What is 8011 H24 Aluminum Foil?
8011 H24 aluminum foil is an alloy composed primarily of aluminum along with a small percentage of manganese and magnesium. The 8011 designation refers to the Aluminum Association's coding system for aluminum alloys, with 8x11 indicating the major alloying elements of manganese and magnesium.
The "H24" indicates the temper or condition of the 8011 Aluminum Foil. "H" refers to the cold rolling process used to work-harden and strengthen the metal, while "24" signifies the minimum yield strength of the alloy in units of ksi (thousands of pounds per square inch). For 8011 H24 aluminum, this translates to a minimum 0.2% offset yield strength of 24 ksi.
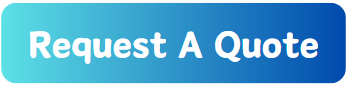
In terms of its physical and chemical properties, 8011 H24 Aluminum Foil has:
A density of around 2.7 g/cm3, making it very lightweight.
High strength-to-weight ratio for its applications. The cold working and aging process imparts excellent strength.
Excellent corrosion resistance due to a thin natural oxide layer that forms on the aluminum surface.
Moldability - it can be easily formed into a variety of shapes through processing like rolling, drawing and stamping.
Barrier properties that help protect foods from moisture, gases and odor transmission.
100% recyclable at the end of its use-life through aluminum recycling programs.

Raw Material Processing for Single-Use Dishes
As a raw material, 8011 H24 Aluminum Foil Container Roll l undergoes several manufacturing processes to transform it into finished single-use dish products:
Foil Production: The aluminum alloy ingots are first melted down and continuously cast into thin coils. These coils are then cold rolled to the desired thickness, usually around 0.2 mm for foodservice applications.
Slitting & Re-Coiling: The large coils are slit into narrower rolls suitable for further processing on stamping lines. Precise width control is important.
Leveling: Any imperfections or curl from roll processing are removed through tension leveling.
Coating: Some Aluminum Foil Container Roll may receive barrier coatings like plastic or wax to improve impermeability properties as needed.
Stamping: High-speed mechanical presses or progressive dies shape the Aluminum Container Raw Material Manufacturers into dishes, trays, clamshells, etc through a blanking and forming process.
Edge Treatment: Sharpened or crimped edges improve rigidity and durability of the formed parts.
Inspection & Packaging: Quality is checked before automated packaging and palletizing of the finished dish products.
Key Attributes for Single-Use Applications
There are several material attributes that make Aluminum Container Raw Material Manufacturers well-suited as a raw material for producing single-use dishes through the above manufacturing route:
Lightweight and Formable - At around 60% the weight of steel or stainless foils, aluminum is easy to form complex dish shapes without excessive thinning. The 0.2 mm thickness keeps weight low.
Corrosion Resistance - Aluminum's natural oxide layer protects foods from reaction and provides a safe packaging medium compliant with food safety regulations.
Rigidity - Cold working and H24 temper gives the foil adequate bending strength and stiffness for manufacturing rigid clamshells, trays and similar products.
Barrier Properties - Aluminum helps protect food from gases, moisture, odors and bacterial infiltration better than some plastic films. Additional coatings can further enhance performance.
Forming Properties - The foil easily blanks and forms sharply at high speeds without issues like work hardening like seen in stainless steel. Dies have long runs.
Recyclable - Post-consumer aluminum packaging is one of most recycled materials, favoring its sustainability profile versus plastics.
Economical - With widespread production infrastructure, aluminum offers a cost-effective solution versus other metal foils or molded fiber alternatives.
Aesthetics - An attractive shiny or printed surface promotes brand image and consumer appeal compared to waxed cardboard or other board-based dishes.
Dimensional Stability - The temper and alloying elements impart good stability and rigidity at elevated oven temperatures if applicable for foodservice use.
Chemical Resistance - Products like chips, nuts and baked goods packaged in aluminum foil dishes are well protected from corrosion or reaction issues.
Biofilms - Studies show aluminum inhibits biofilm formation versus plastics that can harbor bacteria. This aids food safety during storage, warming or reheating of foods.
Barrier performance also protects against transmission of odors, off-flavors and even potential allergens like gluten when packaging a variety of foods.
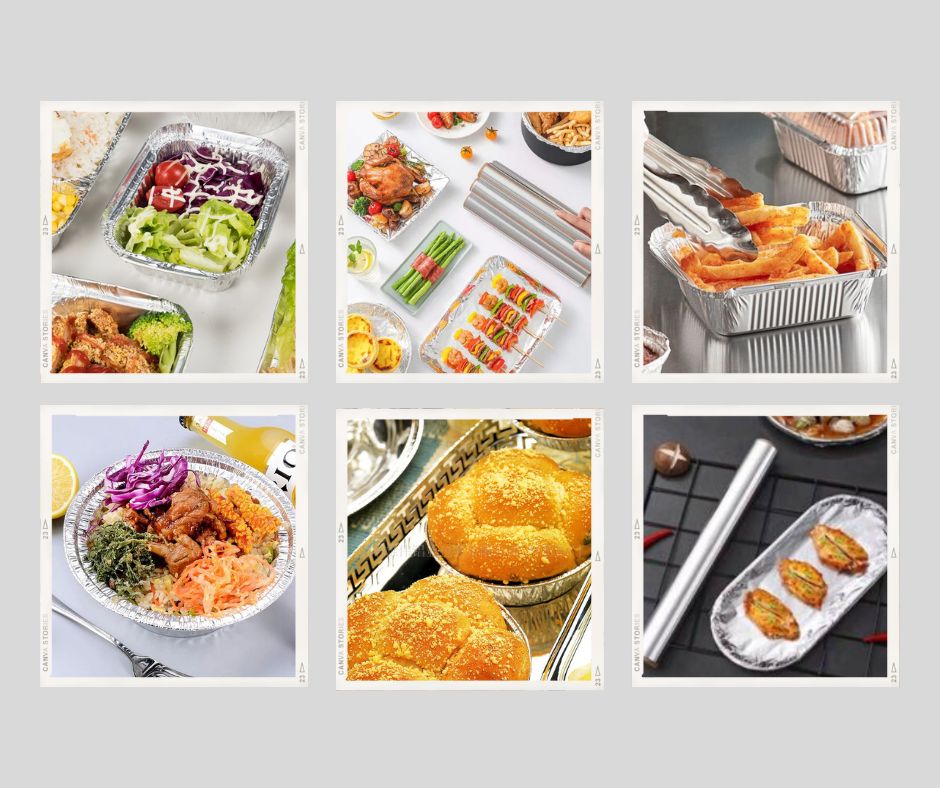
Economics of 8011 H24 Aluminum Processing
From a commercial perspective, 8011 H24 aluminum foil provides an economical raw material solution for high-volume single-use dish production:
Mature Infrastructure - Aluminum rolling, coating, stamping and fabrication technologies are optimized for large throughputs.
Mass Production Scalability - Lines can stamp thousands of dishes per minute in a compact footprint. Production can flex up or down quickly versus custom tooling solutions.
High Yield - Ultra-thin blanking and forming produces almost no scrap metal, improving material utilization rates.
Tooling Economy - Dies for basic dish shapes have long runs before replacement versus steel that work hardens rapidly.
Raw Material Pricing - As a commodity material, aluminum prices fluctuate less severely than special steel or plastic resin prices. They are also more stable long-term.
Recyclability - Post-consumption scrap is remelted, minimizing waste and landfill burden versus many non-recyclable alternatives.
Package to Pallet Logistics - Lightweight aluminum minimizes transport energy use versus heavier materials like coated paperboard.
Branding Compatibility - Surface printing, coating and finishing options support product identification, messaging and shelf appeal.
Regulatory Compliance - Aluminum meets all food safety and packaging material standards globally. It poses no known health risks when used as intended.
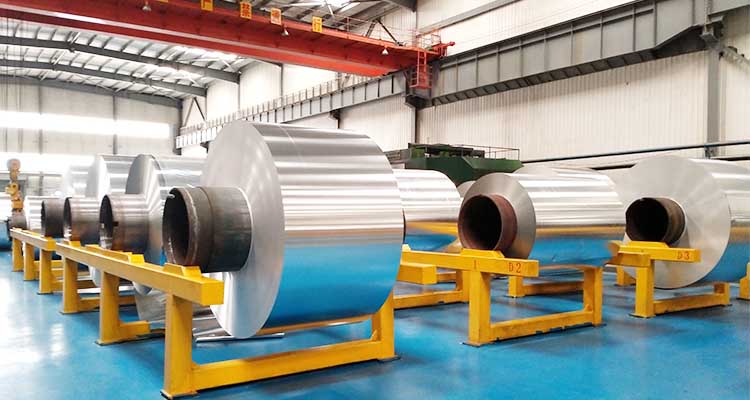
Prominent Applications for 8011 H24 Aluminum Dishes
Given its attributes, 8011 H24 aluminum foil finds application producing popular single-use dish formats including:
Foodservice Clamshells - Used at restaurants, delis, food courts for a la carte items, value meals and more. Common sizes range 6-16 ounces.
Retail Food Trays - Found at grocery deli counters, prepared foods sections for packaging sliced meats, salads, food bar items for home consumption.
Bakery & Snack Trays - Perfect for portioning muffins, pastries, snack mixes, candies and trail mixes for in-store bakery sections or vending machines.
Home Meal Kits - Multi-compartment aluminum trays are ideal for pre-portioned recipe meals delivered to home cooks.
Chinese Food Containers - Standard aluminum containers in a range of sizes from 4-16 ounces serve for takeout and delivery Chinese cuisine.
Single Serving Containers - Smaller 1-4 ounce containers package individual condiments, salad dressings, sauces, butter packs and more.
Crisp Trays - Shallow pans accommodate snack crisps, potato and tortilla chips and minimize breakage during transport.
Frozen Food Trays - Microwavable or ovenable aluminum trays quickly and evenly cook frozen pizzas, meals, appetizers without melting.
With a shelf life often shorter than plastic or glass containers, aluminum dishes cater well to “fast metals” food categories prioritizing convenience, portion control and value. Their disposalcompatibility also plays into the sustainability goals of many quick-service restaurants.