Jumbo foil roll is a versatile material that is used in a wide range of industries for packaging, insulation, shielding, and more. Ensuring consistent quality in foil wholesal manufacturing is essential for meeting customers' requirements and maintaining a competitive edge. Here are some key ways to achieve quality control in aluminum foil production.
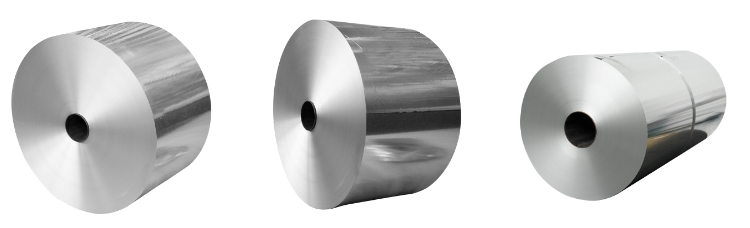
Start With Strict Incoming Material Checks
The raw materials used in jumbo foil roll manufacturing, mainly foil wholesal, have a significant impact on the final product quality. Therefore, perform stringent checks on incoming material to verify that it meets your specifications. Examine foil jumbo roll for defects, cracks, damage, and inconsistencies in thickness and width. Apply nondestructive tests like ultrasound and X-rays to detect internal defects. Only accept material that passes all tests and checklists.
Maintain Machinery and Equipment Properly
The machinery and equipment used at various stages of foil jumbo roll manufacturing, such as annealing furnaces, rolling mills, and cold rolling stands, must function precisely to produce consistent results. Have a planned preventive maintenance schedule in place and carry out repairs and replacements immediately as needed. Regularly calibrate gauges and sensors to ensure accuracy. Also, train equipment operators to follow standard operating procedures.
Control Parameters During Production
Strict control of critical manufacturing parameters like temperature, time, pressure, and tension during production is essential to achieve consistent thickness, width, surface quality, and mechanical properties in aluminum foils. Install sensors and instruments to monitor these parameters during operations and link them to automation systems. Define acceptable tolerance limits and alert operators when parameters are out of range. Take corrective actions as soon as deviations occur.
Institute Statistical Process Control
With statistical process control (SPC), you can monitor the foil aluminum roll manufacturing process to detect when deviations arise. Establish control charts by measuring critical quality characteristics at various stages and tracking them over time. Set upper and lower control limits based on historical data and product specifications. When data points fall outside control limits, investigate the root cause and take action to correct the process and bring it back into control. Performing SPC enables you to catch issues early before they impact product quality.
Perform 100% In-Process and Final Inspections
In-process inspections during foil aluminum roll manufacturing provide an opportunity to detect and fix quality issues before defects reach the final product. Monitor critical quality attributes like thickness, flatness, and tear resistance at different stages, such as after rolling, slitting and annealing. Perform 100% checking of final foil rolls before packaging and shipping using equipment like thickness gauges, micrometers, and tear testers. Only release foil batches that meet all quality specifications to storage.
Track Quality Data and Take Corrective Actions
Tracking quality data from various checks and inspections during aluminum foil production can reveal trends, patterns and areas for improvement. Collect, analyze and visualize data using statistical tools like control charts, histograms and Pareto charts. Review inspection reports, nonconformance records and customer complaints regularly. Identify root causes of defects and failures. Implement corrective actions such as equipment repairs, procedure changes and employee retraining. Over time, quality data analysis will help strengthen your manufacturing processes.
In summary, by following these guidelines for strict materials inspection, proper equipment maintenance, tight parameter control, statistical process monitoring, 100% checking and quality data tracking, you can achieve consistent quality in Aluminum foil manufacturing and improve customer satisfaction.
It will be possible to formalize these best practices and achieve long-term sustainable quality improvement by putting in place a thorough quality management system. If you have any further inquiries, please let me know.
Today's civilization relies heavily on aluminum foil because it has so many uses, from food packaging to industrial purposes. A strong quality control system must be in place in order to produce aluminum foil of the highest caliber. In this post, we'll go through the essential actions aluminum foil producers may take to guarantee quality control throughout the production process.
Inspection of raw materials
Inspecting the raw materials is the first stage in guaranteeing quality control in the production of aluminum foil. Specific quality requirements for aluminum should be met before it is utilized to produce foil. Making ensuring that the aluminum is free of impurities like iron, silicon, and copper is the responsibility of the manufacturer. If impurities are present, they may degrade the final product's quality and lead to problems.
casting after melting
Melting and casting come next once the raw materials have been examined. The aluminum is melted and cast into substantial blocks during this procedure, and the blocks will later be processed into foil. The final product's quality depends heavily on the quality of the aluminum blocks. The aluminum blocks should be free of fractures, cavities, and other flaws that could lower the quality of the finished product, according to the manufacturer.
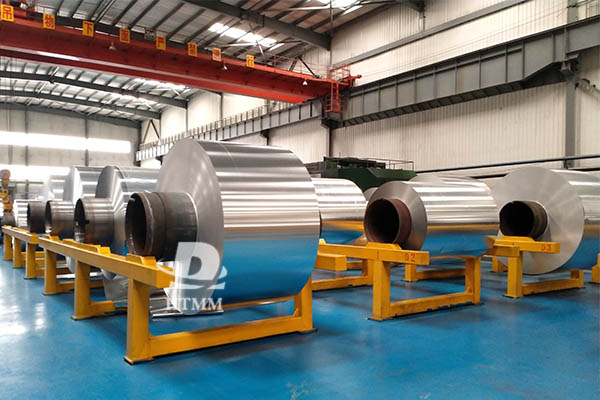
Annealing and rolling
Two essential steps in the production of foil aluminum roll are rolling and annealing. Aluminum blocks are rolled into thin sheets during rolling, and the sheets are heated to a particular temperature and then progressively cooled during annealing. These procedures are essential for ensuring the excellent quality of the finished product. To prevent flaws like wrinkles, cracks, and pinholes, the manufacturer should make sure that the rolling and annealing operations are carried out properly.
Lamination and Coating
Aluminum foil's characteristics are frequently improved via coating and lamination. For instance, coatings can be employed to improve the foil's barrier qualities, making it better suited for food packing. The foil's overall quality should not be impacted by the coatings and laminates utilized, which must be of the highest caliber.
Inspection and testing
Testing and inspection are essential for effective quality control in the production of aluminum foil. To ensure that the finished product satisfies certain quality requirements, the producer should run routine tests. The tests that can be performed include surface quality inspection, tensile strength testing, and thickness measuring. The completed product should be inspected by the manufacturer for flaws like wrinkles, pinholes, and cracks.