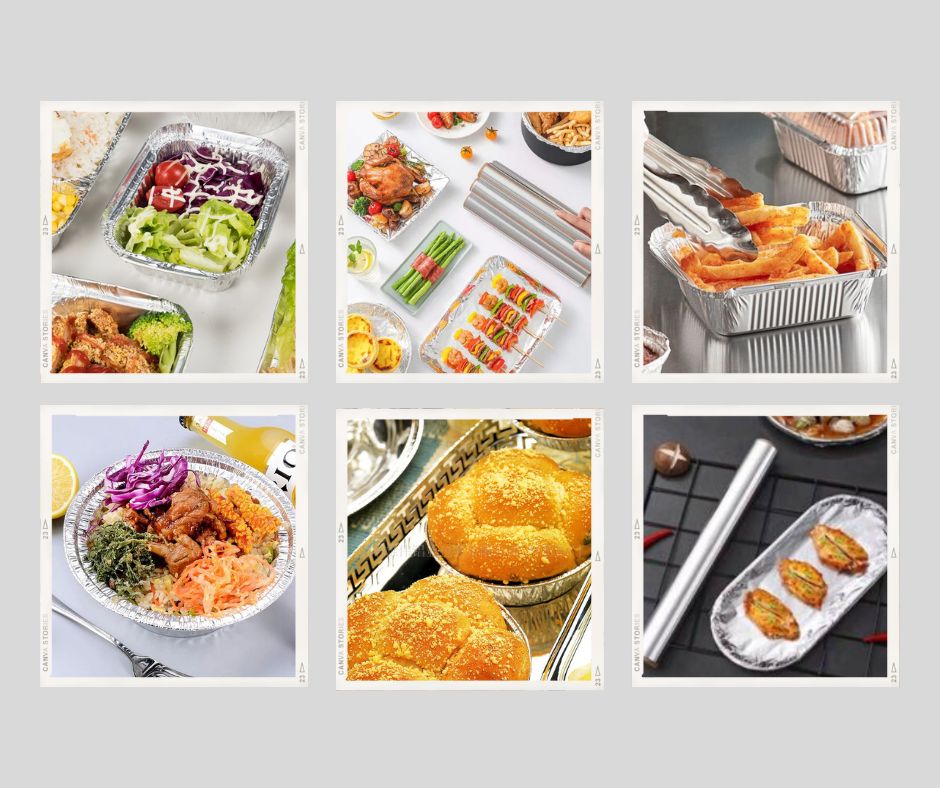
As demonstrated by the exhaustive mining, manufacturing and control processes required, aluminum foil grade 8011 earns its designation as a premium food contact material through meticulous attention to purity and safety.