Heavy gauges in the range of 0.1-0.2mm are versatile enough for numerous types of containers while balancing cost. They permit conventional folding or drawing without the risk of cracking. Some processes like deep drawing benefit from 0.15-0.2mm which withstands higher deformation forces without creasing or cracking. Very thick gauges closer to 0.2mm can even be fluted, corrugated or pleated to maximize strength per surface area. Of course, the use of materials becomes less efficient above this point. Throughout the Aluminium Foil Container Roll thickness spectrum, rigorous quality control ensures that the Aluminium Foil Container Roll roll maintains the uniform and defect-free surface essential for multi-cavity forming operations.
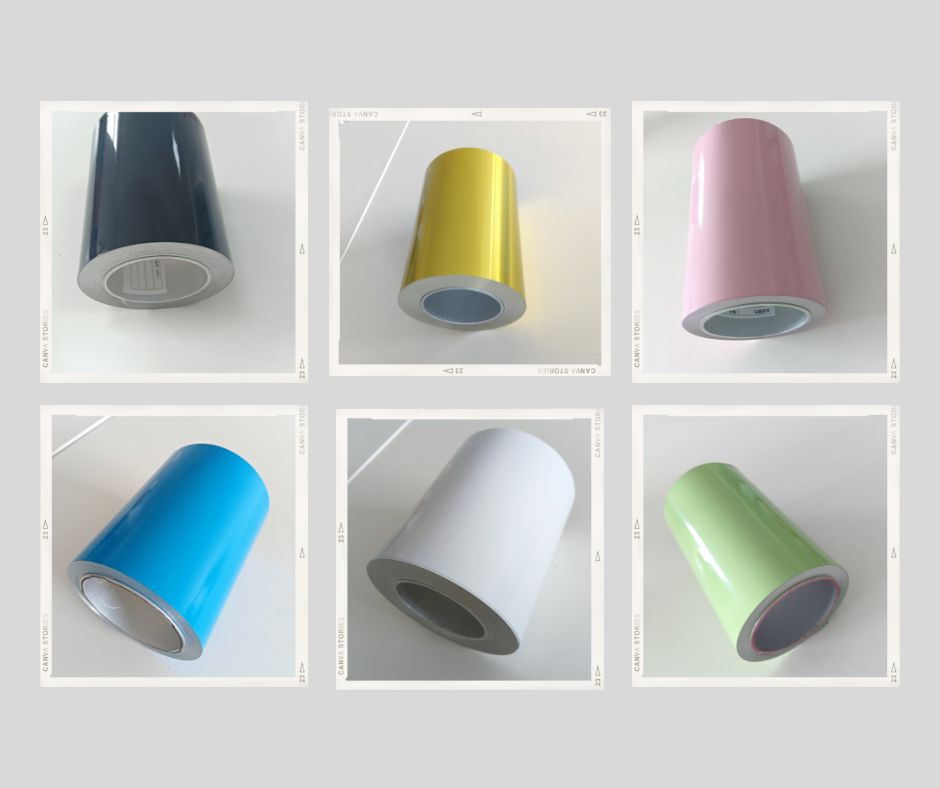
By judiciously tailoring the thickness of Aluminium Foil Container Roll , packaging designers unlock new container solutions. Biomimetic geometry mimics the lightweight structural strength of nature. Downgauging enables a reduction in the size of the product footprint. Clever shapes like blister packs use every square inch efficiently. Each incremental improvement increases sustainability by reducing material requirements. The infinite recyclability of aluminum and the vast global recycling infrastructure play a key supporting role by establishing a circular supply chain following the use of the recovered foil. Ongoing advancements within the value chain will maintain the role of aluminum foil as a premium packaging substrate.
Innovations in recycling and resource recovery have increased closed loop capabilities for foil-based packaging and containers. The new pyrolysis technique uses heat under low oxygen conditions to disperse the mixed waste stream to a pure secondary feedstock such as high purity aluminum. When combined with advanced sorting technologies optimized for multi-material identification, these solutions increase recycled content uptake. Recycling organizations partner directly with major consumer brands to develop packaging with minimal barrier coatings that simplify separation and reprocessing.
Government policy also plays a role in supporting the sustainable role of aluminium. The regulations establish definitions for recyclable or compostable claims to provide clear guidance. Subsidies for domestic remelting capacity reinforce national self-sufficiency. Goals outlining minimum post-consumer content and recycled packaging ratios encourage circular design innovation from manufacturers. Harmonization of global standards streamlines cross-border recycling. And initiatives like corporate recycled manufacturing pledges or landfill bans on recoverable materials spur more collaborative action throughout the value chain.

The combination of progressive market innovation and enabling policy frameworks cements aluminum foil’s position as an eco-friendly substrate for containers worldwide. Its innate recyclability and versatile structure characteristics meet a variety of packaging needs both now and in future closed-loop economies. Continued collaboration across industries will optimize every stage from design to restoration. This strengthens the essential function of aluminum in sustainably supporting global commodity safety for generations to come.
Aluminium Foil Container Roll is widely used in packaging applications due to its unparalleled barrier properties, versatility and sustainability. Produced on advanced rolling lines of 20-150 micron thickness, aluminum foil lends itself well to high-speed forming of numerous container configurations. Its corrosion resistance and printable surface allow for vibrant graphics while protecting content. Tough yet lightweight, foil serves as an effective gas and moisture barrier to extend the shelf life of food, pharmaceuticals and consumer products.
Improvements in rolling and lamination technology improve production efficiency. Near-zero gap casting furnaces reduce contaminants for food contact to 99.995% purity. Multilayer co-extrusion laminates foil with thin plastic film at 300+ m/min. Inline corona treatments and adhesive coatings improve performance. Digital CAD interfaces directly integrate complex die designs with high-speed presses. Artificial intelligence is used for predictive quality control in process models. Such process innovations translate into large cost savings that support the competitive pricing of aluminum.
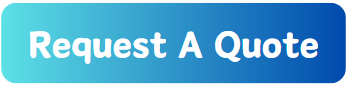
Designers take advantage of the possibility of new structures to minimize material consumption. Biomimetic geometry mimics natural cellular solids for strength with fewer foils. Downgaging preserves critical barrier features where geometric features provide additional protection. Complex die shape maximizes roll width conversion. Embossing substitutions and interactive printing activate engagement without additional substrate. The clever “living hinge” design enables new configurations. When combined with improved recycling disposal, these improvements cement the important environmentally-efficient role of aluminum foil in premium packaging worldwide.
Continuous innovation optimizes the transformation and recycling of 50 micron aluminum foil into sustainable containers. New pyrolysis techniques facilitate the separation of compostable coatings. Investment in domestic remelting reinforces security of supply. Brand partnerships target designs that optimize high recyclability rather than complex multi-component structures. The regulation encourages a minimal and coherent global definition of post-consumer content.
Overall, aluminum foil’s unmatched barrier properties, lightweight strength and endless recyclability cement its critical function in global packaging applications well into the future. Ongoing collaborative improvements within the value chain serve to further optimize its sustainable credentials and endless benefits for premium product safety.
Advances in printing technology have expanded the possibilities for 50 micron aluminum foil as an interactive medium. Digital decor adds immersive brand narratives, dynamic graphics and even sensory responses without extra substrate. Variable content tailors information to individual markets or customer demographics. Time-temperature indicators provide verification of cold-chain integrity. Embedded near-field communication tags trigger augmented reality or allow item tracking throughout the supply chain. These strategies elevate packaging beyond simple safety to an attractive brand building platform.
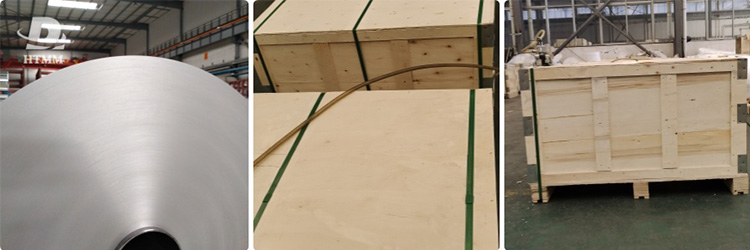
The new solutions also target better recycling logistics. The AI-enabled sorting system helps in precise identification and separation of foil-based structures from post-consumer waste streams using features such as elemental structures and electromagnetic signatures. Deinking improvements remove adhesive residues and inks to produce recycled Aluminum foil jumbo roll suitable for food contact applications. Regional scrap banks promote local collection and remelting networks for manufacturers. Initiatives that encourage design foresight toward disassembly optimize product recovery in future decommissioning. Harmonization of global standards further streamlines the flow of goods across borders.
The combination of continuous manufacturing, design, and end-of-life innovation positions aluminum foil with unmatched sustainability credentials. As the demand for climate-friendly packaging solutions intensifies, Aluminum foil jumbo roll’s versatility, strength and closed-loop circularity ensure its essential role responsibly supporting global product safety now and for generations to come. Ongoing collaboration across industries will optimize every step from concept development to material reuse.