
Aluminum foil is commonly referred to as tin foil in everyday speech. The HTMM manufacturing offers a variety of thicknesses for request. Composite foil typically has a thickness of 6–30 microns. It is renowned for having exceptional barrier properties, which make it ideal for packaging delicate items like food and prescription drugs. The thickness of aluminum foil has a significant impact on how it is used. Thinner aluminum foil is more flexible, while bigger aluminum foil provides greater protection. The HTMM facility has the most advanced manufacturing lines and modern technology. We constantly follow international quality standards like ISO 9001 to ensure the dependability of our product quality.
Our factory will process, anneal, cool, and roll aluminum ingots, among other things. To ensure that clients receive different thicknesses of aluminum foil throughout the rolling process, our rolling mill uses the ABB plate control system and the HONEYWELL thickness control system. We will use a range of rolling processes to produce multilayer foil items with thinner thicknesses. We provide the thinnest 6mic composite foil. Furthermore, we will assess the quality of every batch of products that HTMM manufactures for customers using sampling procedures. Our committed R&D team is committed to continuous product innovation and customized solutions. Because creating green operations is in line with our fundamental objective of sustainability.
A particular alloy composition with at least 99.35% aluminum is 1235 alloy aluminum foil. It has outstanding conductivity, corrosion resistance, and ductility because to its high purity level. Because of its formability and flexibility, 1235 alloy is frequently used in composite foil for flexible packaging and lamination.
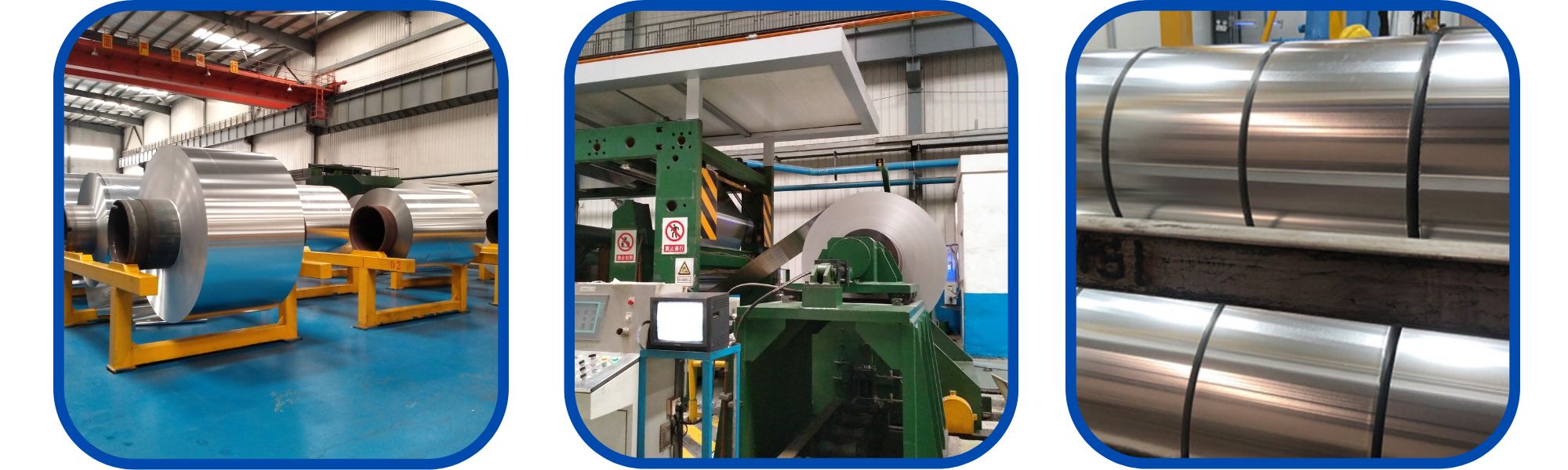
The main use for 7 micron-thick composite foil is in laminated bags for food and beverage packaging. One important application for 7-micron foil is lamination. Using wet or dry lamination processes, the foil's soft, smooth surface makes it easy to cling to other substrates. Common laminates include foil film laminates, aluminum-polymer-aluminum composites, and paper-aluminum-paper sandwiches (PAP).
The foil layer serves as an effective moisture and grease barrier and decorative element for the finished laminated product, which includes food packaging, home packaging, pouches, and other packaging films. Thinner foils, such as 7-micron foils, are commonly used for flexible packaging because they easily conform to the contour of the item being packaged and provide a tight fit that enhances protection.
Aluminum foil is a common material for flexible packaging because of its excellent barrier properties. Aluminum foil effectively prevents oxygen, light, and moisture—the three main factors that lead to food degradation and rotting. Superior barrier properties provided by rolls of 7-micron aluminum foil ensure that the product being packaged will maintain its quality and freshness for a long time. Aluminum foil is suitable for packaging items with irregular forms since it can be adapted to a variety of sizes and shapes.
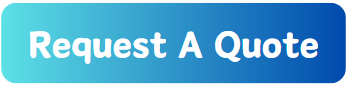
With a 7 micron thickness, aluminum foil provides manufacturers with a cost-effective choice. Because of its excellent barrier properties, less material is needed to give the same degree of protection as conventional packaging materials. This can significantly reduce waste and save raw material costs. As consumers and businesses place a greater focus on sustainability, aluminum foil's environmental friendliness is a huge asset. Flexible packaging manufactured with 7-micron aluminum foil encourages a circular economy since aluminum can be recycled 100% of the time. Businesses may attract environmentally conscious clients by emphasizing eco-friendly packaging.
Using aluminum foil for lamination has the following benefits: Laminating packaging materials using aluminum foil makes them tougher and more resistant to tearing and punctures.
When used for lamination, aluminum foil enhances the overall barrier properties of the packaging and provides greater protection for the goods. The shiny surface of aluminum foil makes the laminated product look more expensive and makes it more appealing to consumers.
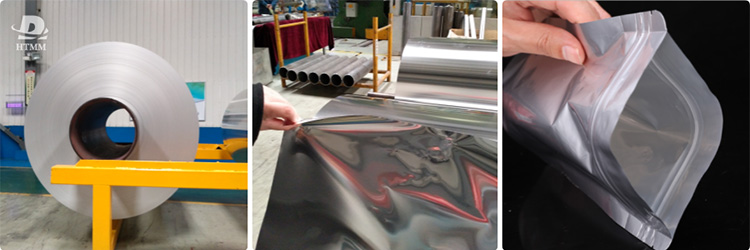
When selecting aluminum foil for flexible packaging or lamination, several factors need to be taken into account:
Thickness: The thickness of the aluminum foil has a big impact on how well it works. For most applications involving flexible packaging, the kind of alloy distinct aluminum alloys have distinct qualities. The recommended aluminum foil is 1235 because to its excellent purity and remarkable formability. composed of an alloy mostly composed of aluminum (Al) with traces of iron (Fe) and silicon (Si).
The composition of aluminum alloys greatly influences their characteristics and applicability for different uses. Composite packaging commonly uses aluminum alloys 8011 and 8079, both of which belong to the 8xxx family. They are well known for having a high tensile strength and remarkable corrosion resistance. The makeup of the three, however, varies somewhat. The 8011 aluminum alloy has a higher tensile strength than the 8079 aluminum alloy.
8011 is hence more appropriate for applications needing greater strength and resistance to deformation. The elongation of the 8079 aluminum alloy is larger than that of the 8011 alloy. Elongation is the capacity of a substance to stretch without breaking. This feature makes 8079 alloy more appropriate for applications like packaging material firms where ductility and flexibility are essential. The surface condition of the 1235 alloy is better than that of the 8011 and 8079 alloys.
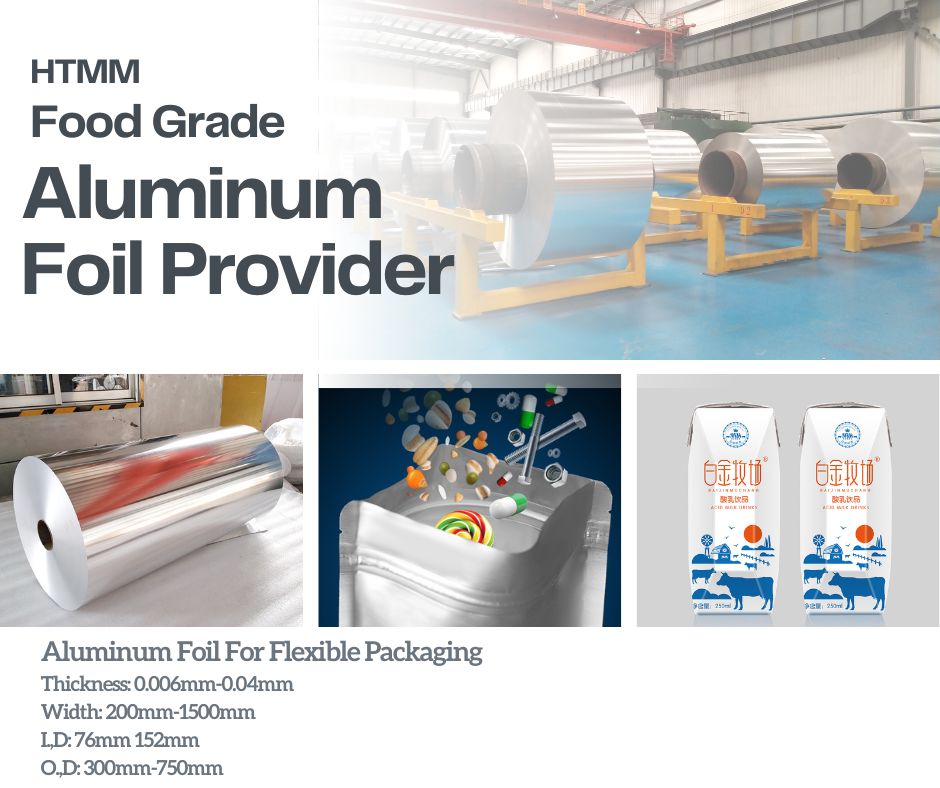
Rolls of 7 micron aluminum foil, especially 1235 aluminum foil, are necessary for the flexible packaging and laminating industries. Because of its remarkable barrier properties, lightweight design, and versatility, it is ideal for a wide range of applications, including flexible packaging for food and liquids. As sustainability gains popularity, aluminum foil's recyclable and environmentally friendly qualities will only make it more appealing in the packaging sector.
Manufacturers that want to benefit from aluminum foil's benefits for flexible packaging should consider the unique properties of 7 micron aluminum foil rolls. By doing this, they can ensure that their products remain fresh, safe, and appealing to consumers. Maintaining a competitive advantage in the packaging industry as the market shifts requires being abreast of the most recent advancements in aluminum foil technology.