Advanced coating technology is driving the adoption of color foils. Suppliers use a controlled coating method by applying a very thin uniform layer that fully bonds to the clean foil without compromising its recyclability or aluminum structure. Advanced curing oven configurations determine complex pigment patterns without immediate deformation. Precise coating gauges ensure reliable coverage regardless of substrate thickness. Today’s selections encompass matte, silk or gloss finishes across the color wheel in optimal opacities for any design need.
Container form fill machines print digitally in variable designs. Laser cutting rapidly produces complex shapes from colored blanks on demand. Robotic loaders accurately sort components directly into containers formed on line. Their bright exterior attracts supermarket shoppers among competitors while maintaining integrity throughout the supply chain and microwave reheating. The hazy foil also camouflages the low-visibility items with a tempting metallic palette of the remaining items.

Suppliers help innovations provide in-depth evaluations. The rigor of the test simulates warehouse vibrations and stacking pressures to ensure survival of the coating and container adhesive distribution. The thermal shock method tests color stability through industrial reheat and freezer. Barrier assessment proves protection against intrusion over a product lifetime of 9-12 months. Optimization feedback from the results constantly drives performance forward.
Aluminum retains leading advantages as demand increases. Its infinite recyclability and abundant global presence offer reliable closed-loop solutions. Paired with a permanent color coating, colored containers are promised their bright future that nourishes the global population for ages to come.
Color Coated Aluminium Foil containers Aluminum Foil Type 3003 attract in different product segments. Prepared food companies use it for portioned entrées that are stabilized for shipping and then reheated on their impressive ships. The bakery shapes colorful foil trays to attractively present artisan pastries without bags. Butchers and delis fill formed containers with a variety of meats and cheeses, to make grab-and-go convenient. Produce Growers use colored foil for berry boxes and trays of seasonally harvested vegetables. Their versatility expands applications.
Suppliers partner with manufacturers, promoting customized container solutions. Laboratories test innovative coatings while maintaining barrier integrity while equipped with antibacterial properties. Some explore the insertion of pulsed UV indicators signaling safe reheating levels. Joint projects create foil/paper laminate-like composite structures using the strengths of each material for cereal boxes. Some combine bioplastics with foils that meet both functional and environmental commitments. Continued cross-industry collaboration broadens the innovations possible.
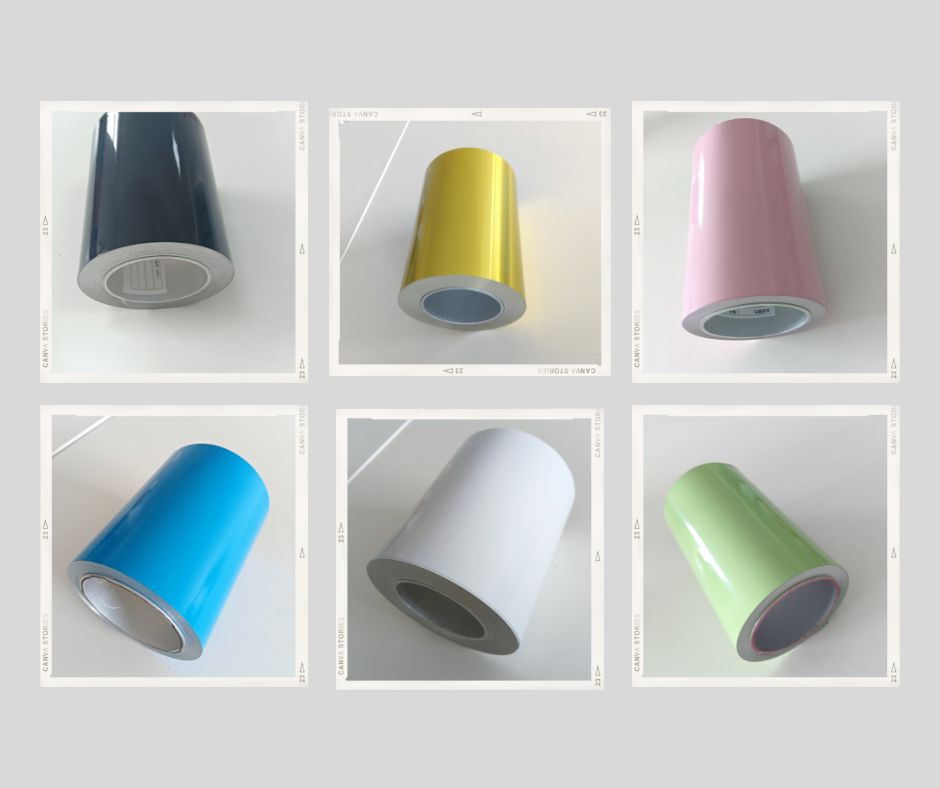
As consumer priorities elevate environmental and social consciousness, Coated Aluminium Foil containers prove uniquely qualified. Their infinite recyclability through established collection systems ultimately recovers all materials. Only 5% of the original energy is required to rebuild the aluminum cycle from scrap to new stock. Responsible sourcing and closed-loop manufacturing prove the container’s credentials for discerning buyers. Partnerships with ideal workplace standards and carbon-reduction targets in global supply chains deliver greater sustainability.
Coated aluminum foil Aluminum Foil Type 3003 refers to aluminum foil to which a thin layer of polymer, lacquer or other material is applied on one or both sides. The coating is used to enhance the properties and performance of foils for various applications. Several types of coatings are used:
Polymer coatings such as polyethylene improve grease and moisture resistance, making Coated Aluminium Foil suitable for cooking and food packaging. They provide nonstick surfaces and barriers to oil, juice and other liquids.
The lacquered coating adds features such as extended printability. They form a thin protective layer that allows graphics and labels to be printed on the foil surface. This is important for product branding and information printing on food packaging.
Barrier coatings such as silicone enhance the foil’s ability to prevent gases such as oxygen from penetrating through. This is crucial for applications where oxygen is needed to be kept from the food to extend shelf life. The barrier coating makes foil suitable for packaging snacks, dry foods and other products requiring high barrier properties.
Coatings are applied thinly, precisely and continuously through processes such as roller coating, blade coating and screen coating. It bonds completely with the underlying aluminum surface, becoming an integrated part of the foil foil. 3003 Alloy Making Food Container Aluminum Foil retains the flame resistance, flexibility and other advantages of aluminum while adding functionality that makes it suitable for specific end uses. They are widely used in food packaging, pharmaceuticals and other markets.
Coated aluminum foil offers various advantages over uncoated foil. The barriers provided by the coating allow foils to be used for applications requiring higher resistance to liquids and gases. This increases potential usable products and shelf life. The coating also enhances the printing and marking ability of the foil. Products can be clearly labeled and branded directly on the foil surface. For some applications, the coating can extend the range of operating temperatures that the foil can withstand.
Suppliers have developed extensive coating capabilities for customized coated foils for different customer needs. One or both sides of the foil can be coated. Coatings are available in a wide range of formulations to achieve desired levels of barrier, slip, ink viscosity and other properties. Some coatings are textured or patterned to add visual interest or functionality. Through careful control, suppliers can ensure coating thickness is precise and uniform. It also helps customers to thoroughly test coated foil samples under applied conditions to validate performance before full-scale production. This ensures that the coated foils will meet the requirements for mechanical properties, shelf life extension and other critical factors.
.jpg)
Coated aluminum foil finds various applications in food packaging due to the advantages offered by the coating. Lids are widely used as films and patches to seal containers, snack bags, pouches and other food packets. The coatings provide an effective barrier while allowing the lid to peel off easily. Coated foil is commonly used as a substrate for labeling food cans to provide a good ink adhesion surface. It is also used to wrap food items such as cheese, meat and baked goods to provide protection from liquids and gases. Some foils have a heat resistant coating that allows them to be thermally sealed for packaging operations.
Pharmaceutical companies use coated Aluminium Foil 8011 using for food sector for blister packs, capsules and other drug packaging applications. The coatings create effective moisture and gas barriers, keeping products stable and protected. Some Aluminium Foil 8011 using for food sector have a heat seal coating that allows for easy sealing and packaging on high-speed lines. Coated foils are used in wall and roof applications due to their corrosion resistance and ability to form foils. They have good reflectivity and can be patterned or painted. 3003 Alloy Making Food Container Aluminum Foil are also used as construction barriers and vapor shields in construction materials. Their lightweight, formability and barrier characteristics make them effective for this end use.