The production of aluminum foil from aluminum foil raw materials in our factory (HTMM) is a multi-step process, including casting, rolling, annealing, slitting and finishing, etc. Each stage helps transform aluminum ingots into thin, flexible and versatile materials that are widely used in various industries. The resulting aluminum foil has excellent barrier properties, heat resistance and flexibility, making it an important component in countless applications. Our factory has the most advanced production lines and cutting-edge technology, with an annual output of more than 80 million tons. We strictly adhere to international quality standards such as ISO 9001 to ensure the reliability of the quality of our products. Our rolling mill adopts HONEYWELL thickness control system and ABB plate control system, which can ensure that the entire rolling process can provide customers with aluminum foil of different thicknesses.
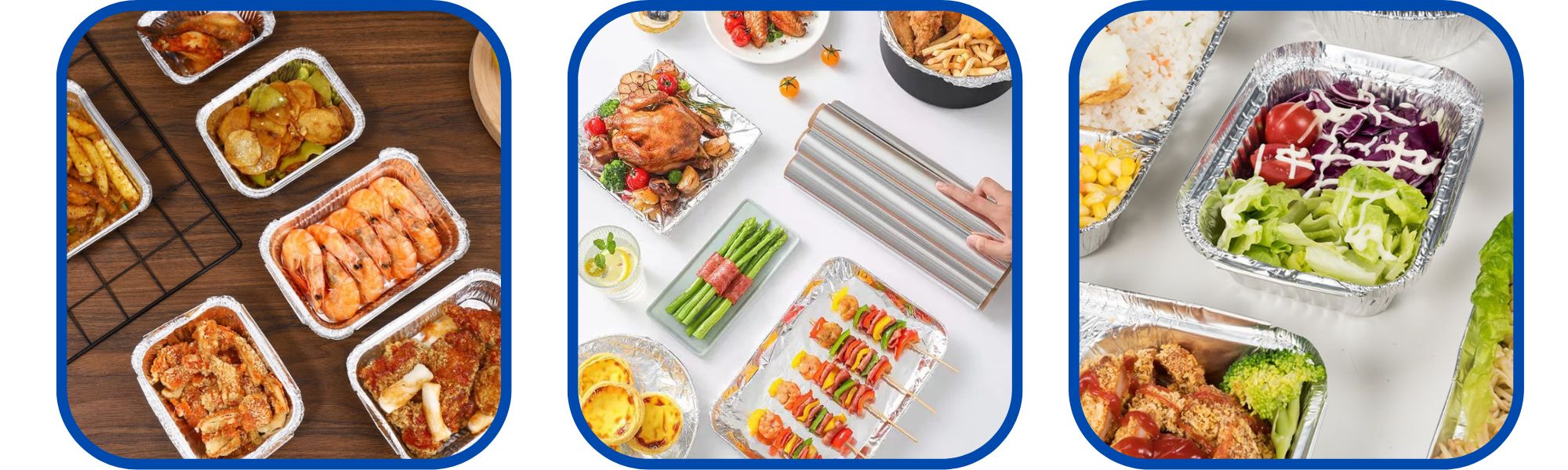
3003 aluminum foil raw material refers to aluminum foil made of 3003 alloy. This alloy is primarily composed of aluminum with a small amount of manganese. The combination of these elements gives the foil excellent strength, corrosion resistance and formability. Aluminum foil raw material 3003 is typically supplied in large rolls and can be further processed into various sizes and shapes for use in food container manufacturing.
The production of aluminum foil in our factory (HTMM) begins with the casting of aluminum ingots. These ingots are typically made from an aluminum alloy, which is a combination of aluminum and other elements to enhance the desired properties of the foil. Molten aluminum alloy is poured into a large flat mold called a slab. Once cooled and solidified, the plates are ready for the next step. The slab then passes through a series of rolling mills that gradually reduce the thickness of the slab. The rolling process involves multiple stages, with each mill applying increasing pressure to the slab, resulting in a gradual reduction in thickness. The slab is rolled several times until the desired thickness of the aluminum foil is reached. After the rolling process, the aluminum is annealed. Annealing is heating a metal to a specific temperature and then cooling it slowly. This step is crucial as it relieves internal stresses, increases the ductility of the foil, and improves its overall quality. The annealing process ensures that the foil is flexible and easy to handle without compromising its strength. Once the aluminum foil reaches the desired thickness and is annealed, it is cut into smaller rolls or sheets. Slitting machines are used to cut wide foil rolls into narrower widths depending on the intended application. This makes the handling and packaging of aluminum foil more efficient.
Our (HTMM) Aluminum Foil factory has third-party quality inspection certificates from Europe, the United States, SVHC, etc. These certificates can prove that our aluminum foil can be in good contact with food, and the quality of our aluminum foil fully complies with certain international food-grade aluminum foil standards. It can protect the health of food while preventing aluminum foil from causing harm to your body. And every batch of goods we produce will undergo strict quality inspection and control. We will conduct inspection procedures on the thickness, width, and quality of the aluminum foil to ensure that each batch of goods meets customer requirements. HTMM also values customer experience. We offer flexible MOQ, on-time delivery and multi-lingual customer service to build long-term partnerships with global buyers. All products are carefully packaged and shipped to ensure quality and safety.
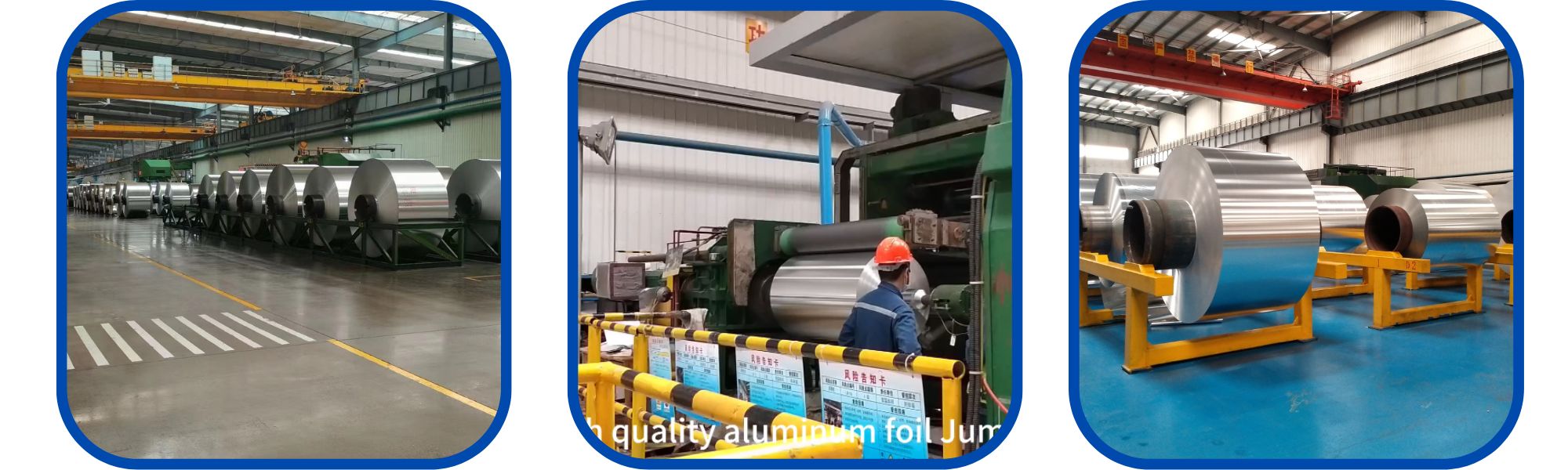
For food container foil, customers can use aluminum foil to make food dining boxes as well as dishes, plates, etc. We can provide customers with aluminum foil alloys 8011, 3003, 8006, alloy states O, H22, H24, etc. Our hot-selling alloy states are 3003, H24. Because the surface state of 3003 alloy is more corrosion-resistant than the surface state of 8011. H24 state is softer than H22 state,
H22, H18 surface condition is too hard, so we recommend customers to buy 3003, H24 alloy condition. The width purchased by the customer should be determined according to their own feeding machine. Different customers require different widths. We can provide you with oiled container foil and non-oiled container foil. If your machine has an oiling function, we recommend you to buy an unoiled container foil. If your machine does not have an oiling function, , we recommend you purchase oiled container foil. When you are making aluminum foil lunch boxes, you must apply oil on the surface of the aluminum foil, because this can prevent the surface of the aluminum foil from being damaged, improve efficiency, and protect the mold on the machine.
Aluminum foil raw material 3003 is made of pure aluminum, ensuring that there are no impurities that may contaminate the food stored in the container. Foil effectively blocks moisture, light, oxygen and other contaminants, thereby maintaining the freshness and quality of food. Aluminum foil raw material 3003 has excellent thermal conductivity and can evenly heat and cook food in the container. Foil can be easily formed, folded and molded into a variety of container shapes without compromising its integrity or structural strength. Aluminum foil is highly recyclable, making it an environmentally friendly choice for food packaging.
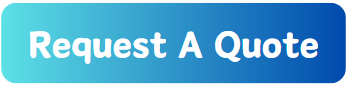
3003 aluminum foil rolls are widely used in the food packaging industry, especially in the manufacture of food containers. It exists in our daily lives. Take-away containers, for example, are widely used in the manufacture of disposable take-out containers for restaurants, fast-food chains and catering services. Convenient, lightweight and easy to seal, these containers are ideal for transporting and storing food. Second Baking and Roasting, 3003 aluminum foil roll is ideal for lining baking sheets, trays and pans, preventing food from sticking and ensuring even heat distribution during baking or roasting. Tertiary aluminum foil is often used to wrap food items such as meats, vegetables, and leftovers before freezing or storing in the refrigerator. It acts as a barrier against frostbite and helps maintain the quality of food. There are also many prepackaged ready-to-eat meals packaged in 3003 aluminum foil containers. These containers are microwave safe, making it easy to reheat food directly in the container. And aluminum foil containers made of 3003 aluminum foil rolls are widely used in catering services for events, parties and gatherings. They provide a hygienic and convenient way to serve and transport large quantities of food.
Aluminum foil raw material 3003 is a versatile and efficient material used in the production of food containers. Its distinguishing features include high purity, excellent barrier properties, thermal conductivity and recyclability, making it ideal for preserving and protecting food. Whether it is takeout containers, disposable food containers, bakery packaging, ready-to-eat meals or catering events, aluminum foil raw material 3003 provides reliable solutions to ensure the freshness and quality of food. Consider aluminum foil raw material 3003 for your food container production needs and experience the advantages it offers.