Aluminum conversion foil is a unique kind of aluminum foil made especially for making laminated tubes. It is a premium material that is thin, flexible, and goes through several steps to get the necessary qualities. Conversion foil serves fundamental purposes and offers advantages as a crucial part of laminated tubes. Its primary function is to serve as a barrier material to keep the tube's contents safe from impurities, moisture, light, and oxygen. Throughout its shelf life, aluminum foil guarantees the integrity and quality of the packed goods. High-grade aluminum is typically used to make conversion foil, which has superior barrier qualities. Aluminum foil is frequently combined with other layers, including polyethylene, to produce laminate structures that are more durable and useful.
The following factors mostly show how laminated tube conversion foil is used. First off, the cosmetics sector uses laminated tubes extensively to package creams, lotions, serums, and other beauty items. By shielding these goods from the elements—such as light, moisture, and air—conversion foil helps preserve their integrity and lengthens their shelf life. Laminated tubes with conversion foil are also commonly used in the pharmaceutical business to package creams, gels, and ointments. The foil serves as a barrier to keep impurities out and preserve the medicinal product's effectiveness.
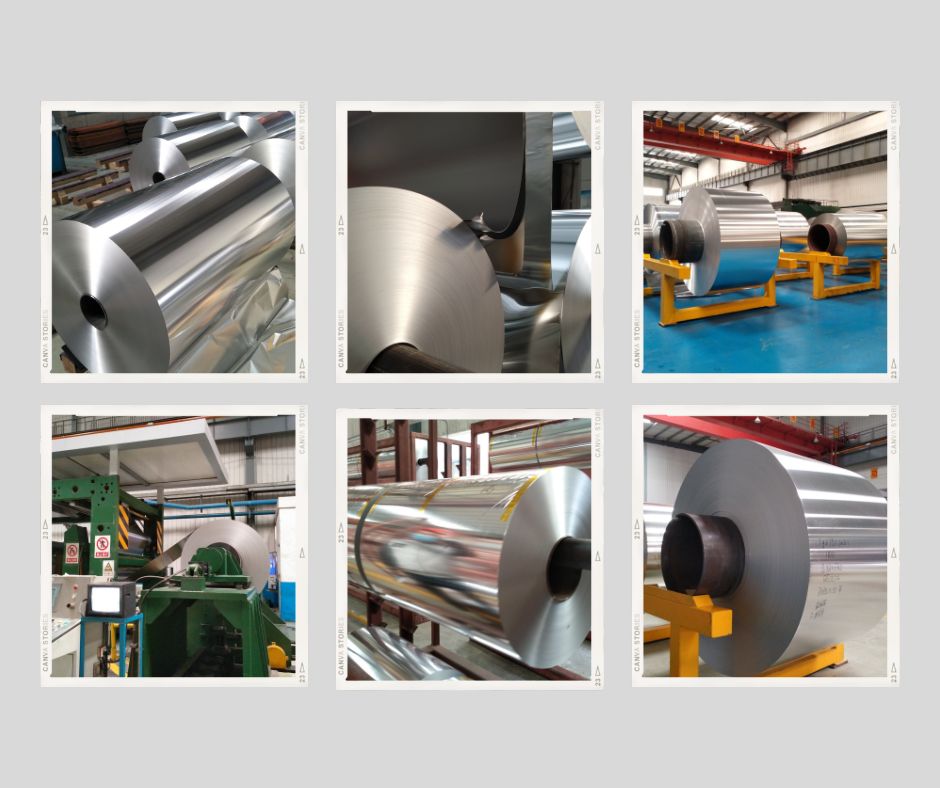
The food business can also employ laminated tube conversion foil. Packaging sauces, pastes, and other condiments is a common usage for it. The food is kept fresh and of high quality because the foil serves as a barrier to light and air.
There are several applications for conversion foil, and its superior barrier qualities are among its key benefits. It serves as a shielding layer to keep off moisture, air, and UV radiation from entering the tube. This barrier makes the packed product acceptable for a range of uses, including perishable foods, by preserving its flavor, freshness, and effectiveness. Because of its extreme flexibility, conversion foil is simple to modify to fit the size and form of the laminated tube. This makes it possible to produce tubes with unique forms, sizes, and shapes to satisfy the demands of various goods and sectors. The foil's formability guarantees a smooth integration into the tube production process.
Additionally, conversion foil has a high heat resistance, which makes it appropriate for items that need to be sterilized at high temperatures. This guarantees the commodities that are packaged are safe and hygienic, which is important in the food and pharmaceutical sectors. Additionally, customers may quickly and simply print vibrant and striking graphics, logos, brand components, and product details on its surface. This makes it possible to communicate with customers more effectively, build brand recognition, and design aesthetically pleasing package solutions.
The thickness of conversion foil in laminated tubes typically falls inside a predetermined range. Conversion foil for laminated tubes typically has a thickness of 20–40 microns (0.02–0.04 mm). This range permits flexibility and formability in the tube-making process while yet offering the required barrier qualities. It is important to remember that the precise thickness might change based on a number of variables, including the particular product being packaged, industry standards, and consumer preferences. Conversion foils for some applications could need to be thinner or thicker, depending on the amount of protection needed, product compatibility, and overall package specifications.
The customer's needs, the type of the packed goods, and the laminated tube's performance requirements ultimately determine the conversion foil thickness.
Customers' normal widths for conversion foil will also differ based on the industry in which it is utilized and their unique needs. Conversion foil typically comes in widths between 200 and 1,000 mm (8 to 40 inches) for laminated tubes. This series provides versatility to suit various production methods and tube diameters. The number of tubes to be produced each run, the intended tube diameter, and the equipment capabilities of the customer's manufacturing setup all influence the choice of width.
Our factory conversion foils (HTMM) may be tailored to match the unique requirements of our clients. Certain manufacturers could need broader or smaller widths due to specific equipment constraints and production needs. In order to guarantee the best possible performance and efficiency in the manufacturing of laminated tubes, the client and the foil provider usually work together to select the width of the conversion foil.
We advise consumers to utilize 8011 alloy when it comes to conversion foil. Aluminum alloy 8011 is the most common alloy that consumers use for conversion foil. Since aluminum alloy 8011 has great qualities and is suitable for conversion procedures, it is frequently utilized in packaging applications. The wrought aluminum alloy Alloy 8011 is renowned for its exceptional strength, excellent formability, and resistance to corrosion. Due to its ability to conform to the size and shape of the tube during the production process, these qualities make it the perfect option for conversion foils used in laminated tubes.
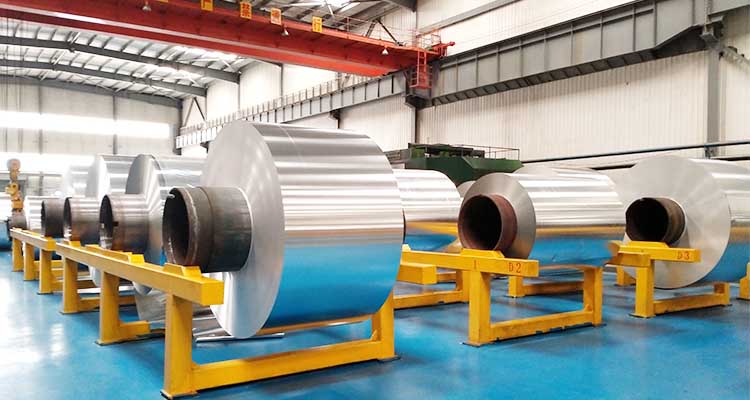
Furthermore, Alloy 8011 possesses strong barrier qualities, which are critical for shielding the contents of laminated tubes from outside influences including moisture, oxygen, and light. It aids in preserving the product's quality, freshness, and integrity when it is packaged. Alloy 8011 may also be readily printed on conversion foil to create vibrant graphics, branding elements, and product information because it is compatible with a wide range of printing and surface treatment techniques. This improves the packaging's ability to communicate ideas visually and verbally.
For laminated tubes to be useful, durable, and protected, aluminum conversion foil is essential. Food, medicine, and cosmetics are just a few of the industries that find it to be a top option due to its exceptional barrier qualities, flexibility, heat resistance, and printability. Manufacturers may enhance the look and feel of their items while guaranteeing the security and contentment of their customers by utilizing conversion foil.