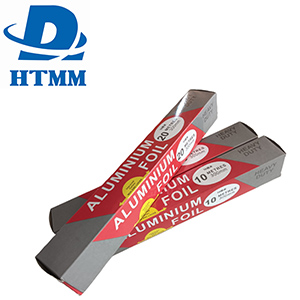
Usually more than 0.020 mm (20 microns) thick, heavy-duty aluminum foil is thicker than regular aluminum foil. Because of its increased thickness and strength, it can be used to wrap heavier objects and withstand higher cooking and baking temperatures. In addition to being a household essential, heavy-duty aluminum foil finds extensive use in industrial and food service settings.
Heavy-duty aluminum foil's primary characteristics are its thickness, which prevents it from tearing or puncturing and makes it perfect for wrapping meats and other large foods. Its ability to tolerate high temperatures is crucial for baking, roasting, and grilling. Food quality and freshness can be preserved by using heavy-duty aluminum foil, which acts as an effective barrier against air, light, and moisture. It has many uses, ranging from baking and cooking to packaging and storing food.
Naturally, aluminum is the primary raw material used to make heavy-duty aluminum foil. Packaging is one of the many uses for aluminum, a lightweight, corrosion-resistant metal that is widely used. Additionally, HTMM uses 99% aluminum ingots.
Bauxite, an ore mainly made of aluminum oxide, is the source of aluminum. There are two primary processes involved in turning bauxite into aluminum: first, the bauxite is refined into aluminum oxide, which is subsequently smelted to create aluminum metal. The earth's surface is mined for bauxite, which is mostly found in tropical and subtropical areas. Open-pit mining is typically used for the extraction process.
Refinement process: A processing step turns bauxite into aluminum oxide. In this procedure, the aluminum oxide is dissolved by crushing the bauxite and combining it with sodium hydroxide. Aluminum hydroxide is then precipitated after the solution has been clarified. Aluminum oxide is created by heating aluminum hydroxide.
It then undergoes smelting, which turns the aluminum oxide into aluminum metal using the Hall-Héroult process. To separate the aluminum from the oxygen, the aluminum oxide is dissolved in molten cryolite and then an electric current is run through it.
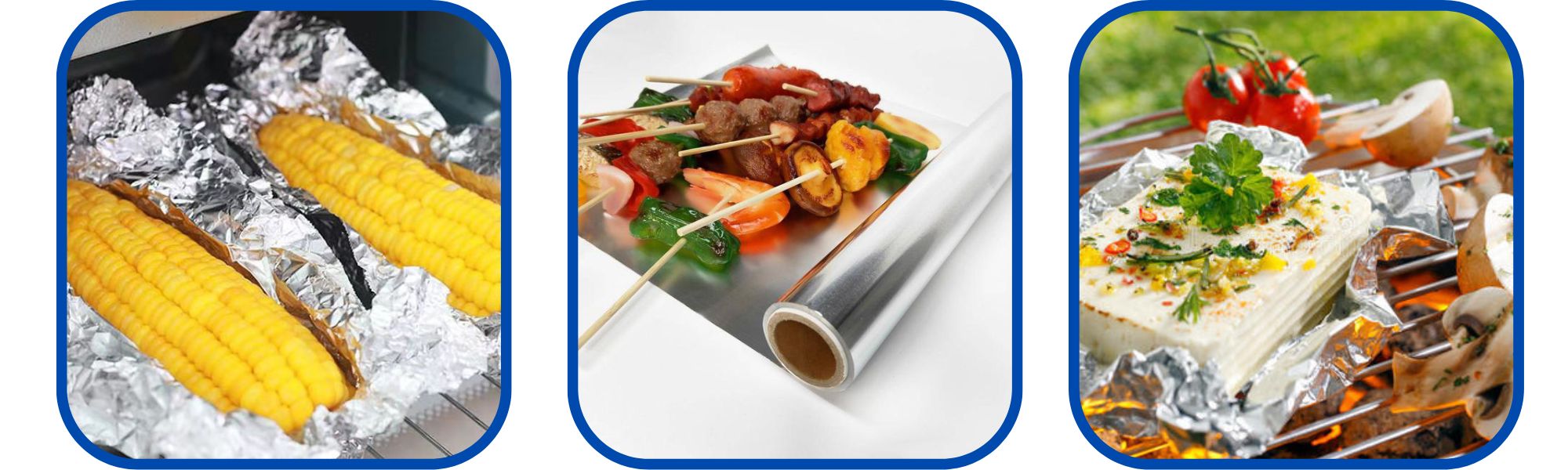
When making heavy-duty aluminum foil, the quality of the aluminum is crucial. Because it guarantees superior performance in terms of strength, flexibility, and barrier qualities, high purity aluminum is recommended. Although aluminum comes in a variety of grades, higher grades—typically 1100 or 1200 series aluminum—are typically utilized for heavy-duty aluminum foil due to its exceptional machinability and resistance to corrosion.
To improve its qualities, heavy-duty aluminum foil is made with a variety of alloying elements and additives in addition to pure aluminum. Alloying elements are among them. Magnesium is typically added to aluminum alloys to boost their strength and suitability for heavy-duty applications. Silicon: By increasing fluidity during the casting process, silicon can raise the foil's overall quality. Copper: Although copper can improve electrical and thermal conductivity, it is only used in very small amounts because it may compromise corrosion resistance.
Rolling and casting the aluminum ingots into thin sheets is the first stage in the HTMM manufacturing process for producing heavy-duty aluminum foil. To guarantee the quality of the metal, this process necessitates exact temperature control. The aluminum must be rolled after it has been cast into thin sheets. To attain the required thickness, the aluminum sheet is passed through a number of rollers during the rolling process. To get the right thickness, heavy-duty foil must go through rollers several times. The foil is annealed after it has been rolled.
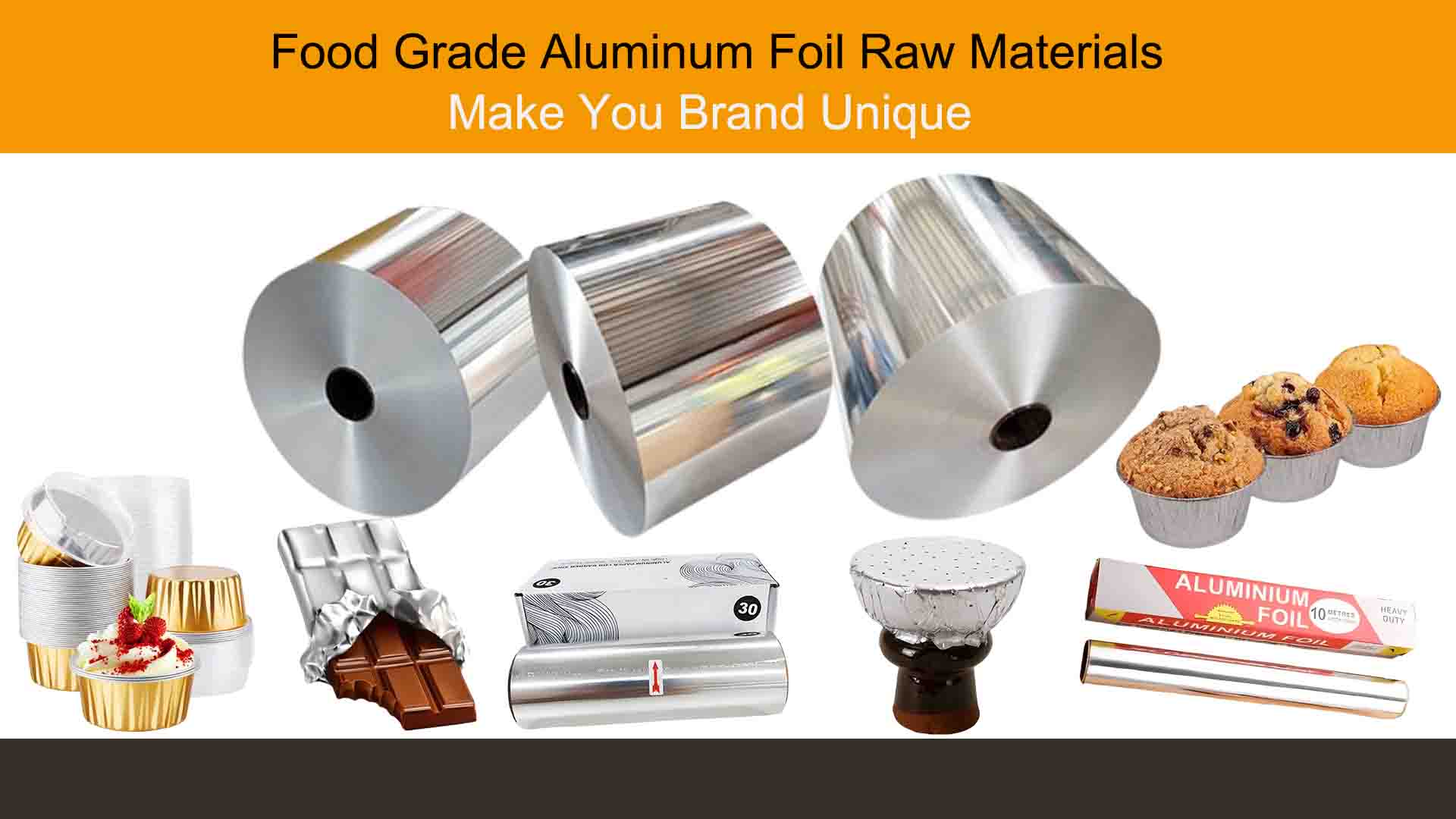
Heating the foil to a predetermined temperature and then gradually cooling it is known as annealing. By increasing the foil's ductility, this step improves its strength and facilitates processing. Depending on the needs of the market, the rolled and annealed foil is subsequently cut into different widths and lengths. The completed rolls are packaged for distribution to guarantee their safety during handling and transit.
HTMM's quality control in the production of heavy-duty foil is reflected in our strict adherence to international quality standards such as ISO 9001 to ensure the reliability of our product quality. After receiving an order from a customer, our factory will go through processes such as aluminum ingot processing, rolling, cooling, annealing, cooling, etc.
In the rolling process, our rolling mill uses HONEYWELL thickness control system and ABB plate control system, which can ensure that the entire rolling process provides customers with different thicknesses of aluminum foil. Quality control is an important aspect of heavy-duty foil production. Strict testing and inspection processes are implemented to ensure that raw materials and final products meet industry standards.
Important quality control procedures consist of Material Testing: Prior to being used in production, raw materials undergo testing to determine their physical characteristics, chemical makeup, and purity. Thickness Measurement: To guarantee uniformity and adherence to requirements, the foil's thickness is monitored during the manufacturing process.
Strength Testing: To make sure the finished product can endure the demands of use, the mechanical characteristics of the foil, such as its tensile strength and elongation, are examined. Barrier Testing: To guarantee food safety and quality, the foil's resistance to moisture, light, and oxygen is assessed.
Home kitchens are one of the many places that heavy-duty aluminum foil finds use. It is perfect for grilling vegetables, wrapping meats, and lining baking sheets. It helps keep food safe and fresh by acting as an efficient barrier for leftovers. It maintains food's freshness and warmth while in transit in the food service sector. It is utilized in packaging containers and prepared foods. In order to reflect heat and increase energy efficiency, heavy-duty aluminum foil is also utilized in a number of industrial sectors and construction materials. Because of its conductive qualities, it can be utilized as an insulating material for cables and connectors. Additionally, it can be utilized in the manufacturing of HVAC accessories and industrial tapes.
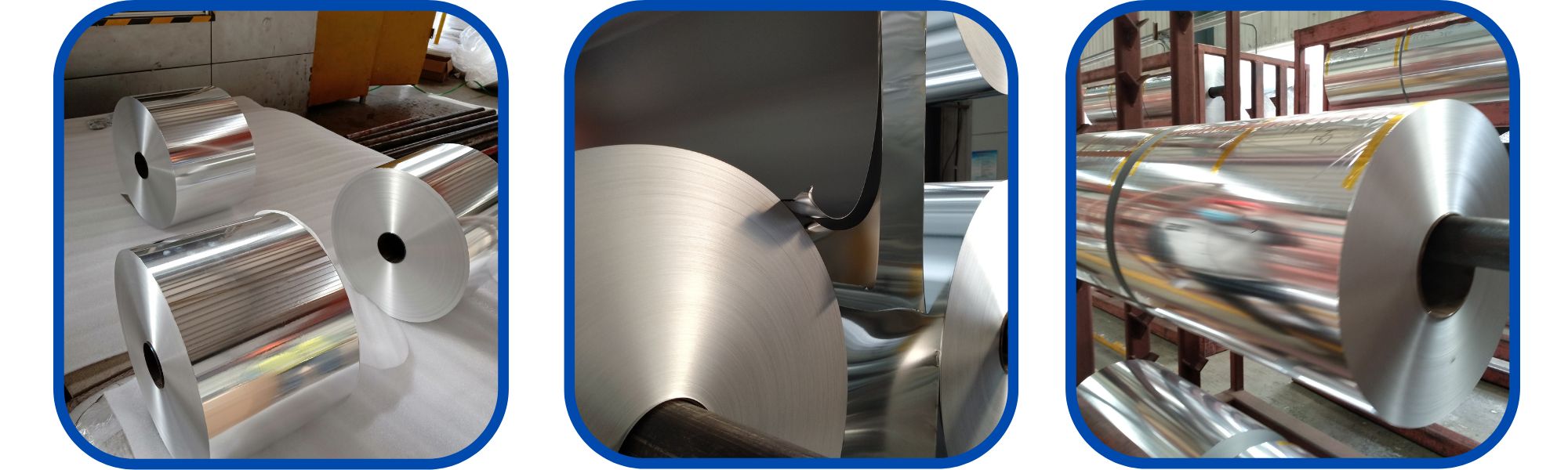
To comprehend the quality, functionality, and adaptability of heavy-duty aluminum foil, one must be aware of its raw materials. The main raw material, aluminum, goes through a rigorous production process that includes rolling, annealing, smelting, and refining. Because of its exceptional strength and barrier qualities, heavy-duty aluminum foil is still a crucial component in industrial settings, catering, and kitchens.
Customers can anticipate high-performing products that not only satisfy their needs but also help protect the environment as long as manufacturers maintain their focus on sustainability and quality assurance. To put it briefly, heavy-duty aluminum foil is a product of meticulous design and premium materials that make it more than just a kitchen necessity; it is an essential tool in our daily lives.