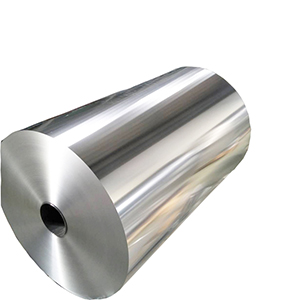
Cast and wrought aluminum alloys are the two primary varieties. The alloys 1235 and 8079, which belong to the 1 and 8 series, respectively, are included in the wrought category. This suggests that they are produced via mechanical processes like rolling and forging. Each alloy has unique properties that make it suitable for specific applications.
The two main types of aluminum alloys are cast and wrought. The wrought category includes the alloys 1235 and 8079, which are classified into the 1 and 8 series, respectively. This indicates that mechanical procedures like rolling and forging are used in their production. Every alloy has distinct qualities that make it appropriate for particular uses.
Made of alloys composed mainly of aluminum (Al) and small amounts of other elements such as iron (Fe) and silicon (Si). 8079 aluminum alloy exhibits higher elongation than 1235 aluminum alloy. Elongation refers to the ability of a material to stretch without breaking. The surface condition of 1235 alloy is better than that of 8079 alloy aluminum foil.
With a minimum aluminum content of 99.35%, 1235 aluminum foil is distinguished by its exceptional purity. Because of its high degree of purity, it has exceptional electrical conductivity and formability, which makes it perfect for a range of uses. Excellent electrical and thermal conductivity is guaranteed by the high aluminum content of 1235 aluminum foil, which is its primary characteristic. Many companies use this kind of aluminum foil because it is often less expensive to produce than other alloys.
The 8079 alloy differs from the 1235 alloy in its chemical composition. With very small amounts of alloying components, aluminum makes up the majority of 1235 alloy. The 8079 alloy's properties are enhanced by a mix of copper, aluminum, and other elements. 1235 aluminum foil and 8079 alloy foil are well-known in the flexible packaging industry for their softness, flexibility, ease of handling, and compatibility with a variety of materials.
The chemical makeup distinguishes the 8079 alloy from the 1235 alloy. Aluminum makes up the majority of 1235 alloy, with extremely minor quantities of alloying components. A combination of copper, aluminum, and other components improve the qualities of the 8079 alloy. In the flexible packaging sector, 1235 aluminum foil and 8079 alloy foil are renowned for their softness, flexibility, ease of handling, and suitability for a range of materials.
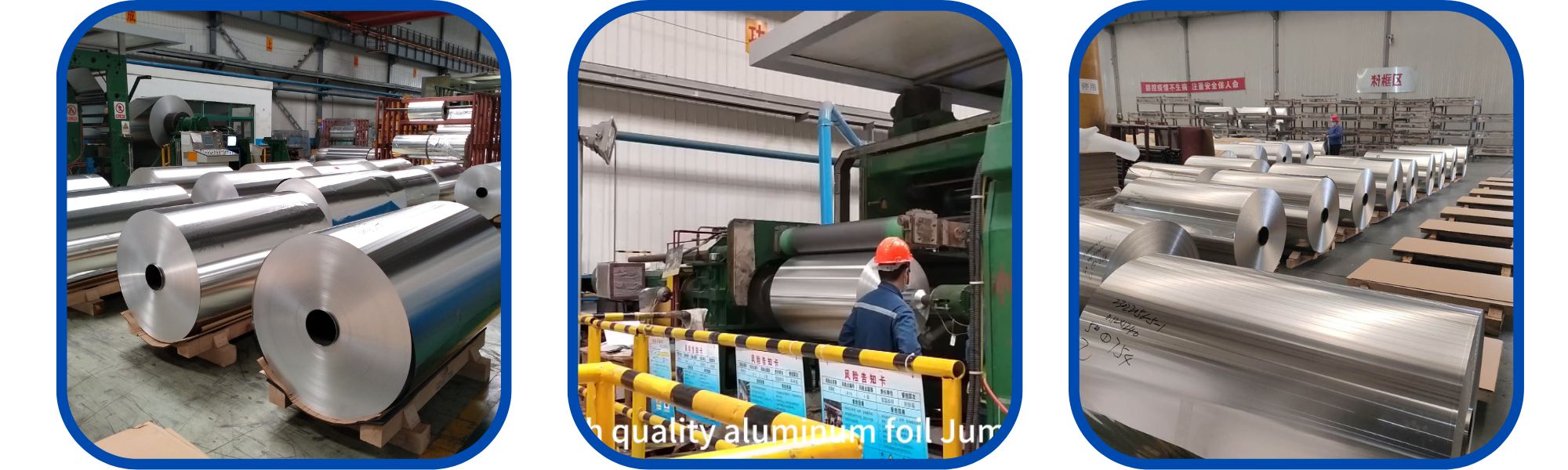
Although the 1235 alloy has strong barrier qualities, it performs worse than the 8079. In addition to having outstanding barrier qualities, 8079 alloy may offer superior protection against light, moisture, and gases. According to economic considerations, 8079 alloy is more expensive than 1235 alloy since it has more elongation and superior softness.
Because aluminum foil itself has barrier qualities and is resistant to oxidation and moisture, 8079 alloy and 1235 alloy composite foil may be employed in a variety of flexible packaging sectors. It is frequently utilized in the field of flexible packaging as one of the composite materials. Manufacturers of packaging will mix aluminum foil with PE, PET, PP, and other materials to create flexible packaging bags, self-supporting bags, liquid beverage packaging boxes, snacks, and quick meals. They may also mix aluminum foil with paper to package sandwiches, hamburgers, and other items. We encounter these packing items on a daily basis.
Aluminum foil is a popular option for food packaging because of its special qualities. It ensures that food stays fresh by fitting tightly and creating an efficient seal. It helps to keep food fresh by limiting its exposure to moisture and air. This is particularly crucial for foods that spoil quickly. Additionally, it keeps aromas and smells from transferring from one dish to another, guaranteeing that each item has its own flavor. Packaging makers can pick between 1235 and 8079 alloys depending on the kind of bag they are making. For liquid packaging boxes, our clients often use 8079 alloy, and for food packaging bags such stand-up bags, zipper bags, cooking bags, etc., 1235 and 8079 will be chosen.
A substance that is often used in daily life, aluminum foil is also a necessary raw material for the food and pharmaceutical sectors. By efficiently blocking light, oxygen, and moisture, aluminum foil can help keep the goods in its packaging from going bad. In the food and pharmaceutical sectors, where preserving freshness and quality is crucial, this is particularly crucial. The product's shelf life can be considerably increased by using aluminum foil in the packaging.
Aluminum foil preserves food's taste, texture, and nutritional content by keeping it out of the air and moisture. Because aluminum foil packaging is lightweight and manageable, both producers and consumers find it to be a convenient option. It may be utilized in a range of packaging configurations, including trays and bags, and is simple to make and seal.
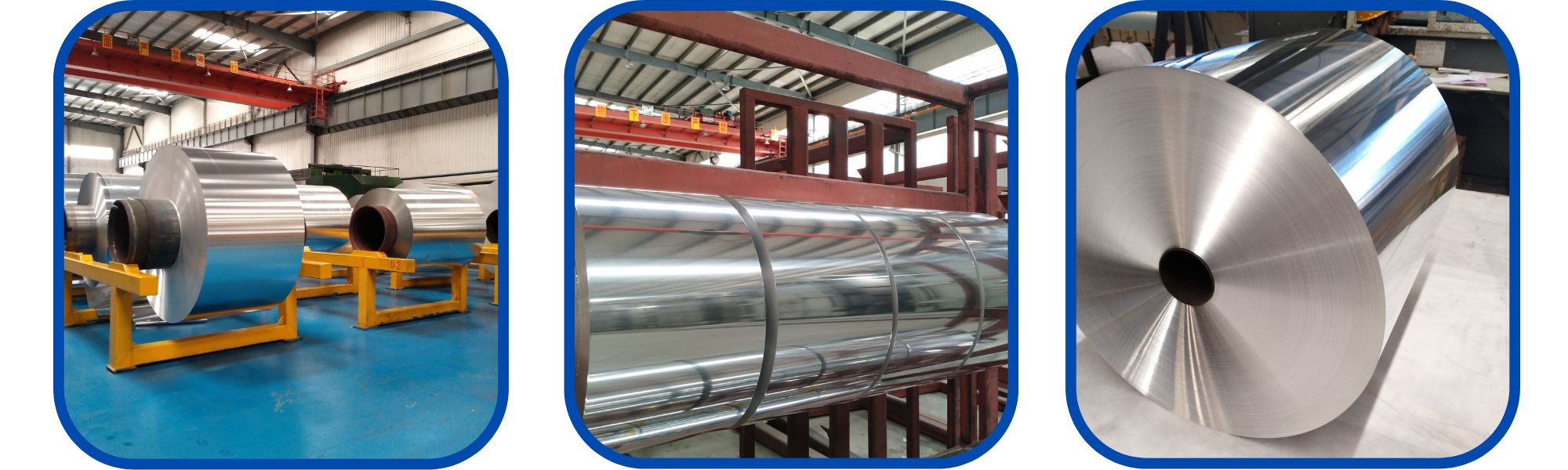
Innovation in aluminum foil packaging is at the forefront of emerging trends in the ever-evolving packaging business. Although it is more expensive to produce high-quality aluminum foil than alternative packaging materials, aluminum foil is nevertheless a necessary component of the food and pharmaceutical sectors.As one of the most reliable aluminum foil wholesalers, HTMM is able to provide a stable supply of high-quality 8079 alloy and 1235 alloy aluminum foil. We can provide customers with 1 series alloys and a full range of 8 series and 3 series alloys. Custom production is provided to customers. When you have any aluminum foil needs, you can look to us to provide you with the best quality alloy aluminum foil.
In conclusion, 1235 and 8079 aluminum foils each have special qualities that allow them to be used in various ways. The strength and barrier qualities of 8079 aluminum foil are superior to those of 1235 aluminum foil, which is renowned for its excellent purity, flexibility, and affordability.
Making wise choices in packaging and other applications requires an understanding of the distinctions between these two alloys. You may efficiently select the ideal aluminum foil to satisfy your demands by taking into account the particular requirements of your project.