Jumbo coil aluminum foil is a thin, flexible material made from aluminum alloy sheets. jumbo coil aluminum foil comes in various thicknesses and alloys to suit a range of purposes. Within its designed applications, tensile strength is an important property that determines how suitable a particular foil is.
Tensile strength refers to how much longitudinal stress a material can withstand before failing. It's a measure of how much the material can be stretched or pulled apart. A higher tensile strength means the foil is less likely to break, puncture or tear under tensile loads.
For most uses of aluminum foil roll jumbo, a tensile strength between 13,000 and 18,000 pounds per square inch (PSI) is considered good. Here are the factors that determine the ideal tensile strength for foil:
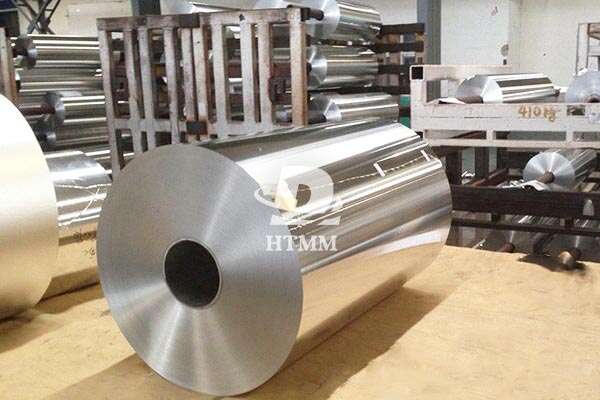
Thickness
Aluminum foil roll jumbo thickness has the largest impact on tensile strength. Thinner silver foil roll tend to have lower tensile strength because there is less material resisting tensile loads. Standard aluminum foil ranges from 0.001 to 0.005 inches thick and has a tensile strength of 13,000 to 16,000 PSI. Heavy-duty foil from 0.006 to 0.008 inches thick can achieve strengths up to 18,000 PSI.
For most applications like wrapping food and industrial insulation, regular foil thickness is sufficient. But tasks that involve crimping, folding and abrasion benefit more from heavy-duty foil with a higher tensile strength.
Alloy Composition
Aluminum alloys with manganese content have higher tensile strength due to manganese's strengthening effect. For example, silver foil roll containing 11% manganese has a tensile strength around 15,000 to 18,000 PSI. This is noticeably higher than pure aluminum foil (3XXX series) with strengths under 13,000 PSI.
Foil intended for heavy-duty uses should contain some manganese to boost its tensile strength. However, manganese also makes foil harder and less ductile so softer aluminium foil price are better for applications that require folding.
Surface Coatings
Some aluminium foil price have surface coatings that reduce their tensile strength slightly. Lubricants are often added to the coating to make the foil nonstick, grease resistant or easier to tear. These coatings can weaken the foil's tensile strength by 5% to 20%, so uncoated foils are inherently stronger.
When high tensile strength is critical, choose foil with minimal coatings or an untreated surface. But for most wrapping and insulation, the reduction in strength from coatings is negligible.
Application Requirements
The necessary strength depends on how the foil will be used. Some applications that benefit most from high tensile strength foil include:
• Industrial insulation where foil undergoes abrasion and tears easily
• Medical uses with risks of punctures
• High pressure barriers for fluids and gasses
• Crimping and sealing around pipes and containers
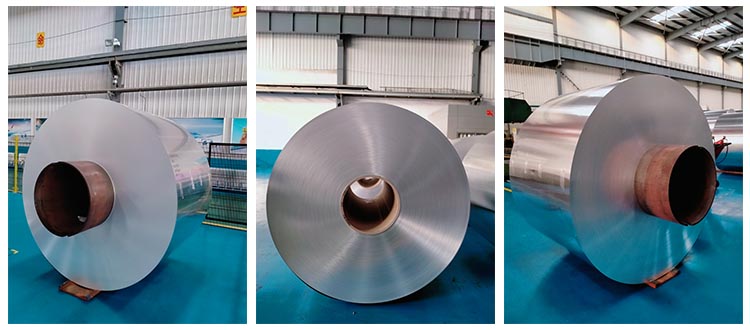
For simple uses like wrapping food or lining baking pans, regular foil with a tensile strength around 15,000 PSI is sufficient. Heavier-duty foil above 18,000 PSI is usually overkill unless the application involves folding, crimping or abrasion that risks weakening regular foil.
In summary, a tensile strength between 13,000 and 18,000 PSI ensures aluminum foil is resistant enough for most wrapping and insulation applications. Heavier-duty foils with tensile strengths above 18,000 PSI provide extra durability for tasks that put more stress on the material. Choosing foil based on its thickness, alloy, surface coatings and your specific requirements will help you achieve an appropriate tensile strength for the intended use.
High-Grade Aluminum Foil: Unmatched Quality and Performance
Aluminum foil is available in a wide range of grades to suit various applications. While regular foil gets the job done for many simple uses, high-grade foil made from specialized alloys offers unmatched quality and performance. Choosing high-grade foil for the right application can make a huge difference.
What Makes Foil High-Grade?
Several factors determine whether aluminum foil is considered high-grade:
Alloy - Foils made from specialized alloys like 8011 (81% Al, 11% Mn) or 8079 (80% Al, 7% Zn, 9% Mg) are high-grade due to their unique properties.
Thickness - Heavier gauges above 0.005 inches are categorized as high-grade and industrial foil.
Surface - Untreated or anodized surfaces are higher quality than coated foils.
Properties - High tensile strength, higher temperature resistance and less heat transfer make foil a higher grade.
Cost - High-grade foils tend to cost more due to the specialized alloys and extra production steps.
Uses - Foils intended for specialty uses like industrial insulation, medical applications and extreme conditions are high-grade.
So what do you gain by choosing high-grade foil for the right application?
Advantages of High-Grade Foil
High-grade foils provide the following benefits over regular foil:
Increased Durability
The thicker gauges and specialized alloys of high-grade foil make it significantly more puncture resistant, tear resistant and abrasion resistant. It's less likely to break down under extreme use.
Higher Heat Resistance
Foils like 8011 alloy can withstand continuous heat up to 550°F while regular foil breaks down above 400°F. The extra heat resistance of high-grade foil expands its cooking and insulation capabilities.
Reduced Heat Transfer
Due to the unique properties of their alloys, some high-grade foils impede heat transfer through the material more effectively. This makes them superior insulation materials.
Increased Strength
The combination of thicker gauges and specialized alloys give high-grade foils tensile strengths up to twice that of regular foil. This extra strength allows them to better withstand tension, stress and crimping.
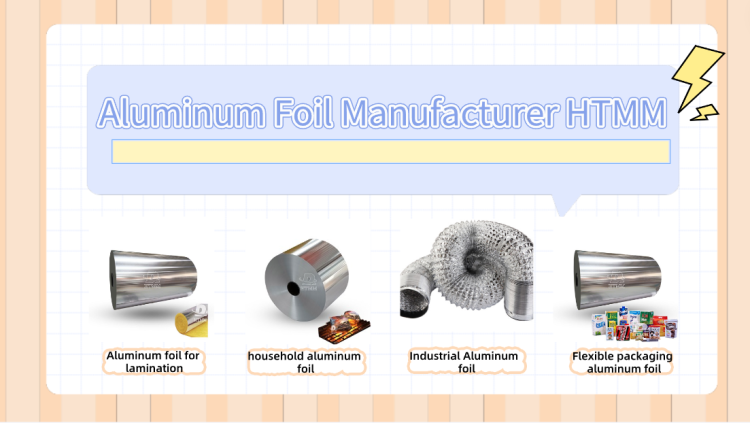
Greater Chemical Resistance
Foils made from certain alloys like 8079 exhibit higher resistance to corrosion from acids and chemicals. They maintain their properties after exposure better than regular foil.
Untreated Surface
Many high-grade foils have untreated or anodized surfaces rather than lubricated coatings. This provides a purer aluminum material with maximum strength and minimum contamination.
Specialized Performance
High-grade foils are often tailored for specific uses requiring the maximum possible performance from aluminum foil. Their alloys and properties are optimized for these purposes.
Suitable Applications for High-Grade Foil
Examples of applications where high-grade foil provides clear advantages include:
Industrial insulation for extreme conditions involving abrasion, tearing and high heat
Sealing and crimping around valves, pipes and containers with high internal pressure