How to made heat sealing aluminum foil?
Aluminum metal is used to make aluminum foil for heat sealing. It performs well in terms of gas and moisture resistance as well as heat insulation. It primarily warms and seals the package using a heat-sealing device while in operation, and then it creates a seal. packaging to shield the contents from contaminants including air, moisture, and scents. Aluminum foil jumbo roll is used extensively in many sectors for heat sealing because of its great qualities.
The typical manufacturing procedure for aluminum foil alloy 8011 for heat sealing is casting and rolling. A typical method for producing aluminum foil roll jumbo is casting and rolling.
The aluminum alloy material is first melted and then cast into the shape of an aluminum sheet or strip. Aluminum foil 8011 alloy has been alloyed to provide it exceptional flexibility, hardness, and heat resistance making it appropriate for heat sealing needs. The needed sheet of aluminum foil big roll is then created by rolling the aluminum sheet or strip repeatedly in hot, cold, and annealing procedures for plastic deformation and thickness control. The aluminum foil is also rolled and annealed numerous times during the rolling process to acquire the necessary thickness, hardness, and surface quality to satisfy the demands of customer.
We may alter the structure and properties of the material throughout the casting and rolling process to satisfy our requirements for heat-sealed packaging. In order to enhance the heat sealing effect and printing, the casting and rolling processes may also guarantee the flatness and glossiness of the aluminum foil surface. Our consumers should be aware that when purchasing heat-sealing aluminum foils, we must pick the right product specifications and performance based on the unique packaging needs. Heat-sealing aluminum foils have many of characteristics and requirements.
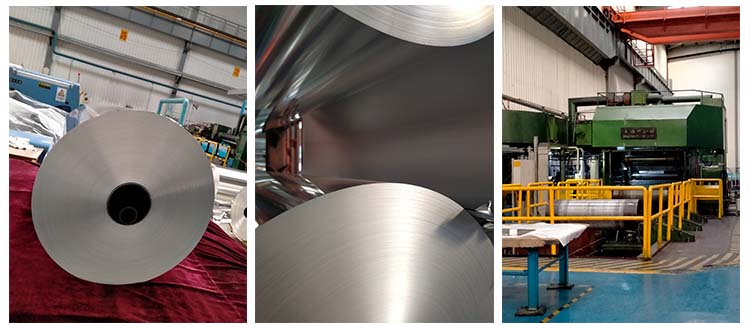
How to use heat sealing aluminum foil?
First, heat sealing using large rolls of aluminum foil is a common practice in food packaging. The oxidation and contamination of food brought on by light, oxygen, water vapor, unusual aromas, and other things can be successfully stopped by the heat-sealing aluminum foil. especially for products that are prone to oxidation in our everyday lives, such coffee, chocolate, and almonds in their exterior packaging.
Food manufacturers heat seal aluminum foil jumbo rolls to extend the shelf life and maintain the excellent quality of the product. Aluminum foil may be used for heat sealing in addition to preventing the flavor and nutrients in the food from degrading. so that consumers may enjoy delicious and wholesome flavors while dining.
Second, aluminum foil jambo reel is widely used in the pharmaceutical industry for heat sealing. Pharmaceuticals have a significant negative impact on the environment since they are susceptible to environmental factors including moisture, temperature, and light. However, pharmaceutical firms may effectively protect their goods from the environment by employing aluminum foil for heat sealing, maintaining the stability and potency of the items.
We have also seen in practice that heat-sealing aluminum foil, particularly in some drug-filled packages, may successfully seal the seal, restrict the volatilization and oxidation of pharmaceuticals, and enhance the efficacy and safety of medications.
Thirdly, aluminum foil that is heat-sealed is often used in the packaging of a variety of products that are vulnerable to environmental factors, such as electronics and cosmetics. For instance, using aluminum foil for heat sealing helps prevent the oxidation, volatilization, and contamination of sensitive active compounds used in cosmetics. The heat insulation and static-shielding capabilities of aluminum foil for heat sealing aid to reduce static electricity accumulation and protect electronic equipment.
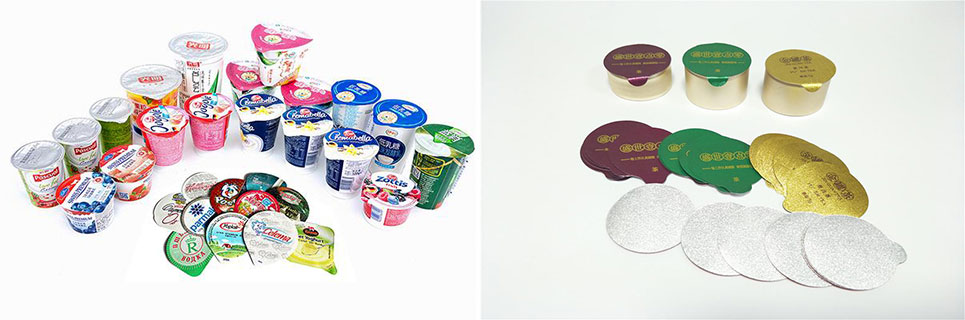
Heat sealing Aluminum Foil Application
The production floor supervisors check the heat sealing machine's temperature and pressure before they begin their job and confirm that the product within the foil pouch or container is within the necessary temperature range. In order to guarantee that the foil completely covers the goods and secures its tightness, employees flatten, fold, and place the foil in accordance with the shape and size of the package. The product is then placed on the folded foil in the crucial next step, aligned with the sealing region of the heat-sealing apparatus such that the heat and pressure of the sealing apparatus seals the foil to the container or bag around the product.
Ased on the needs of the sealing machine, the kind of foil, and the product, factory workers establish the ideal sealing time and temperature. Our clients must pay close attention to this phase. Typically, the temperature ranges from 100 to 180 degrees Celsius, and the sealing period ranges from one to three seconds. The workers in our manufacturing workshop should inspect the sealing once it has been sealed in order to make sure it is totally airtight and to look for any evident damage. If an issue is discovered, it must be fixed quickly.
Temperature control: When employees utilize aluminum foil for heat sealing, temperature control is crucial. Lower temperatures may lead to flimsy or even impossible sealing, while higher temperatures may cause the foil to stretch, melt, or become damaged. Therefore, it is crucial to manage the sealing temperature sensibly in accordance with the unique needs of the aluminum foil for heat sealing and the articles to be sealed.
1. Controlling pressure is important because it affects how well aluminum foil heat seals. Applying exactly the appropriate amount of pressure to the aluminum foil and the item being sealed will result in a strong and airtight seal. The quality and efficacy of the seal will be harmed by too much or too little pressure, thus the workers in the production workshop must also adjust and control as needed.
2. During the process, the sealing time, which controls how long the heat-sealing machine applies heat and pressure, takes place. How well the production workshop staff can manage the sealing phase will have a direct impact on the firmness and completion of the sealing. A seal that develops too quickly could not be functional, whereas one that does so gradually might generate excessive heat, distortion, or damage. It should go without saying how crucial it is to set the sealing time properly.
3. Cup surface treatment: The sealing effect will also be directly influenced by the cup's surface treatment. The sealing might not produce the ideal result we hoped for if the surface of the cup is too unclean, as in the case of oil, dust, or other pollutants. Workers must thus make sure the surface of the cup body is clean, dry, and pollutant-free before sealing.
4. Aluminum foil should completely enclose the area that has to be sealed off and have the ideal size and form to snugly fit around its edge. The protective function would be diminished by an insufficient seal or insufficient seal hardness caused by improper aluminum foil covering location or size.
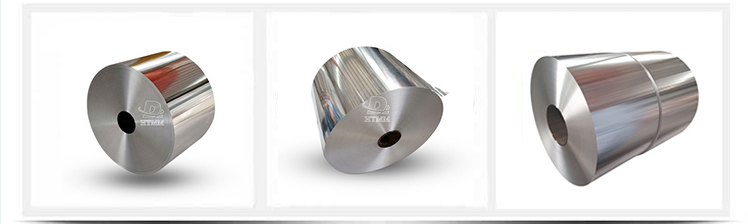
HTMM is a professional bare aluminum foil jumbo roll manufacturer . The aluminum foil we produce is a food -grade. bare aluminum foil jumbo roll has been authenticated by the US FDA certification test. have also passed EU ROHS and SVHC tests.Pure aluminum foil jumbo rolls are applied to home kitchen, making food container , soft flexible packaging, industrial use.