Foil roll aluminum is a versatile material with many packaging applications. It can be used for wrapping, lining, bag making and more. But with so many foil options available, choosing the right one for your needs can be confusing. This guide will help you understand the different types of aluminum foil and factors to consider when selecting foil for your packaging requirements.
1. Aluminum Foil Thickness
Foil aluminum Thickness is the most basic specification of foil roll aluminum and is measured in microns or gauges. Thinner foil below 20 microns is best for intricate wrapping or when light weight is required. Medium thickness between 20-50 microns is suitable for general purpose packaging. Foils above 50 microns are heavier duty options, ideal for industrial uses like lining boxes. Choose thickness based on your required strength, flexibility and weight needs.
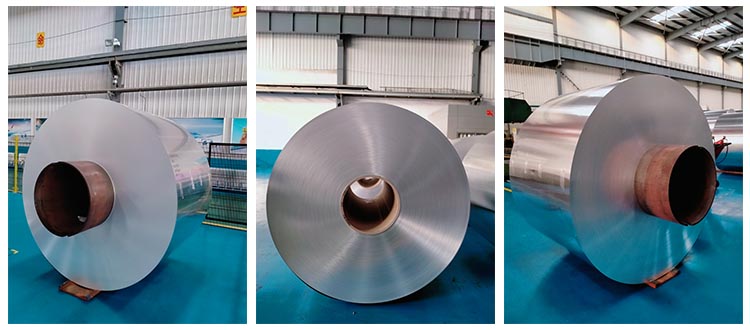
2. Aluminum Foil Temper
The temper or softness of roll aluminum foil also affects its strength, ductility and stretchability. There are three main tempers:
• Soft - Below 150°: This is the most malleable and easiest to tear or puncture. Soft foil is best for delicate wrappers or food liners that need extra softness.
• Half-hard - 150-200°: This has medium tensile strength and can stretch further before breaking. Half-hard foil is suitable for most general purpose packaging applications.
• Hard - Above 200°: This is the strongest temper with high tensile strength but less flexibility. Hard foil is durable for industrial lining, heavier duty bags and boxes.
3. Foil Aluminum Surface Treatment
The surface of roll aluminum foil can be treated to alter its performance:
• Mill Finish: Has a natural matte finish and is untreated. Mill finish foil is economical but not very appealing for premium packaging.
• Annealed: Heated and softened to increase formability. Annealed foil has a slightly shiny finish.
• Emulsion Treated: Coated with a resin to improve adhesion for lamination or printing. It has a glossy surface that takes ink well.
• Crystallizing Treatment: Heated to make small crystals on the surface for enhanced printability and adhesion.
Choose surface treatment based on your printing and adhesion requirements. Emulsion and crystallizing treatments are best if foil printing or lamination is needed.
4. Aluminum Foil Width
Foil aluminum is sold in standard widths from 6 inches to 100 inches or more, in half inch increments. Width will determine how much material you get in a roll and how many parts you can cut from a sheet. Choose the widest width suitable for your application to minimize waste.
5. Form
foil aluminum is available in four main forms:
• Rolls: Most economical when packaging a single product or in high volumes.
• Sheets: Useful for one-time or small batch packaging applications. Less waste than rolls.
• Pre-cut shapes: Rectangles, squares or custom die-cut shapes for specific uses. Convenient but more expensive.
• Bags: Premade stand up foil bags for products like potato chips. Ready-to-use but have a higher overall cost.
Pick the aluminum foil form that matches your packaging production needs in terms of cost, convenience and required shapes.
Additional Considerations
Other factors to weigh when choosing aluminum foil include:
• Purity: Higher purity foils above 99% aluminum content are best for food contact.
• Alloy: Specific alloys may be needed for heat resistance, strength or corrosion protection.
• Barrier properties: Foils with a special oxide coating can provide moisture and oxygen barrier.
• Recyclability: To have a less environmental impact, choose aluminum foil that has been recycled.
• Cost: Balance thickness, surface treatment and purity needs with your packaging budget.
A variety of packaging applications can be made use of the adaptable material known as price aluminum foil. It is extensively utilized in the food business, the pharmaceutical industry, and other sectors where high-quality packaging is necessary to shield items from outside influences. But selecting the price aluminum foil for your packaging requirements might be difficult. We'll go over how to pick the ideal aluminum foil for your packaging needs in this article.
6. Aluminum Foil Alloy
When selecting the best aluminum foil for your packaging needs, it's also important to take the alloy into account. The composition of aluminum foil is referred to as the alloy. Aluminum foil is most frequently made from the alloys 8011 and 1235. There are additional aluminum alloys, though.
Due to how it impacts the foil's ability to resist corrosion, the aluminum alloy is crucial. Because it shields the packaged product from any chemical reactions with the foil, aluminum foil's corrosion resistance is essential.
Because of this, you must take into account the degree of corrosion resistance necessary for your product when selecting the appropriate aluminum foil for your packaging needs. For instance, you could require foil with a stronger corrosion resistance if your product is acidic or contains a lot of salt.
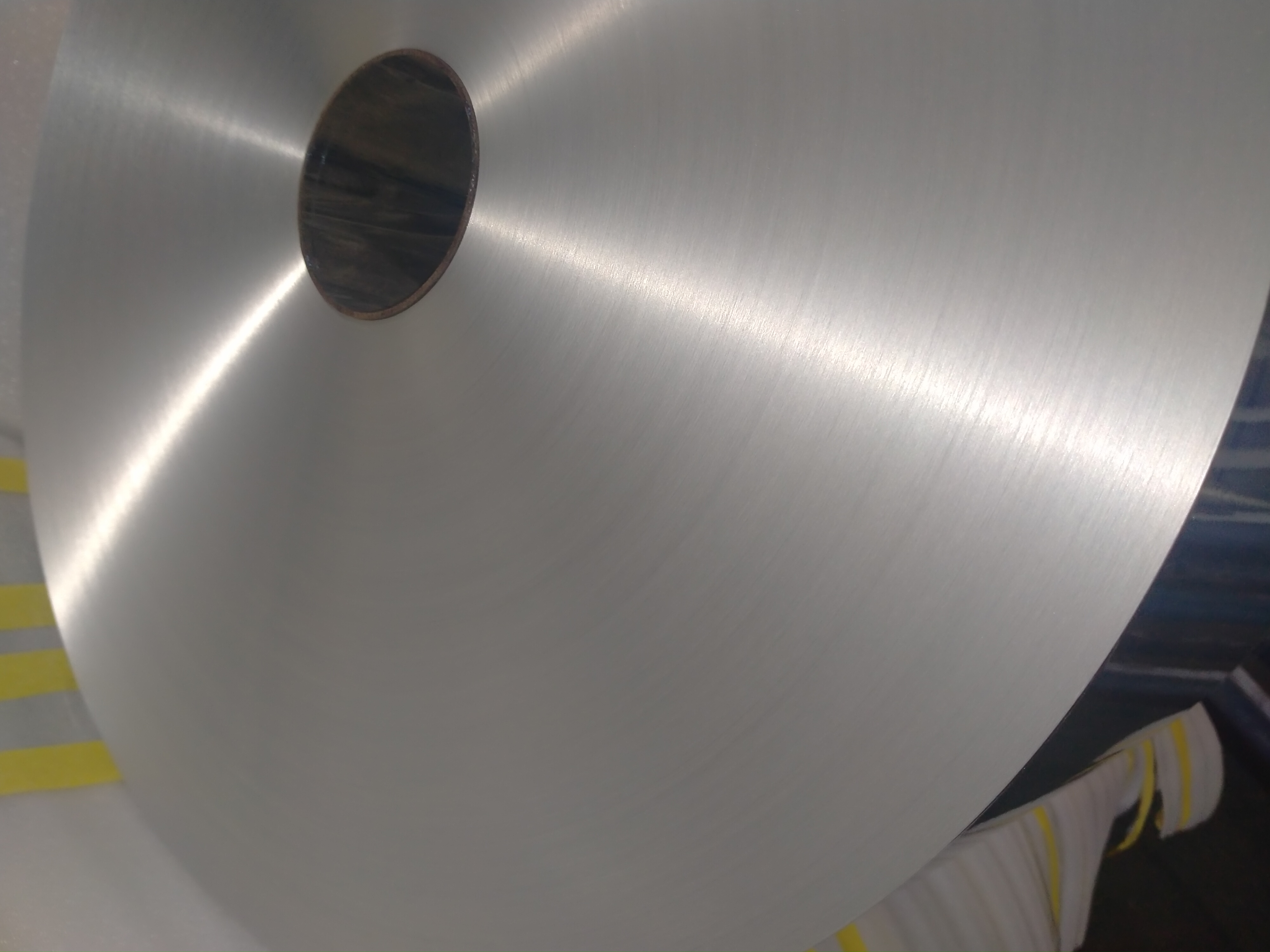
Surface Quality
When selecting the ideal aluminum foil for your packaging needs, it's also essential to take the foil's surface finish into account. The appearance of the aluminum foil's surface is referred to as its surface finish.
Bright finish, matte finish, and satin finish are the three most popular surface treatments for aluminum foil.
Aluminum foil's surface finish is crucial since it influences the packaging's appearance and functionality. For instance, choosing a foil with a brilliant finish may be a good idea if you want your packaging to look sparkling.
Consequently, you must take into account the intended aesthetic and functionality of your packaging when selecting the appropriate aluminum foil for your packaging needs.
Barrier Features
When selecting the best aluminum foil for your packaging needs, it's also important to take into account the foil's barrier qualities. Aluminum foil's barrier capabilities refer to its capacity to shield the packaged product from external elements like dampness.