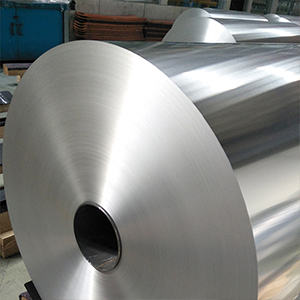
The tempering process also affects other properties such as strength, ductility and thickness. Soft foils have lower tensile strength but higher flexibility, making them more flexible. It can be rolled much thinner to 5-10 microns. A harder temper gives a stronger, harder material that holds its shape better for pans, trays and rigid containers. For soft foil-like applications, it requires a thick gauge of 20-50 microns. These factors dictate general use - soft foil excels in food packaging, sandwich wraps and container linings due to its thin, flexible formability. Hard foil works well for cooking pans, baking cups and takeaway service-ware where rigidity and dent-resistance are important.
While hard aluminum foil maintain shape better, softer foils can do many of the same things while providing extra support. For example, soft foil takeaway containers are reinforced with folds and crimps in the material. Food service pans are solidified through extended bases or cradles. The choice of the right foil depends on the required performance characteristics, manufacturing constraints, and overall cost considerations for the specific intended application. Both tempers meet different requirements through optimized material properties while providing the basic functionality of barrier protection and stability expected from aluminum.
Processing technique is another factor that affects the inherent properties of soft versus hard foils. Soft foil goes through a slower rolling schedule with more frequent annealing stops to achieve the required flexibility. The work is spread over many more rolling stands. Hard foils follow a more aggressive schedule by applying more rolling forces at a lower stand, thus providing the work hardening required for rigidity. These tailored processes ensure that the microstructure is optimized for the use of each temper.
Appearance is also affected by mood. The Soft temper aluminum foil
hard aluminum foil shine is more reflective, shiny compared to the satin finish of the hard foil. Different grain structures scatter light in distinct ways. The working solid state of hard foils can reveal visible microscopic multidirectional flow lines under magnification from rolling strain. Proper quality control regardless of temper ensures consistency in gauge tolerances, surface quality and degree of purity which is critical to performance and safety.
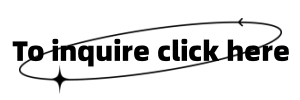
Both temper types are very sustainable due to the recyclability of aluminum. After use, soft and hard foils are typically recycled together through curbside programs and melted back into ingots without loss of properties for reprocessing.hard aluminum foil can go through fewer recycling loops because their extended durability extends product life. Overall recycling rates in developed countries exceed 60%, helping aluminum minimize environmental impact across countless applications that meet critical needs.
While Soft aluminum foil and hard aluminum foil have different material properties, both offer outstanding barrier properties to protect food, pharmaceuticals, chemicals and other products from moisture, gases, odors and cross-contamination. Due to the dense molecular structure of aluminium, the soft foil provides an effective barrier down to 5 micron gauge. Hard foil maintains over 20 microns of integrity for heavy use exposed to wear. Both seal more than 99% of oxygen and water vapor, far surpassing alternatives like plastic. This storage capacity stems from the combination of aluminum’s high impermeability and inertia.
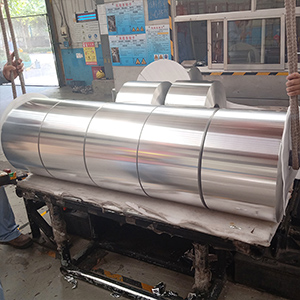
While there are differences in the properties of Soft temper aluminum foil and hard foils, both offer outstanding formability potential through press-working and other conversion methods. The annealed temper of the Soft temper aluminum foil allows it to be deeply drawn or stamped into intricate shapes at high speeds on modern conversion lines. Typical products include blister packs, snug-fitting liners, pleated containers and various formed packaging components. Hard foils undergo various formations such as turning or multi-stage pressing in solid objects such as baking cups, pans and trays and require rigidity rather than mouldability. Both tempers complement the downstream converting capabilities.
Quality assurance remains essential regardless of foil properties. Testing ensures consistency in important factors such as thickness, degree of purity and mechanical integrity. Constraint analysis ensures safety standards are met. Suppliers implement strict control programs to maintain quality through sourcing and delivery. Even major brands undergo deliberate abuse testing to evaluate performance under extreme expected conditions. Joint efforts between manufacturers and quality inspectors help guarantee aluminum’s renowned protective qualities.
With thoughtful application of the power of each temper, soft and hard aluminum foil offer highly customized solutions. Foodservice chooses hard for durability and securely wraps soft perishables. Medical packaging uses both - rigid for external protection of the soft inner lining preserving a sterile environment. The engineering leverages each quality for thermal management, structural support and barrier function. Over a century of development has optimized aluminum foil to enable reliable delivery of key features through versatile tempering.
While soft and hard foils have different material properties, both can be produced in a variety of styles for special needs. These include pre-curled foils for easy folding, laminated foils with additional layers such as plastic or film to increase barrier or strength, and composite foils combined with other materials. Foils can also be produced in different colors through pigment addition or coating processes. A plastic-like draped appearance is achieved by using a layer of ultra-thin vapor-deposited aluminum on metalized foil.

Textured foils add workability - loose or wrinkled foils have a weaker structure which improves formability. Embossed or embossed foil includes punched patterns or indentations. The micro-perforated foils can be precisely punched with small holes to improve breathability for treatment or hygiene. cut and printed foil with industry or product logo. Production complexity ranges from simple raw foils to highly customized structured materials.
Sustainable practices span the aluminum industry. Most foil producers only source primary molten aluminum made from recycled scrap to achieve nearly zero virgin mining effects. Foreign matter is carefully sorted and removed from the foil stream to maintain the high circularity of the foil. Excess foil trims and scraps are recycled internally instead of being thrown away. Manufacturers promote consumer education about post-use recycling to continue the reuse of foils in various applications. The long-lasting properties of foils make both soft and hard foils uniquely suited to storage needs while minimizing environmental footprint.